Deck 10: Sales and Operations Planning Aggregate Planning
Question
Question
Question
Question
Question
Question
Question
Question
Question
Question
Question
Question
Question
Question
Question
Question
Question
Question
Question
Question
Question
Question
Question
Question
Question
Question
Question
Question
Question
Question
Question
Question
Question
Question
Question
Question
Question
Question
Question
Question
Question
Question
Question
Question
Question
Question
Question
Question
Question
Question
Question
Question
Question
Question
Question
Question
Question
Question
Question
Question
Question
Question
Question
Question
Question
Question
Question
Question
Question
Question
Question
Question
Question
Question
Question
Question
Question
Question
Question
Question
Unlock Deck
Sign up to unlock the cards in this deck!
Unlock Deck
Unlock Deck
1/80
Play
Full screen (f)
Deck 10: Sales and Operations Planning Aggregate Planning
1
A company has a sales forecast for the following five months as shown in the table. If they have a beginning inventory of 100 units, what amount should be produced under a level plan in order for them to have an ending inventory of zero units at the end of the five-month period?
A)320 units per month
B)360 units per month
C)400 units per month
D)440 units per month
A)320 units per month
B)360 units per month
C)400 units per month
D)440 units per month
360 units per month
2
A company has a sales forecast for the following five months as shown in the table. If they have a beginning inventory of 225 units, what amount should be produced under a level plan in order for them to have an ending inventory of zero units at the end of the five-month period?
A)580 units per month
B)595 units per month
C)585 units per month
D)575 units per month
A)580 units per month
B)595 units per month
C)585 units per month
D)575 units per month
575 units per month
3
There are few, if any, options for adjusting capacity levels for managers involved in what planning level?
A)strategic planning
B)operational planning
C)tactical planning
D)detailed planning and control
A)strategic planning
B)operational planning
C)tactical planning
D)detailed planning and control
detailed planning and control
4
Distinguish between strategic, tactical and detailed planning and control in terms of their ability to adjust capacity, the amount of risk, and the specificity of the plans.
Unlock Deck
Unlock for access to all 80 flashcards in this deck.
Unlock Deck
k this deck
5
Compared to other levels of planning, detailed planning and control offers the greatest ability to adjust capacity.
Unlock Deck
Unlock for access to all 80 flashcards in this deck.
Unlock Deck
k this deck
6
Detailed planning and control is riskier than strategic planning.
Unlock Deck
Unlock for access to all 80 flashcards in this deck.
Unlock Deck
k this deck
7
Tactical capacity resources include:
A)customer demand.
B)the size of the workforce.
C)major process choice decisions.
D)construction of new plants.
A)customer demand.
B)the size of the workforce.
C)major process choice decisions.
D)construction of new plants.
Unlock Deck
Unlock for access to all 80 flashcards in this deck.
Unlock Deck
k this deck
8
A company has a sales forecast for the following five months as shown in the table. If they have a beginning inventory of 1225 units, what amount should be produced under a level plan in order for them to have an ending inventory of zero units at the end of the five-month period?
A)1,435 units per month
B)1,595 units per month
C)1,385 units per month
D)1,515 units per month
A)1,435 units per month
B)1,595 units per month
C)1,385 units per month
D)1,515 units per month
Unlock Deck
Unlock for access to all 80 flashcards in this deck.
Unlock Deck
k this deck
9
Planning numbers are somewhat aggregated (month by month)in what planning level?
A)strategic planning
B)operational planning
C)tactical planning
D)detailed planning and control
A)strategic planning
B)operational planning
C)tactical planning
D)detailed planning and control
Unlock Deck
Unlock for access to all 80 flashcards in this deck.
Unlock Deck
k this deck
10
How can a sales and operations plan be articulated so that all supply chain participants can understand what is needed?
Unlock Deck
Unlock for access to all 80 flashcards in this deck.
Unlock Deck
k this deck
11
Within the context of the planning cycle, the planning that takes place at the highest levels of the firm is called:
A)strategic planning.
B)operational planning.
C)tactical planning.
D)detailed planning and control.
A)strategic planning.
B)operational planning.
C)tactical planning.
D)detailed planning and control.
Unlock Deck
Unlock for access to all 80 flashcards in this deck.
Unlock Deck
k this deck
12
Sales and operations planning indicates how the organization will use its tactical capacity resources to meet expected customer demand.
Unlock Deck
Unlock for access to all 80 flashcards in this deck.
Unlock Deck
k this deck
13
A company has a sales forecast for the following five months as shown in the table. If they have a beginning inventory of 350 units, what amount should be produced under a level plan in order for them to have an ending inventory of zero units at the end of the five-month period?
A)580 units per month
B)595 units per month
C)610 units per month
D)640 units per month
A)580 units per month
B)595 units per month
C)610 units per month
D)640 units per month
Unlock Deck
Unlock for access to all 80 flashcards in this deck.
Unlock Deck
k this deck
14
What is the ending inventory level for April in the production plan shown in the table? All entries in the table are in terms of sales units.
A)150 units
B)125 units
C)100 units
D)75 units
A)150 units
B)125 units
C)100 units
D)75 units
Unlock Deck
Unlock for access to all 80 flashcards in this deck.
Unlock Deck
k this deck
15
Sales and operations planning should inform all members of the supply chain what to do and what not to do.
Unlock Deck
Unlock for access to all 80 flashcards in this deck.
Unlock Deck
k this deck
16
To develop a superior plan, sales and operations planning must consider:
A)customer demand.
B)capabilities of suppliers.
C)capabilities of logistics service providers.
D)All of these must be considered when performing S&OP.
A)customer demand.
B)capabilities of suppliers.
C)capabilities of logistics service providers.
D)All of these must be considered when performing S&OP.
Unlock Deck
Unlock for access to all 80 flashcards in this deck.
Unlock Deck
k this deck
17
The purpose of aggregate planning is to help businesses develop effective ________ plans.
Unlock Deck
Unlock for access to all 80 flashcards in this deck.
Unlock Deck
k this deck
18
It costs $10 to make a single unit using regular production and $15 to make a single unit using overtime production. Total overtime production is limited to 1000 units for the five-month period. The manufacturing plant has a regular production capacity of 250 units per month and 225 units in inventory at the start of the planning period. There is a $5 per unit charge for holding inventory at the end of each month and a limit of 600 units ending inventory for any period. What is the minimum cost production plan if the forecast must be met with a zero ending inventory each month?
A)$15,850
B)$16,150
C)$16,500
D)$16,800
A)$15,850
B)$16,150
C)$16,500
D)$16,800
Unlock Deck
Unlock for access to all 80 flashcards in this deck.
Unlock Deck
k this deck
19
Among strategic, tactical and detailed planning, it is ________ planning that presents managers with the fewest options for altering capacity.
Unlock Deck
Unlock for access to all 80 flashcards in this deck.
Unlock Deck
k this deck
20
What is the purpose of S&OP and what takes place at the strategic, tactical, and detailed planning and control levels?
Unlock Deck
Unlock for access to all 80 flashcards in this deck.
Unlock Deck
k this deck
21
Net cash flow is the difference between the value added and the cash on hand at the end of the period.
Unlock Deck
Unlock for access to all 80 flashcards in this deck.
Unlock Deck
k this deck
22
Bottom-up planning should be used when the product/service mix is unstable and resource requirements vary greatly across the offerings.
Unlock Deck
Unlock for access to all 80 flashcards in this deck.
Unlock Deck
k this deck
23
Regular production costs $25 per unit and selling a unit represents a cash inflow of $30 per unit. Assume that all units reflected on the forecast will be sold. What is the cumulative net cash flow at the end of April?
A)$10,000
B)$12,000
C)$5,750
D)$2,000
A)$10,000
B)$12,000
C)$5,750
D)$2,000
Unlock Deck
Unlock for access to all 80 flashcards in this deck.
Unlock Deck
k this deck
24
Forty percent of a house painter's business is exterior work and the other sixty percent is interior. The average exterior paint job takes 30 hours of labor and $500 of paint and primer, but the average interior job takes only 6 hours of labor and $80 of paint and primer. If he gets 25 service calls for the coming month and 30 calls for the month after that, which of the following resource requirements is correct?
A)The painter has supply costs of greater than $13,500 but less than $13,600 for the next two months.
B)The painter has a labor demand of greater than 800 hours but less than 850 hours for the next two months.
C)The painter has supply costs of greater than $13,400 but less than $13,500 for the next two months.
D)The painter has a labor demand of greater than 850 hours but less than 900 hours for the next two months.
A)The painter has supply costs of greater than $13,500 but less than $13,600 for the next two months.
B)The painter has a labor demand of greater than 800 hours but less than 850 hours for the next two months.
C)The painter has supply costs of greater than $13,400 but less than $13,500 for the next two months.
D)The painter has a labor demand of greater than 850 hours but less than 900 hours for the next two months.
Unlock Deck
Unlock for access to all 80 flashcards in this deck.
Unlock Deck
k this deck
25
Willow Trees Inc. makes seven different products, four of which are within their first year of existence. The demands for all products, especially the newest ones, are not well known. The newest products are intended to complement their existing products and take different materials, different processes, and an entirely different set of labor skills for production. Which of these statements regarding their likely sales and operations planning activities is BEST?
A)The planning values for the oldest items in the product line should be used for the new items in the product line.
B)Willow Trees Inc. should avoid using sales and operations planning until their product line matures.
C)Willow Trees Inc. should use top-down planning.
D)Willow Trees Inc. should use bottom-up planning.
A)The planning values for the oldest items in the product line should be used for the new items in the product line.
B)Willow Trees Inc. should avoid using sales and operations planning until their product line matures.
C)Willow Trees Inc. should use top-down planning.
D)Willow Trees Inc. should use bottom-up planning.
Unlock Deck
Unlock for access to all 80 flashcards in this deck.
Unlock Deck
k this deck
26
Regular production costs $15 per unit and selling a unit represents a cash inflow of $25 per unit. Assume that all units reflected on the forecast will be sold. What is the net cash flow for March?
A)$11,500
B)$7,500
C)$4,500
D)$3,000
A)$11,500
B)$7,500
C)$4,500
D)$3,000
Unlock Deck
Unlock for access to all 80 flashcards in this deck.
Unlock Deck
k this deck
27
At the beginning of the semester, you decide to devote 12 hours a week outside of class time to your operations management studies, regardless of scheduled tests, assignments, or project due dates. This is a level plan approach to your favorite course.
Unlock Deck
Unlock for access to all 80 flashcards in this deck.
Unlock Deck
k this deck
28
The alternative production strategies of level, chase, or mixed that are available in top-down planning cannot be used in bottom-up planning.
Unlock Deck
Unlock for access to all 80 flashcards in this deck.
Unlock Deck
k this deck
29
It costs $12 to make a single unit using regular production and $15 to make a single unit using overtime production. Total overtime production is limited to 500 units for the five month period. The manufacturing plant has a regular production capacity of 250 units per month and 50 units in inventory at the start of the planning period. There is a $5 per unit charge for holding inventory at the end of each month and a limit of 250 units ending inventory for any period. What is the lowest cost production plan if the forecast must be met with a zero ending inventory each month?
A)$20,850
B)$19,750
C)$19,500
D)$20,550
A)$20,850
B)$19,750
C)$19,500
D)$20,550
Unlock Deck
Unlock for access to all 80 flashcards in this deck.
Unlock Deck
k this deck
30
It costs $10 to make a single unit using regular production and $15 to make a single unit using overtime production. Finished units sell for $17 and are built to order. The manufacturing plant has a regular production capacity of 250 units per month and no inventory at the start of the planning period. What is the BEST net cash flow for the entire planning period if the manufacturer uses a chase plan?
A)$6,800
B)$7,050
C)$7,300
D)$7,550
A)$6,800
B)$7,050
C)$7,300
D)$7,550
Unlock Deck
Unlock for access to all 80 flashcards in this deck.
Unlock Deck
k this deck
31
A company has the cost structure shown in the table and faces a demand in July that exceeds capacity by 200 units. They enter June with an inventory of zero and a demand equal to capacity. Their best course of action in order to completely fill all of the orders for both June and July by the end of July is to:
A)subcontract 200 units in June and use 100% of their regular capacity in both June and July.
B)subcontract 100 units in both June and July and use 100% of their regular capacity in both June and July.
C)produce 200 units using overtime in July and use 100% of their regular capacity in both June and July.
D)subcontract 200 units in July and use 100% of their regular capacity in both June and July.
A)subcontract 200 units in June and use 100% of their regular capacity in both June and July.
B)subcontract 100 units in both June and July and use 100% of their regular capacity in both June and July.
C)produce 200 units using overtime in July and use 100% of their regular capacity in both June and July.
D)subcontract 200 units in July and use 100% of their regular capacity in both June and July.
Unlock Deck
Unlock for access to all 80 flashcards in this deck.
Unlock Deck
k this deck
32
Last month a firm made 100 model A's using all of their available labor. If they have already taken orders for 150 model A's for next month, then their planning value must be 1.5.
Unlock Deck
Unlock for access to all 80 flashcards in this deck.
Unlock Deck
k this deck
33
This graph of expected sales level and expected output shows: 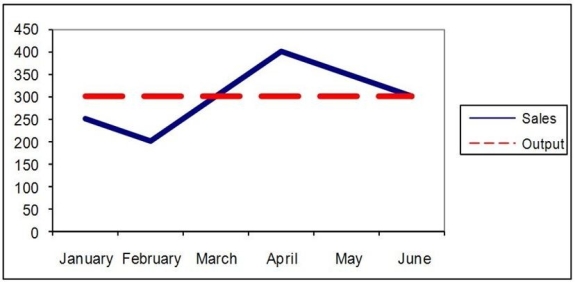
A)a chase production plan is being used.
B)a level production plan is being used.
C)a mixed production plan is being used.
D)planning levels have been computed.
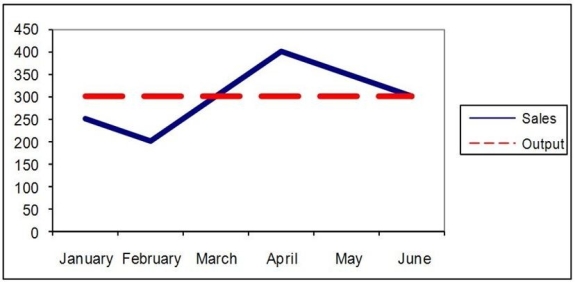
A)a chase production plan is being used.
B)a level production plan is being used.
C)a mixed production plan is being used.
D)planning levels have been computed.
Unlock Deck
Unlock for access to all 80 flashcards in this deck.
Unlock Deck
k this deck
34
Planning values are used in bottom-up planning, but cannot be used in top-down planning.
Unlock Deck
Unlock for access to all 80 flashcards in this deck.
Unlock Deck
k this deck
35
Seventy percent of a house painter's business is exterior work and the other thirty percent is interior. The average exterior paint job takes 20 hours of labor and $400 of paint and primer, but the average interior job takes only 6 hours of labor and $75 of paint and primer. If he gets 20 service calls for the coming month, which of the following resource requirements is correct?
A)The painter has supply costs of $4750 for next month.
B)The painter has a labor demand of 260 hours for next month.
C)The painter has supply costs of $6050 for next month.
D)The painter has a labor demand of 204 hours for next month.
A)The painter has supply costs of $4750 for next month.
B)The painter has a labor demand of 260 hours for next month.
C)The painter has supply costs of $6050 for next month.
D)The painter has a labor demand of 204 hours for next month.
Unlock Deck
Unlock for access to all 80 flashcards in this deck.
Unlock Deck
k this deck
36
The standard equation used by Gigi Enterprises for production planning is Production = Demand. The sales and operations planner is probably using:
A)a mixed production approach.
B)a level production approach.
C)a chase production approach.
D)a bottom-up planning approach.
A)a mixed production approach.
B)a level production approach.
C)a chase production approach.
D)a bottom-up planning approach.
Unlock Deck
Unlock for access to all 80 flashcards in this deck.
Unlock Deck
k this deck
37
Regular production costs $13 per unit and selling a unit represents a cash inflow of $28 per unit. Assume that all units reflected on the forecast will be sold. What is the cumulative net cash flow through March?
A)$11,250
B)$4,500
C)$8,400
D)$3,900
A)$11,250
B)$4,500
C)$8,400
D)$3,900
Unlock Deck
Unlock for access to all 80 flashcards in this deck.
Unlock Deck
k this deck
38
A company has the cost structure shown in the table and faces a demand in July that exceeds capacity by 200 units. They enter June with an inventory of zero and a demand equal to capacity. Their best course of action in order to completely fill all of the orders for both June and July by the end of July is to subcontract the extra 200 units in June and hold the inventory one period for July's demand.
Unlock Deck
Unlock for access to all 80 flashcards in this deck.
Unlock Deck
k this deck
39
It costs $12 to make a single unit using regular production and $15 to make a single unit using overtime production. Total overtime production is limited to 500 units for the five month period. The manufacturing plant has a regular production capacity of 250 units per month and 50 units in inventory at the start of the planning period. There is a $5 per unit charge for holding inventory at the end of each month and a limit of 250 units ending inventory for any period. What is the total number of units to be produced using overtime throughout the entire planning period if the forecast must be met and costs are to be minimized with a zero ending inventory each month?
A)450
B)500
C)400
D)350
A)450
B)500
C)400
D)350
Unlock Deck
Unlock for access to all 80 flashcards in this deck.
Unlock Deck
k this deck
40
When the products and services have very different resource requirements and the mix is unstable from one period to the next, bottom-up planning works best.
Unlock Deck
Unlock for access to all 80 flashcards in this deck.
Unlock Deck
k this deck
41
Last month, the sales and operations plan showed projections from January through April. This month, the sales and operations plan shows projections from February through May. This is an example of a rolling planning horizon.
Unlock Deck
Unlock for access to all 80 flashcards in this deck.
Unlock Deck
k this deck
42
Regular production costs $25 per unit and selling a unit represents a cash inflow of $30 per unit. Assume that all units reflected on the forecast will be sold. What is the cumulative net cash flow at the end of April?
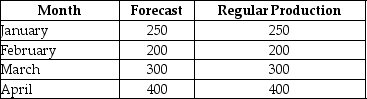
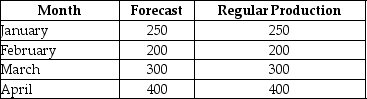
Unlock Deck
Unlock for access to all 80 flashcards in this deck.
Unlock Deck
k this deck
43
Your book describes three phases in the implementation of sales and operations planning in an organization. What are the three phases and what takes place in each?
Unlock Deck
Unlock for access to all 80 flashcards in this deck.
Unlock Deck
k this deck
44
There are three phases to sales and operations planning implementation. The first phase, during which employees are trained, information systems implemented, and ideal products are identified for initial efforts is called ________.
Unlock Deck
Unlock for access to all 80 flashcards in this deck.
Unlock Deck
k this deck
45
Describe the differences between level, chase, and mixed production plans. Use the forecast in the table to show the differences by creating a plan of each type. There is no beginning inventory and regular production capacity is 350 units. Overtime costs $10 extra and is limited to 50 units per month. Subcontracting is limited to 100 units per month and costs $15 per unit. Back orders cost $40 per unit and there is a cost of $5 per month to hold a unit in inventory. There is room for only 100 units in inventory.
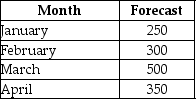
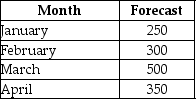
Unlock Deck
Unlock for access to all 80 flashcards in this deck.
Unlock Deck
k this deck
46
An organization with twenty people developing sales and operations plans might receive twenty different proposals. What are some factors an organization might consider when deciding among these alternative plans? Provide a ranking for your factors and support your ranking with examples from recent business news media.
Unlock Deck
Unlock for access to all 80 flashcards in this deck.
Unlock Deck
k this deck
47
In order for ________ planning to work, the mix of products or services must be essentially the same from one time period to the next or the products must have very similar resource requirements.
Unlock Deck
Unlock for access to all 80 flashcards in this deck.
Unlock Deck
k this deck
48
Create a level plan with a zero ending inventory for the forecast shown in the table. There is no beginning inventory and regular production capacity is 300 units. Overtime costs $15 extra and is limited to 25 units per month and subcontracting is limited to 60 units per month and costs $10 per unit. Back orders cost $50 per unit and there is a cost of $5 per month to hold a unit in inventory. What is the total plan cost above the regular production cost?
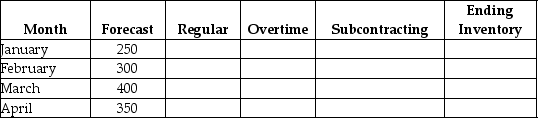
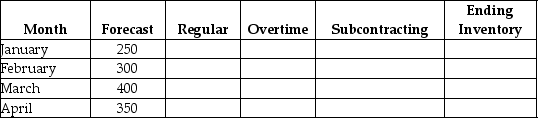
Unlock Deck
Unlock for access to all 80 flashcards in this deck.
Unlock Deck
k this deck
49
Sales and operations planning is a necessary task for all companies, but is never a source of competitive advantage.
Unlock Deck
Unlock for access to all 80 flashcards in this deck.
Unlock Deck
k this deck
50
A production planner can confirm future capacity requirements based on released or planned orders by referring to a(n)________.
Unlock Deck
Unlock for access to all 80 flashcards in this deck.
Unlock Deck
k this deck
51
The Super Bowl is right around the corner and Gowgem Hotels is aquiver with anticipation. They'd like to price their rooms at their three city locations, next to the stadium, near the airport, and in the suburbs, as high as possible but still achieve 100% occupancy. The approach they should take to this opportunity is:
A)yield management.
B)a tiered workforce.
C)a load profile.
D)a chase plan.
A)yield management.
B)a tiered workforce.
C)a load profile.
D)a chase plan.
Unlock Deck
Unlock for access to all 80 flashcards in this deck.
Unlock Deck
k this deck
52
An organization has developed three alternate sales and operations plans for the coming six months and now must choose between them. They should consider:
A)how their plan will impact supply chain partners.
B)what the cash flows are like.
C)how flexible the plan is.
D)All of these are useful criteria for a sales and operation plan.
A)how their plan will impact supply chain partners.
B)what the cash flows are like.
C)how flexible the plan is.
D)All of these are useful criteria for a sales and operation plan.
Unlock Deck
Unlock for access to all 80 flashcards in this deck.
Unlock Deck
k this deck
53
A(n)________ production plan matches production in each time period with the sales forecast.
Unlock Deck
Unlock for access to all 80 flashcards in this deck.
Unlock Deck
k this deck
54
Sales and operations plans must be updated as time progresses, so most firms establish a(n)________.
Unlock Deck
Unlock for access to all 80 flashcards in this deck.
Unlock Deck
k this deck
55
It costs $12 to make a single unit using regular production and $15 to make a single unit using overtime production. Total overtime production is limited to 500 units for the five month period. The manufacturing plant has a regular production capacity of 250 units per month and has 50 units in inventory at the start of the planning period. There is a $5 per unit charge for holding inventory at the end of each month and a limit of 250 units ending inventory for any period. Develop a minimum cost production plan if the forecast must be met and costs must be minimized.
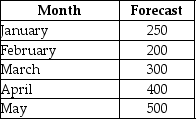
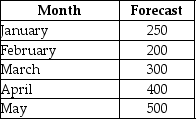
Unlock Deck
Unlock for access to all 80 flashcards in this deck.
Unlock Deck
k this deck
56
A company pondering the implementation of S&OP should first:
A)build the managerial support and infrastructure needed to make S&OP a success.
B)adopt S&OP as part of the organization's normal planning process.
C)elevate the decision-making authority of the sales and marketing team.
D)decide whether to commoditize the services offered with their products.
A)build the managerial support and infrastructure needed to make S&OP a success.
B)adopt S&OP as part of the organization's normal planning process.
C)elevate the decision-making authority of the sales and marketing team.
D)decide whether to commoditize the services offered with their products.
Unlock Deck
Unlock for access to all 80 flashcards in this deck.
Unlock Deck
k this deck
57
A sales and operations plan that varies both production and inventory levels is called a(n)________ production plan.
Unlock Deck
Unlock for access to all 80 flashcards in this deck.
Unlock Deck
k this deck
58
Tim subtracted his cash outflows for 2015 from his cash inflows for the same period to arrive at his ________.
Unlock Deck
Unlock for access to all 80 flashcards in this deck.
Unlock Deck
k this deck
59
Create a minimum cost chase plan for the forecast shown in the table. There is no beginning inventory and regular production capacity is 350 units. Overtime costs $20 extra and is limited to 50 units per month and subcontracting is limited to 100 units per month and costs $15 per unit. Back orders cost $40 per unit and there is a cost of $5 per month to hold a unit in inventory. There is room for only 100 units in inventory. What is the total plan cost above regular production cost?
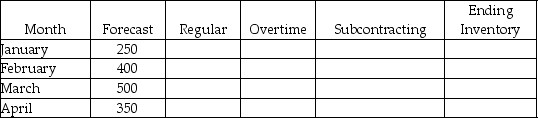
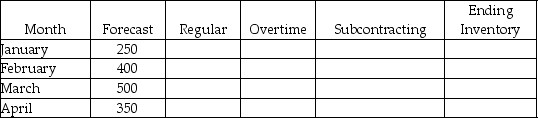
Unlock Deck
Unlock for access to all 80 flashcards in this deck.
Unlock Deck
k this deck
60
Describe how both top-down and bottom-up planning work and the situations where one approach is superior to the other.
Unlock Deck
Unlock for access to all 80 flashcards in this deck.
Unlock Deck
k this deck
61
A company that makes the rocket widget has one machine capable of producing this unique item. The machine requires an attendant, who works 40 hours a week for $12 per hour and has made himself available for a maximum of 8 hours of overtime. It costs $20 per hour to run the machine and it is capable of producing 10,000 rocket widgets per hour. The widgets sell for $10 per hundred and cost $1 per hundred in materials. If the production manager wishes to develop a sales and operations plans using an optimization model, which of the following statements is valid?
A)A constraint should limit overtime to less than 8 hours per week.
B)The objective function should maximize the amount of rocket widgets produced.
C)The objective function must be to minimize the overtime.
D)A constraint should limit the cost to run the machine to less than or equal to $20 per hour.
A)A constraint should limit overtime to less than 8 hours per week.
B)The objective function should maximize the amount of rocket widgets produced.
C)The objective function must be to minimize the overtime.
D)A constraint should limit the cost to run the machine to less than or equal to $20 per hour.
Unlock Deck
Unlock for access to all 80 flashcards in this deck.
Unlock Deck
k this deck
62
A home improvement store adds several workers to the garden center in the summer in order to meet the demands of do-it-yourselfers for their dazzling array of plants. Once gardening season is over, both the workers' jobs (and the plants they sold)will perish. The home improvement store is following an offloading strategy.
Unlock Deck
Unlock for access to all 80 flashcards in this deck.
Unlock Deck
k this deck
63
Sales and operations planning across a supply chain is similar in nature to collaborative planning, forecasting, and replenishment.
Unlock Deck
Unlock for access to all 80 flashcards in this deck.
Unlock Deck
k this deck
64
Each entity in a supply chain should produce its own sales and operations plan independent of the other members in order to improve the overall cost performance in a supply chain.
Unlock Deck
Unlock for access to all 80 flashcards in this deck.
Unlock Deck
k this deck
65
It costs $12 to make a single unit using regular production and $15 to make a single unit using overtime production. Total overtime production is limited to 500 units for the five-month period. The manufacturing plant has a regular production capacity of 250 units per month and 50 units in inventory at the start of the planning period. There is a $5 per unit charge for holding inventory at the end of each month and a limit of 250 units ending inventory for any period. Develop an objective function and constraints to solve this problem.
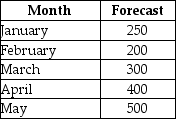
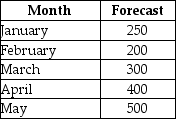
Unlock Deck
Unlock for access to all 80 flashcards in this deck.
Unlock Deck
k this deck
66
A(n)________ limits our ability to increase profits or cut costs by reducing the set of possible solutions in an optimization model.
Unlock Deck
Unlock for access to all 80 flashcards in this deck.
Unlock Deck
k this deck
67
A hotel using yield management would ________ prices if demand is higher than expected only if the expected result is ________.
Unlock Deck
Unlock for access to all 80 flashcards in this deck.
Unlock Deck
k this deck
68
A routine flight from LaGuardia Airport to Will Rogers Airport may have passengers that have paid radically different ticket prices. These prices fluctuate based on an approach called yield management.
Unlock Deck
Unlock for access to all 80 flashcards in this deck.
Unlock Deck
k this deck
69
Which of these is NOT an advantage of linking sales and operations planning throughout the supply chain?
A)increased sales revenue
B)greater coordination
C)improved productivity
D)fewer disruptions in the flow of goods and services
A)increased sales revenue
B)greater coordination
C)improved productivity
D)fewer disruptions in the flow of goods and services
Unlock Deck
Unlock for access to all 80 flashcards in this deck.
Unlock Deck
k this deck
70
How can and why should a firm link S&OP throughout the supply chain?
Unlock Deck
Unlock for access to all 80 flashcards in this deck.
Unlock Deck
k this deck
71
As potato harvest season approaches, the number of year-round llama wranglers is insufficient to meet the demand, so a few wranglers are hired just for the month it takes to haul the harvest down from the mountains to the anxious potato-festival crowd. This approach to meeting the labor requirements is called:
A)a tiered workforce.
B)offloading.
C)labor management.
D)yield management.
A)a tiered workforce.
B)offloading.
C)labor management.
D)yield management.
Unlock Deck
Unlock for access to all 80 flashcards in this deck.
Unlock Deck
k this deck
72
An organization that meets seasonal swings in demand by hiring and then laying off temporary workers while maintaining a few full-time permanent workers is employing a(n)________ strategy.
Unlock Deck
Unlock for access to all 80 flashcards in this deck.
Unlock Deck
k this deck
73
The objective function of an optimization modeling approach to S&OP should not allow available labor or equipment time to be exceeded.
Unlock Deck
Unlock for access to all 80 flashcards in this deck.
Unlock Deck
k this deck
74
What are the possibilities for matching capacity to sales and vice versa when doing S&OP in a service environment?
Unlock Deck
Unlock for access to all 80 flashcards in this deck.
Unlock Deck
k this deck
75
It costs $20 to make a single unit using regular production and $25 to make a single unit using overtime production. Total overtime production is limited to 50 units for the five-month period. The manufacturing plant has a regular production capacity of 300 units per month and no units in inventory at the start of the planning period. There is a $10 per unit charge for holding inventory at the end of each month and the ending inventory of the five-month planning period should be zero. Develop an objective function and constraints to solve this problem.
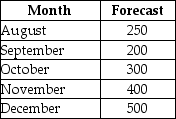
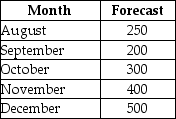
Unlock Deck
Unlock for access to all 80 flashcards in this deck.
Unlock Deck
k this deck
76
A company that makes the rocket widget has one machine capable of producing this unique item. The machine requires an attendant, who works 40 hours a week for $12 per hour and has made himself available for a maximum of 8 hours of overtime. It costs $20 per hour to run the machine and it is capable of producing 10,000 rocket widgets per hour. It is possible to outsource some production, as long as the total output is limited to less than ten percent of total output. The widgets sell for $10 per hundred and cost $1 per hundred in materials. If the production manager wishes to develop a sales and operations plans using an optimization model, which of the following statements is valid?
A)A constraint should limit the cost of materials to less than or equal to $1.
B)A constraint should be to limit outsourced output to less than 10% of total output.
C)The objective function must be to produce at least 10,000 rocket widgets per hour.
D)A constraint should limit the cost to run the machine to less than or equal to $20 per hour.
A)A constraint should limit the cost of materials to less than or equal to $1.
B)A constraint should be to limit outsourced output to less than 10% of total output.
C)The objective function must be to produce at least 10,000 rocket widgets per hour.
D)A constraint should limit the cost to run the machine to less than or equal to $20 per hour.
Unlock Deck
Unlock for access to all 80 flashcards in this deck.
Unlock Deck
k this deck
77
A company that makes the rocket widget has one machine capable of producing this unique item. The machine requires an attendant, who works 40 hours a week for $12 per hour and has made himself available for a maximum of 8 hours of overtime. It costs $20 per hour to run the machine and it is capable of producing 10,000 rocket widgets per hour. The widgets sell for $10 per hundred and cost $1 per hundred in materials. If the production manager wishes to develop a sales and operations plans using an optimization model, which of the following statements is valid?
A)The objective function should limit overtime to less than 8 hours per week.
B)The objective function should maximize the amount of rocket widgets produced.
C)The objective function should be to minimize costs.
D)None of these statements will help plan production using optimization modeling.
A)The objective function should limit overtime to less than 8 hours per week.
B)The objective function should maximize the amount of rocket widgets produced.
C)The objective function should be to minimize costs.
D)None of these statements will help plan production using optimization modeling.
Unlock Deck
Unlock for access to all 80 flashcards in this deck.
Unlock Deck
k this deck
78
A major retailer has recently deployed self-checkout stands at the front of the store. As long as you don't have items like paint, cold medicine, beer, fruits, or vegetables in your shopping cart, you can check out quickly in one of these lines. This retailer is providing a prime example of:
A)a tiered workforce.
B)offloading.
C)yield management.
D)a constraint.
A)a tiered workforce.
B)offloading.
C)yield management.
D)a constraint.
Unlock Deck
Unlock for access to all 80 flashcards in this deck.
Unlock Deck
k this deck
79
A(n)________ is a formula that is the goal of an optimization model for S&OP.
Unlock Deck
Unlock for access to all 80 flashcards in this deck.
Unlock Deck
k this deck
80
A constraint in an optimization modeling approach to S&OP should not allow overscheduling of equipment time.
Unlock Deck
Unlock for access to all 80 flashcards in this deck.
Unlock Deck
k this deck