Deck 15: Lean and Six Sigma Management and Leading Change
Question
Question
Question
Question
Question
Question
Question
Question
Question
Question
Question
Question
Question
Question
Question
Question
Question
Question
Question
Question
Question
Unlock Deck
Sign up to unlock the cards in this deck!
Unlock Deck
Unlock Deck
1/21
Play
Full screen (f)
Deck 15: Lean and Six Sigma Management and Leading Change
1
Currently, a company produces 1500 parts per day to meet demand. A standard container of the parts under consideration holds 250 items. It takes 0.75 day to receive the parts once a card is released. If the company wants a safety stock of 500 of these parts, how many kanban cards are needed?
Kanban:
Kanban is the method of a card system, which is used, for controlling the flow of materials through process.
It is given that the daily demand, container size, lead-time. It is required to determine the number of Kanban cards if there is no safety stock.
Determine the number of Kanban cards:
Number of Kanban cards is determined by dividing the value, whichis attained by adding the safety with the multiple of daily demand and lead times with container size.
C refers to the number of kanban cards.
B refers to the safety stock.
D refers to the daily demand of the item.
L refers to lead time.
S refers to the container size.
Hence, the number of Kanban cards is
.
Kanban is the method of a card system, which is used, for controlling the flow of materials through process.
It is given that the daily demand, container size, lead-time. It is required to determine the number of Kanban cards if there is no safety stock.
Determine the number of Kanban cards:
Number of Kanban cards is determined by dividing the value, whichis attained by adding the safety with the multiple of daily demand and lead times with container size.
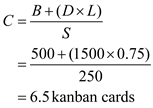
B refers to the safety stock.
D refers to the daily demand of the item.
L refers to lead time.
S refers to the container size.
Hence, the number of Kanban cards is
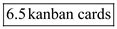
2
Briefly compare and contrast the roles and responsibilities of black belts and green belts in a Six Sigma organization.
Black belt and green belt:
Black belt is one of the roles of six-sigma organization. They are individuals specially trained to execute six sigma projects of the organization.
Green belt is another role adopted by six-sigma organization. They are individuals trained to use the basic quality tools.
Green belt's roles and responsibilities:
Green belts are expert in managing basic quality tools. Green belt individuals work part time on design and process development of the organization. Sometimes, the result of black belt and green belt activities are similar to some extent. Green belt individuals are involved in less critical projects.
Black belt's roles and responsibilities:
The black belt is a solution to six-sigma or lean management. The training of black belt individuals takes around four to six months. Once the training is complete, the firm appoints these individuals to complete the project of six-sigma cost reduction.
Conclusion:
There is a significant difference between black belt and green belt individuals. Black belts work on most critical projects, but green belts work on less critical projects. The training period is also more for black belts than green belts.
Black belt is one of the roles of six-sigma organization. They are individuals specially trained to execute six sigma projects of the organization.
Green belt is another role adopted by six-sigma organization. They are individuals trained to use the basic quality tools.
Green belt's roles and responsibilities:
Green belts are expert in managing basic quality tools. Green belt individuals work part time on design and process development of the organization. Sometimes, the result of black belt and green belt activities are similar to some extent. Green belt individuals are involved in less critical projects.
Black belt's roles and responsibilities:
The black belt is a solution to six-sigma or lean management. The training of black belt individuals takes around four to six months. Once the training is complete, the firm appoints these individuals to complete the project of six-sigma cost reduction.
Conclusion:
There is a significant difference between black belt and green belt individuals. Black belts work on most critical projects, but green belts work on less critical projects. The training period is also more for black belts than green belts.
3
What is DMAIC? How is it related to the Six Sigma process?
Define, Measure, Analyze, Improve, Control (DMAIC):
• Define: It refers to defining customer deliverables and project goals.
• Measure: It refers to the evaluation of recognized current performance levels of the project.
• Analyze: It refers to analyzing and determining the original cause of imperfection.
• Improve: It refers to improvement of the process by way of eradicating imperfections or defects.
• Control: It refers to controlled future performance of the process.
Determine whether DMAIC is related to six-sigma process:
There is a relationship between DMAIC and the six-sigma process. The process involves defining the problem, measuring the data, analyzing performance of the data, implementing and designing improvements, and monitoring the process of improvement.
There are activities in each stage of the DMAIC process. The six-sigma project consistently uses these five stages to provide a standard method for improvement.
Conclusion:
The six-sigma procedure consists of DMAIC five-stage process. It uses to develop the design of the organization efficiently by determining and solving the defects.
• Define: It refers to defining customer deliverables and project goals.
• Measure: It refers to the evaluation of recognized current performance levels of the project.
• Analyze: It refers to analyzing and determining the original cause of imperfection.
• Improve: It refers to improvement of the process by way of eradicating imperfections or defects.
• Control: It refers to controlled future performance of the process.
Determine whether DMAIC is related to six-sigma process:
There is a relationship between DMAIC and the six-sigma process. The process involves defining the problem, measuring the data, analyzing performance of the data, implementing and designing improvements, and monitoring the process of improvement.
There are activities in each stage of the DMAIC process. The six-sigma project consistently uses these five stages to provide a standard method for improvement.
Conclusion:
The six-sigma procedure consists of DMAIC five-stage process. It uses to develop the design of the organization efficiently by determining and solving the defects.
4
What is meant by the term muda? Why is reducing muda a focus of lean/Six Sigma management?
Unlock Deck
Unlock for access to all 21 flashcards in this deck.
Unlock Deck
k this deck
5
Briefly describe the two views of lean management that are common in business literature.
Unlock Deck
Unlock for access to all 21 flashcards in this deck.
Unlock Deck
k this deck
6
What are the seven wastes that Toyota Motor Company addresses in its improvement processes?
Unlock Deck
Unlock for access to all 21 flashcards in this deck.
Unlock Deck
k this deck
7
What is a kanban? How is it related to inventory movement through a process?
Unlock Deck
Unlock for access to all 21 flashcards in this deck.
Unlock Deck
k this deck
8
List and briefly define the different types of kanbans that can be found in a production process.
Unlock Deck
Unlock for access to all 21 flashcards in this deck.
Unlock Deck
k this deck
9
Susan Gonzalez was puzzled. Her company, Automotive Resources, had established a favorable reputation as a supplier of parts and components to automobile assembly plants in the United States, Canada, and Mexico. She had been with die company for nearly 20 years and had watched it grow from a small company with only one plant, producing a limited number of products, to a company with five production facilities in a three-state region now supplying a variety of components for the small car, small truck, and SUV market.
Susan, now the company's vice president of production and lean operations, was facing a growing challenge. The economic downturn was threatening not only the firms profitability, but its very survival. Customers were beginning to complain about late deliveries and quality problems with parts supplied by Automotive Resources. Customers were also less willing to accept price increases now than in the past. Employees of Automotive Resources were grumbling about unpredictable work schedules, declining worker benefits, and hourly wages, which had been decreasing since the start of the economic downturn. Susan, who over her career at Automotive Resources had attended a variety of professional development programs focused on manager employee relations, quality improvement, supplier customer relationship management, lean operations, Six Sigma principles, and kaizen, knew that something significant needed to be done to better position her company in the current economy. Recently, she had been hearing more and more companies and consultants talk about sustainability and its relationship to the supply chain. She also knew that any program she implemented would have to have input from management and employees. Her customers would need to be convinced that she could supply cost-competitive, quality parts with faster response times. She also understood that her customers were now concerned about how her company was engaged in enhancing its efforts in sustainability. Susan knew that she needed to develop a program that could help address the many issues she faced. Which program would that be, and how could it be structured? If only she had a blueprint to follow.
Questions
1. Briefly describe the problems facing Automotive Resources.
2. What options do you think are available to Susan?
3. What attributes of lean management, kaizen, and Six Sigma management might be applicable to the challenges that Susan faces?
4. How can Susan and the Automotive Resources management team lead the change needed to improve the company's competitive position?
Susan, now the company's vice president of production and lean operations, was facing a growing challenge. The economic downturn was threatening not only the firms profitability, but its very survival. Customers were beginning to complain about late deliveries and quality problems with parts supplied by Automotive Resources. Customers were also less willing to accept price increases now than in the past. Employees of Automotive Resources were grumbling about unpredictable work schedules, declining worker benefits, and hourly wages, which had been decreasing since the start of the economic downturn. Susan, who over her career at Automotive Resources had attended a variety of professional development programs focused on manager employee relations, quality improvement, supplier customer relationship management, lean operations, Six Sigma principles, and kaizen, knew that something significant needed to be done to better position her company in the current economy. Recently, she had been hearing more and more companies and consultants talk about sustainability and its relationship to the supply chain. She also knew that any program she implemented would have to have input from management and employees. Her customers would need to be convinced that she could supply cost-competitive, quality parts with faster response times. She also understood that her customers were now concerned about how her company was engaged in enhancing its efforts in sustainability. Susan knew that she needed to develop a program that could help address the many issues she faced. Which program would that be, and how could it be structured? If only she had a blueprint to follow.
Questions
1. Briefly describe the problems facing Automotive Resources.
2. What options do you think are available to Susan?
3. What attributes of lean management, kaizen, and Six Sigma management might be applicable to the challenges that Susan faces?
4. How can Susan and the Automotive Resources management team lead the change needed to improve the company's competitive position?
Unlock Deck
Unlock for access to all 21 flashcards in this deck.
Unlock Deck
k this deck
10
What is meant by the term jidoka ? Briefly outline the steps involved in its implementation.
Unlock Deck
Unlock for access to all 21 flashcards in this deck.
Unlock Deck
k this deck
11
Within an organization, what is meant by change management?
Unlock Deck
Unlock for access to all 21 flashcards in this deck.
Unlock Deck
k this deck
12
Why is visibility an important component of the lean approach?
Unlock Deck
Unlock for access to all 21 flashcards in this deck.
Unlock Deck
k this deck
13
Together with a team of students, visit a company that has recently, or is currently, engaged in a lean/Six Sigma project. Ask the company to take you through its process for continuous improvement. What challenges did the company face? How were the challenges overcome? What opportunities did the company uncover? What specific tools and techniques were used to bring about continuous improvement? How has the company quantified the benefits of its improvement activities?
Unlock Deck
Unlock for access to all 21 flashcards in this deck.
Unlock Deck
k this deck
14
What is pull production? How does it help to accomplish the objectives of lean?
Unlock Deck
Unlock for access to all 21 flashcards in this deck.
Unlock Deck
k this deck
15
Successful business and organizations continually look for ways to improve operations and business processes. Working with a team of students, describe how lean/Six Sigma techniques can be used to identify problems, solve problems, and improve operations. Discuss the design, measure, analyze, improve, and control activities as they relate to continuous improvement. What types of employees would be involved in your lean/Six Sigma efforts? Describe the challenges you might face leading the change.
Unlock Deck
Unlock for access to all 21 flashcards in this deck.
Unlock Deck
k this deck
16
What is SMED? How is SMED related to small lot production?
Unlock Deck
Unlock for access to all 21 flashcards in this deck.
Unlock Deck
k this deck
17
A company produces 200 parts per day to meet daily demand. A standard container of the parts holds 25 items. It takes 0.1 day to receive the parts once the card is released. Assuming that the company has no safety stock for this part, determine the number of kanban cards needed to maintain production.
Unlock Deck
Unlock for access to all 21 flashcards in this deck.
Unlock Deck
k this deck
18
How is the N = 2 technique different from traditional acceptance sampling?
Unlock Deck
Unlock for access to all 21 flashcards in this deck.
Unlock Deck
k this deck
19
How can combining Six Sigma and lean techniques help an organization identify and solve problems?
Unlock Deck
Unlock for access to all 21 flashcards in this deck.
Unlock Deck
k this deck
20
A company produces 500 parts per day to meet its demand. A standard container of the parts holds 100 items.
It takes 0.25 day to receive the parts once a card is released. If the company wants a safety stock of 100 parts, how many kanban cards are needed?
It takes 0.25 day to receive the parts once a card is released. If the company wants a safety stock of 100 parts, how many kanban cards are needed?
Unlock Deck
Unlock for access to all 21 flashcards in this deck.
Unlock Deck
k this deck
21
Briefly describe what is meant by the term Six Sigma. How is it related to product design?
Unlock Deck
Unlock for access to all 21 flashcards in this deck.
Unlock Deck
k this deck