Deck 11: Criticisms of Absorption Cost Systems: Inaccurate Product Costs
Question
Question
Question
Unlock Deck
Sign up to unlock the cards in this deck!
Unlock Deck
Unlock Deck
1/3
Play
Full screen (f)
Deck 11: Criticisms of Absorption Cost Systems: Inaccurate Product Costs
Describe ABC
Required:
a.What is activity-based costing and how does it differ from traditional absorption costing?
b.Describe the advantages and disadvantages of activity-based costing systems.
Required:
a.What is activity-based costing and how does it differ from traditional absorption costing?
b.Describe the advantages and disadvantages of activity-based costing systems.
Solution to Describe ABC (15 minutes)
An ABC system provides a finer partitioning of indirect costs than absorption costs and a different way of assigning these costs to products.Indirect costs are broken into batch-level processes,product-line processes,and all others (production sustaining).These buckets are not allocated directly to units produced using a volume-related measure but rather are assigned using the cost driver most closely associated with how costs vary in each bucket (e.g. ,number of batches,number of products,number of part numbers).These costs may or may not be allocated to the unit level,but usually are.The distinction between ABC and absorption costing is that the latter allocates all costs using a unit-based volume measure.ABC allocates batch and product line costs using non-unit-based volume measures.
Advantages:
more accurate product costs for decision making
focus managers' attention on the "true" cost drivers
Disadvantages:
costly to implement
costly to operate
organization problems might increase if ABC systems provide less control
Since few firms use ABC for internal and external reporting one must question whether for the typical production setting the benefits exceed the costs (i.e. ,apply the parable of the marmots and the bears).
An ABC system provides a finer partitioning of indirect costs than absorption costs and a different way of assigning these costs to products.Indirect costs are broken into batch-level processes,product-line processes,and all others (production sustaining).These buckets are not allocated directly to units produced using a volume-related measure but rather are assigned using the cost driver most closely associated with how costs vary in each bucket (e.g. ,number of batches,number of products,number of part numbers).These costs may or may not be allocated to the unit level,but usually are.The distinction between ABC and absorption costing is that the latter allocates all costs using a unit-based volume measure.ABC allocates batch and product line costs using non-unit-based volume measures.
Advantages:
more accurate product costs for decision making
focus managers' attention on the "true" cost drivers
Disadvantages:
costly to implement
costly to operate
organization problems might increase if ABC systems provide less control
Since few firms use ABC for internal and external reporting one must question whether for the typical production setting the benefits exceed the costs (i.e. ,apply the parable of the marmots and the bears).
ABC and Average Cost in a Service Industry
For many years the Honey Lake Summer Camp had used the number of campers per week to estimate weekly costs.The summer camp is open for ten weeks during the summer with a different number of campers each week.July is busiest with June and the end of August least busy.Costs from the last week of summer camp in 1998 are used to estimate costs for 1999 for pricing purposes.The following costs occurred during the last week of 1998 and the costs of each cost category are expected to be the same for 1999:
Cost per camper:$12,200/50 campers = $244/camper
The Honey Lake Summer Camp expects 75 campers during the second week of July.
Required:
a.What is the expected cost of that week using the average cost?
b.What is the expected cost of that week using ABC?
For many years the Honey Lake Summer Camp had used the number of campers per week to estimate weekly costs.The summer camp is open for ten weeks during the summer with a different number of campers each week.July is busiest with June and the end of August least busy.Costs from the last week of summer camp in 1998 are used to estimate costs for 1999 for pricing purposes.The following costs occurred during the last week of 1998 and the costs of each cost category are expected to be the same for 1999:
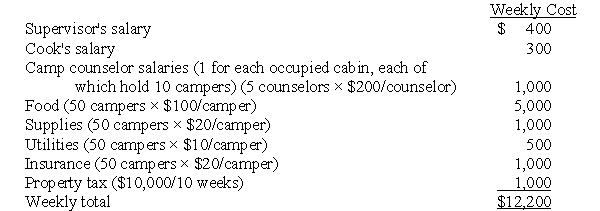
The Honey Lake Summer Camp expects 75 campers during the second week of July.
Required:
a.What is the expected cost of that week using the average cost?
b.What is the expected cost of that week using ABC?
Solution to ABC and Average Cost in a Service Industry (20 minutes)
a.The average cost per camper using last year's last week of camp is $204/camper.The total expected cost using that average cost is:
(75 campers)($204/camper)= $15,300
b.ABC recognizes how the costs would change with different uses of activities and changing numbers of campers.In particular: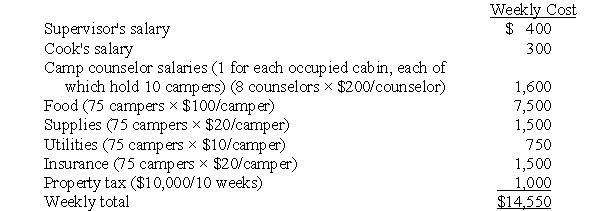
a.The average cost per camper using last year's last week of camp is $204/camper.The total expected cost using that average cost is:
(75 campers)($204/camper)= $15,300
b.ABC recognizes how the costs would change with different uses of activities and changing numbers of campers.In particular:
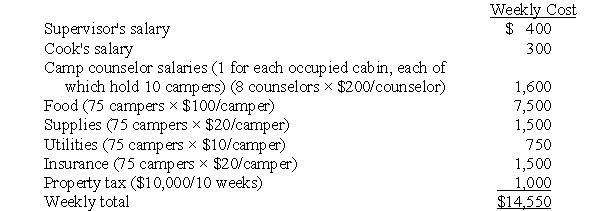
Different Overhead Allocation Bases
Set-Up Company produces blue things and gray things.Blue things are in much greater demand in the market and the firm sells 120,000 blue things a year.Set-Up Co.sells 6,000 gray things per year in small boutiques.Things have a short shelf life.They must be distributed,sold,and consumed within two months of manufacture.
Both things use the identical production process and production facilities.Direct labor is $0.50 per thing and direct material is $0.50 per thing.Things are produced in batches.Blue things are produced in batches of 600 units and gray things in batches of 30.Each batch of things goes through the thingamajig,which is the machine that converts raw inputs into things.Each batch requires engineers to reset the machine for the next batch,calibrate settings,and test the first 10 things for product quality and conformity to standards.Even if sequential batches of the same things are made,setups must be performed for each new batch.All the overhead costs are incurred in setups.Indirect labor,indirect materials,and supplies consumed during setup cost $360,000 per year.The only costs of producing things are direct labor,direct materials,and the overhead of setups.The company is currently allocating setup costs to things based on direct labor cost.
The firm has been selling blue things for $4 per unit and gray things for $6 per unit.But foreign competition for blue things is starting to put pressure on the $4 price.Some competitors are selling blue things for as low as $3 per unit.Management is considering putting more emphasis on selling gray things,whose margins are higher.On the other hand,management worries that the current system for allocating overhead costs is misrepresenting the costs of the two products because direct labor costs are not representative of the time spent by each product on the thingamajig.Management is considering allocating setup costs using machine hours on the thingamajig.A batch of gray things requires one hour of machine time and a batch of blue things requires 20 hours of machine time.
Required:
Analyze the present situation.Is there anything wrong with the costing system? If so,should management change to the proposed allocation base of machine hours?
Set-Up Company produces blue things and gray things.Blue things are in much greater demand in the market and the firm sells 120,000 blue things a year.Set-Up Co.sells 6,000 gray things per year in small boutiques.Things have a short shelf life.They must be distributed,sold,and consumed within two months of manufacture.
Both things use the identical production process and production facilities.Direct labor is $0.50 per thing and direct material is $0.50 per thing.Things are produced in batches.Blue things are produced in batches of 600 units and gray things in batches of 30.Each batch of things goes through the thingamajig,which is the machine that converts raw inputs into things.Each batch requires engineers to reset the machine for the next batch,calibrate settings,and test the first 10 things for product quality and conformity to standards.Even if sequential batches of the same things are made,setups must be performed for each new batch.All the overhead costs are incurred in setups.Indirect labor,indirect materials,and supplies consumed during setup cost $360,000 per year.The only costs of producing things are direct labor,direct materials,and the overhead of setups.The company is currently allocating setup costs to things based on direct labor cost.
The firm has been selling blue things for $4 per unit and gray things for $6 per unit.But foreign competition for blue things is starting to put pressure on the $4 price.Some competitors are selling blue things for as low as $3 per unit.Management is considering putting more emphasis on selling gray things,whose margins are higher.On the other hand,management worries that the current system for allocating overhead costs is misrepresenting the costs of the two products because direct labor costs are not representative of the time spent by each product on the thingamajig.Management is considering allocating setup costs using machine hours on the thingamajig.A batch of gray things requires one hour of machine time and a batch of blue things requires 20 hours of machine time.
Required:
Analyze the present situation.Is there anything wrong with the costing system? If so,should management change to the proposed allocation base of machine hours?
Solution to Different Overhead Allocation Bases (40 minutes)
In this problem,there are three possible overhead allocation bases: direct labor (present system),machine hours (the proposed system),and number of batches.First,calculate product costs under each of the three allocation schemes:
1.Direct labor cost as the allocation base (present system):
2.Machine hours as the allocation base (proposed system):
3.Number of batches as the allocation base:
Notice that allocating overhead by either direct labor or machine hours produces identical product costs.Thus,the proposed system change will not affect decision making.
There are two cost drivers in Set-up Company.Unit volume drives direct materials and direct labor,but set-ups (number of batches)appear to drive overhead costs.Allocating overhead using direct labor gives an incorrect impression of how overhead costs vary and distorts product costs.Overhead costs are incurred in set-ups.While run times per unit of thing is the same for blues and grays,batch sizes vary considerably.In fact,bluethings and graythings each required 200 batches.Therefore,each product line (as opposed to each unit of product)should be allocated an equal dollar amount of overhead.If this is done,then graythings become massive losers and bluethings are seen to be profitable,even with market price of $3 per unit.
But these allocated costs using number of batches still do not necessarily represent opportunity costs.If the thing-a-majig and set-up crews are not operating at full capacity,then the opportunity cost of a batch of graythings is $30 (just variable cost).However,if the firm is reducing the number of bluethings it can produce to make graythings (production is at capacity),then the opportunity cost of a graything is the forgone margin on a batch of bluethings plus the variable costs of the graythings.Or,
The decision to continue to make graythings depends on i)how overhead costs vary with batches and ii)whether additional bluethings can be sold if graythings are not produced.If the size and cost of the set-up crew is invariant to the number of batches,then direct labor is probably not too bad an allocation base.If more bluethings cannot be sold,again it is not optimum to drop graythings.Graythings are covering variable cost.Just because all overhead costs are incurred in set-ups does not make set-up costs variable with number of batches.Some of the overhead costs are sunk costs and do not vary with batches (e.g. ,depreciation of the "thing-a-majig").
In this problem,there are three possible overhead allocation bases: direct labor (present system),machine hours (the proposed system),and number of batches.First,calculate product costs under each of the three allocation schemes:
1.Direct labor cost as the allocation base (present system):
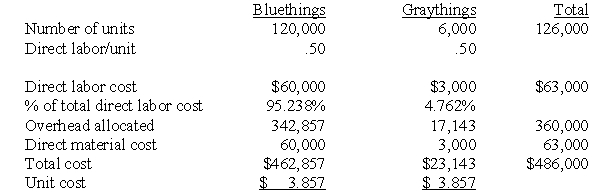
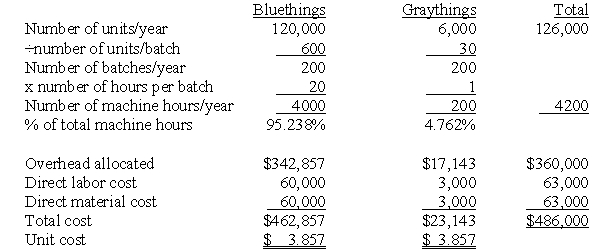
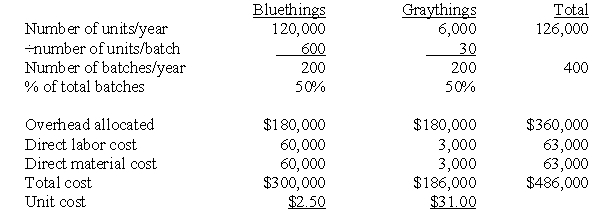
There are two cost drivers in Set-up Company.Unit volume drives direct materials and direct labor,but set-ups (number of batches)appear to drive overhead costs.Allocating overhead using direct labor gives an incorrect impression of how overhead costs vary and distorts product costs.Overhead costs are incurred in set-ups.While run times per unit of thing is the same for blues and grays,batch sizes vary considerably.In fact,bluethings and graythings each required 200 batches.Therefore,each product line (as opposed to each unit of product)should be allocated an equal dollar amount of overhead.If this is done,then graythings become massive losers and bluethings are seen to be profitable,even with market price of $3 per unit.
But these allocated costs using number of batches still do not necessarily represent opportunity costs.If the thing-a-majig and set-up crews are not operating at full capacity,then the opportunity cost of a batch of graythings is $30 (just variable cost).However,if the firm is reducing the number of bluethings it can produce to make graythings (production is at capacity),then the opportunity cost of a graything is the forgone margin on a batch of bluethings plus the variable costs of the graythings.Or,
