Deck 9: Absorption Cost System
Question
Question
Question
Question
Question
Question
Question
Question
Question
Question
Question
Question
Question
Question
Question
Question
Question
Question
Question
Question
Question
Question
Question
Question
Question
Question
Question
Question
Unlock Deck
Sign up to unlock the cards in this deck!
Unlock Deck
Unlock Deck
1/28
Play
Full screen (f)
Deck 9: Absorption Cost System
1
Hercules Hair Restorer Inc. (HHRI) makes many varieties of hair restoration products which are sold under well-known marketing labels. A single batch contains 10,000 8 oz. bottles and takes two days to make. Typically 15 batches are completed per month, for different brands. Basic cost data for the month of January appears below.
The firm uses actual absorption costing and allocates overhead on the basis of direct labor hours. For batches made in January, which is true?
A)Direct materials costs total $192,200
B)Direct labor and direct material cost per batch is $192,900
C)Overheads per direct labor hour amount to $41.09
D)The full cost of 20 bottles is $385.80
E)None of the above
The firm uses actual absorption costing and allocates overhead on the basis of direct labor hours. For batches made in January, which is true?
A)Direct materials costs total $192,200
B)Direct labor and direct material cost per batch is $192,900
C)Overheads per direct labor hour amount to $41.09
D)The full cost of 20 bottles is $385.80
E)None of the above
The full cost of 20 bottles is $385.80
2
Hercules Hair Restorer Inc. (HHRI) makes many varieties of hair restoration products which are sold under well-known marketing labels. A single batch contains 10,000 8 oz. bottles and takes two days to make. Typically 15 batches are completed per month, for different brands. Basic cost data for the month of January appears below.
HHRI appoints a new CEO, who decides to increase production targets to 200 batches per year. She also hires a management accountant who decides to apply normal costing and does some research into cost behavior. Basic product data still applies. New information appears below. If HHRI uses a plant-wide rate based on a single cost pool, which of the following statements is true?
A)The overhead rate is $35.564 per hour
B)If machine hours are used as the cost driver, the overhead rate is $41.254 per hour
C)If machine hours are used as the cost driver, the full cost per bottle is $19.762
D)If direct labor hours are used as the cost driver, the full cost per batch $192,762.70
E)(c) and (d) only
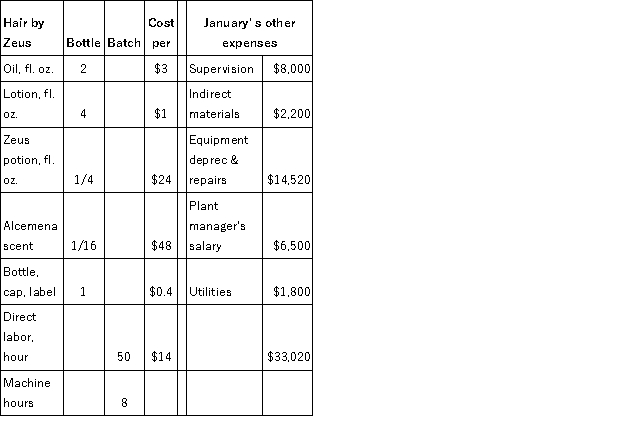
A)The overhead rate is $35.564 per hour
B)If machine hours are used as the cost driver, the overhead rate is $41.254 per hour
C)If machine hours are used as the cost driver, the full cost per bottle is $19.762
D)If direct labor hours are used as the cost driver, the full cost per batch $192,762.70
E)(c) and (d) only
(c) and (d) only
3
Rose Bach has recently been hired as controller of Lempco Inc., a sheet-metal manufacturer. Lempco has been in the sheet-metal business for many years and is currently investigating ways to modernize its manufacturing process. At the first staff meeting Bach attended, Bob Kelley, chief engineer, presented a proposal for automating the drilling department. Kelley recommended that Lempco purchase two robots that could replace the eight direct labor workers in the department. The cost savings outlined in Kelley's proposal include two elements. First, direct labor cost in the drilling department is eliminated. Second, manufacturing overhead cost in the department is reduced to zero because Lempco charges manufacturing overhead on the basis of direct labor dollars using a plantwide rate.
The president of Lempco felt that Kelley's explanation of the cost savings made no sense. Bach agreed and explained that as firms become more automated, they should rethink their manufacturing overhead systems. The president asked Bach to look into the matter and prepare a report for the next staff meeting.
To refresh her knowledge, Bach reviewed articles on manufacturing overhead allocation for an automated factory and discussed the matter with some of her peers. She also gathered the historical data presented below on the manufacturing overhead rates experienced by Lempco over the years. Bach also wanted to have some departmental data to present at the meeting. Using Lempco's accounting records, she was able to estimate the annual averages presented below for each manufacturing department in the 1990s.
Required:
a. Disregarding the proposed use of robots in the drilling department, describe the shortcomings of Lempco's current system for applying overhead.
b. Do you agree with Bob Kelley's statement that the manufacturing overhead cost in the drilling department will be reduced to zero if the automation proposal is implemented? Explain.
c. Recommend ways to improve Lempco's method for applying overhead by describing how it should revise its overhead accounting system:
(i) in the cutting and grinding departments.
(ii) to accommodate the automation of the drilling department.
The president of Lempco felt that Kelley's explanation of the cost savings made no sense. Bach agreed and explained that as firms become more automated, they should rethink their manufacturing overhead systems. The president asked Bach to look into the matter and prepare a report for the next staff meeting.
To refresh her knowledge, Bach reviewed articles on manufacturing overhead allocation for an automated factory and discussed the matter with some of her peers. She also gathered the historical data presented below on the manufacturing overhead rates experienced by Lempco over the years. Bach also wanted to have some departmental data to present at the meeting. Using Lempco's accounting records, she was able to estimate the annual averages presented below for each manufacturing department in the 1990s.
Required:
a. Disregarding the proposed use of robots in the drilling department, describe the shortcomings of Lempco's current system for applying overhead.
b. Do you agree with Bob Kelley's statement that the manufacturing overhead cost in the drilling department will be reduced to zero if the automation proposal is implemented? Explain.
c. Recommend ways to improve Lempco's method for applying overhead by describing how it should revise its overhead accounting system:
(i) in the cutting and grinding departments.
(ii) to accommodate the automation of the drilling department.
a. Lempco Inc. is currently using a plantwide overhead rate that is applied on the basis of direct labor dollars. In general, a plantwide manufacturing overhead rate is acceptable only if a similar relation between overhead and direct labor exists in all departments, or if the company manufactures products which receive proportional services from each department.
In some cases, departmental overhead rates are preferable to plantwide overhead rates because plantwide overhead rates do not provide:
• a framework for reviewing overhead costs (performance evaluation) on a departmental basis, identifying departmental cost overruns, or taking corrective action to improve departmental cost control.
• sufficient information about product profitability, thus increasing the difficulties associated with management decision making.
b. Because Lempco uses a plantwide overhead rate applied on the basis of direct labor dollars, the elimination of direct labor in the Drilling Department through the introduction of robots may appear to reduce the overhead cost of the Drilling Department to zero. However, this change will not reduce fixed manufacturing expenses such as depreciation, plant supervision, etc. In reality, the use of robots is likely to increase fixed expenses because of increased depreciation expense. Under Lempco's current method of allocating overhead costs, the remaining departments will merely absorb these costs.
c. (i) In order to improve the allocation of overhead costs in the Cutting and Grinding Departments, Lempco should:
• establish separate overhead accounts (pools) and rates for each of these departments.
• select an application basis for each of these departments that best reflects the relation of the departmental activity to the overhead costs incurred (e.g., direct labor hours, machine hours, etc.)
• identify, if possible, fixed and variable overhead costs and establish fixed and variable overhead rates.
(ii) In order to accommodate the automation of the Drilling Department in its overhead accounting system, Lempco should:
• establish separate overhead accounts (pools) and rates for the Drilling Department.
• identify, if possible, fixed and variable overhead costs and establish fixed and variable overhead rates.
• apply overhead costs to the Drilling Department on the basis of robot or machine hours.
In some cases, departmental overhead rates are preferable to plantwide overhead rates because plantwide overhead rates do not provide:
• a framework for reviewing overhead costs (performance evaluation) on a departmental basis, identifying departmental cost overruns, or taking corrective action to improve departmental cost control.
• sufficient information about product profitability, thus increasing the difficulties associated with management decision making.
b. Because Lempco uses a plantwide overhead rate applied on the basis of direct labor dollars, the elimination of direct labor in the Drilling Department through the introduction of robots may appear to reduce the overhead cost of the Drilling Department to zero. However, this change will not reduce fixed manufacturing expenses such as depreciation, plant supervision, etc. In reality, the use of robots is likely to increase fixed expenses because of increased depreciation expense. Under Lempco's current method of allocating overhead costs, the remaining departments will merely absorb these costs.
c. (i) In order to improve the allocation of overhead costs in the Cutting and Grinding Departments, Lempco should:
• establish separate overhead accounts (pools) and rates for each of these departments.
• select an application basis for each of these departments that best reflects the relation of the departmental activity to the overhead costs incurred (e.g., direct labor hours, machine hours, etc.)
• identify, if possible, fixed and variable overhead costs and establish fixed and variable overhead rates.
(ii) In order to accommodate the automation of the Drilling Department in its overhead accounting system, Lempco should:
• establish separate overhead accounts (pools) and rates for the Drilling Department.
• identify, if possible, fixed and variable overhead costs and establish fixed and variable overhead rates.
• apply overhead costs to the Drilling Department on the basis of robot or machine hours.
4
The Alphonse Company allocates fixed overhead costs by machine hours and variable overhead costs by direct labor hours. At the beginning of the year the company expects fixed overhead costs to be $600,000 and variable costs to be $800,000. The expected machine hours are 6,000 and the expected direct labor hours are 80,000. The actual fixed overhead costs are $700,000 and the actual variable overhead costs are $750,000. The actual machine hours during the year are 5,500 and the actual direct labor hours are 90,000.
Required:
a. How much overhead is allocated?
b. What is the over/under-absorbed overhead?
Required:
a. How much overhead is allocated?
b. What is the over/under-absorbed overhead?
Unlock Deck
Unlock for access to all 28 flashcards in this deck.
Unlock Deck
k this deck
5
Hercules Hair Restorer Inc. (HHRI) makes many varieties of hair restoration products which are sold under well-known marketing labels. A single batch contains 10,000 8 oz. bottles and takes two days to make. Typically 15 batches are completed per month, for different brands. Basic cost data for the month of January appears below.
If overheads for January are calculated per machine hour, which is false?
A)The hourly overhead absorption rate will be $275.17 per machine hour
B)The overheads per bottle remain the same
C)The full cost of 20 bottles is $385.80
D)The hourly overhead absorption rate will increase to $2,201.33
E)(c) and (d) only
If overheads for January are calculated per machine hour, which is false?
A)The hourly overhead absorption rate will be $275.17 per machine hour
B)The overheads per bottle remain the same
C)The full cost of 20 bottles is $385.80
D)The hourly overhead absorption rate will increase to $2,201.33
E)(c) and (d) only
Unlock Deck
Unlock for access to all 28 flashcards in this deck.
Unlock Deck
k this deck
6
Barbara Karloff Inc. recently set up as a microbrewery to manufacture a variety of beers, ales and stouts to customer specifications. The standard sizes per batch are as follows: stout, 5,000 gallons; ale, 8,000 gallons; and beer, 10,000 gallons. A beer batch takes six days to process, ale ten days and stout 14 days, the difference primarily attributable to the number of steps in the brewing process and the amount of time needed to mature the brew to the intended flavor specifications. By tradition, a new batch is started at 7 a.m., the start of a work day. It costs $1,800 in labor and variable overheads to set up each batch. The brewery's monthly fixed overheads are $220,000, which is allocated to products based on gallons. Other costing data appears below. With respect to direct materials, which is true for the first month of operations?
A)A total of 102,000 gallons was completed
B)A total of 16 bottles was donated to the picnic
C)Fifty-eight bottles were donated to the picnic
D)Basic direct materials cost $38,900
E)None of the above
A)A total of 102,000 gallons was completed
B)A total of 16 bottles was donated to the picnic
C)Fifty-eight bottles were donated to the picnic
D)Basic direct materials cost $38,900
E)None of the above
Unlock Deck
Unlock for access to all 28 flashcards in this deck.
Unlock Deck
k this deck
7
Hercules Hair Restorer Inc. (HHRI) makes many varieties of hair restoration products which are sold under well-known marketing labels. A single batch contains 10,000 8 oz. bottles and takes two days to make. Typically 15 batches are completed per month, for different brands. Basic cost data for the month of January appears below.
The new CEO has decided that 25% of the production target of 200 batches per year will be a new product, whose information appears below. If the same dual rate scheme from Q5 is applied, which is true?
A)The introduction of the Jove product will not affect the costing of the Zeus product
B)The introduction of the Jove product will cause the rate per labor hour to increase
C)The introduction of the Jove product will cause the rate per machine hour to fall
D)Full cost for the Zeus product will change, but by more than 2 cents per bottle
E)None of the above
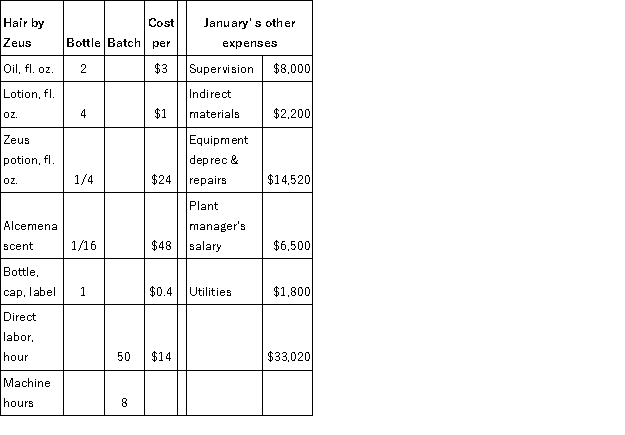
A)The introduction of the Jove product will not affect the costing of the Zeus product
B)The introduction of the Jove product will cause the rate per labor hour to increase
C)The introduction of the Jove product will cause the rate per machine hour to fall
D)Full cost for the Zeus product will change, but by more than 2 cents per bottle
E)None of the above
Unlock Deck
Unlock for access to all 28 flashcards in this deck.
Unlock Deck
k this deck
8
Barbara Karloff Inc. recently set up as a microbrewery to manufacture a variety of beers, ales and stouts to customer specifications. The standard sizes per batch are as follows: stout, 5,000 gallons; ale, 8,000 gallons; and beer, 10,000 gallons. A beer batch takes six days to process, ale ten days and stout 14 days, the difference primarily attributable to the number of steps in the brewing process and the amount of time needed to mature the brew to the intended flavor specifications. By tradition, a new batch is started at 7 a.m., the start of a work day. It costs $1,800 in labor and variable overheads to set up each batch. The brewery's monthly fixed overheads are $220,000, which is allocated to products based on gallons. Other costing data appears below. Basic direct materials are applied at the start of the process. Direct materials costs are charged when used in production and variable conversion costs are applied evenly throughout the production process. All products are sold in 12-ounce bottles. Beer is sold with 24 bottles per case, but ale is packed by the dozen in mini-crates, and stout in 6-packs. In April, the first month of operations, BKI finished five batches of beer, three of ale and one of stout. Dribbles of liquids from one batch that do not completely fill a bottle are poured away. Bottles from a batch that do not make up a complete case, crate or pack are donated to the company monthly picnic. In reviewing the production records, you find that a batch of stout was started on the 23rd, a batch of ale on the 27th, and a batch of beer on the 29th. These batches constitute ending work in process (EWIP).
With respect to conversion costs, which is true for the first month of operations?
A)The conversion costs traced directly to stout are $11,226
B)Total conversion costs are $320,784
C)Beer's direct conversion costs amount to $1.016 per gallon
D)$3.945 is ale's conversion cost per gallon
E)None of the above
With respect to conversion costs, which is true for the first month of operations?
A)The conversion costs traced directly to stout are $11,226
B)Total conversion costs are $320,784
C)Beer's direct conversion costs amount to $1.016 per gallon
D)$3.945 is ale's conversion cost per gallon
E)None of the above
Unlock Deck
Unlock for access to all 28 flashcards in this deck.
Unlock Deck
k this deck
9
Hercules Hair Restorer Inc. (HHRI) makes many varieties of hair restoration products which are sold under well-known marketing labels. A single batch contains 10,000 8 oz. bottles and takes two days to make. Typically 15 batches are completed per month, for different brands. Basic cost data for the month of January appears below.
The new CEO has decided that 25% of the production target of 200 batches per year will be a new product, whose information appears below. If HHRI makes 204 batches in the planned sales mix, which is true (to nearest $)?
A)Product Jove's total variable costs are $9,092,000
B)Product Jove's total variable costs are $9,273,840
C)Product Jove's total full costs are $9,386,191
D)Product Jove's total full costs are $9,388,163
E)None of the above
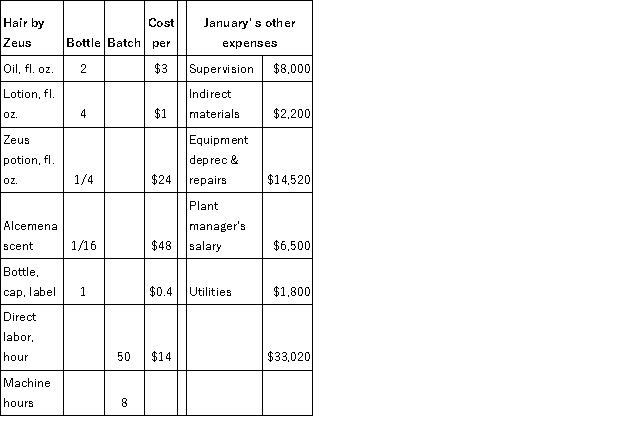
A)Product Jove's total variable costs are $9,092,000
B)Product Jove's total variable costs are $9,273,840
C)Product Jove's total full costs are $9,386,191
D)Product Jove's total full costs are $9,388,163
E)None of the above
Unlock Deck
Unlock for access to all 28 flashcards in this deck.
Unlock Deck
k this deck
10
Micro Enterprises planned to produce 120,000 lerts per year. Annual overheads, of which 32.5% are variable, are estimated at $320,400. Each lert takes 1.2 machine hours and 3 labor hours to produce. The firm allocates overhead by direct labor hours. You review the accounting records at the end of the year. You learn that Micro made 125,000 lerts in the year, using 356,000 direct labor hours. Actual overhead expenditures totaled $333,333.
A)Under-applied overhead is $417 and should be credited to CGS
B)Under-applied overhead is $417 and should be prorated across Raw Materials, Work in Process, and Finished Goods inventories and Cost of Goods Sold
C)Under-applied overhead is $16,493 and should be charged to Cost of Goods Sold
D)Over-applied overheads are $417 and should be credited to Cost of Goods Sold
E)None of the above
A)Under-applied overhead is $417 and should be credited to CGS
B)Under-applied overhead is $417 and should be prorated across Raw Materials, Work in Process, and Finished Goods inventories and Cost of Goods Sold
C)Under-applied overhead is $16,493 and should be charged to Cost of Goods Sold
D)Over-applied overheads are $417 and should be credited to Cost of Goods Sold
E)None of the above
Unlock Deck
Unlock for access to all 28 flashcards in this deck.
Unlock Deck
k this deck
11
Hercules Hair Restorer Inc. (HHRI) makes many varieties of hair restoration products which are sold under well-known marketing labels. A single batch contains 10,000 8 oz. bottles and takes two days to make. Typically 15 batches are completed per month, for different brands. Basic cost data for the month of January appears below.
Hercules Hair Restorer Inc. (HHRI) appoints a new CEO, who decides to increase production targets to 200 batches per year. She also hires a management accountant who decides to apply normal costing and does some research into cost behavior. Basic product data (from Q1) still applies. New information appears below. If HHRI uses for overhead allocation a dual rate system, whereby fixed overheads are allocated on the basis of direct labor hours and variable overheads are allocated on the basis of machine hours, which is true?
A)If this scheme is employed, the full cost per batch is $192,762.70
B)The overhead rate per DLH is $29.743
C)The hourly variable overhead rate is $34.502
D)The hourly fixed overhead rate is $215.638
E)None of the above
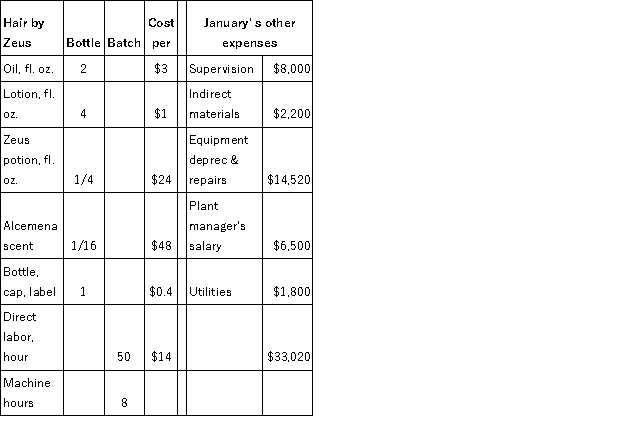
A)If this scheme is employed, the full cost per batch is $192,762.70
B)The overhead rate per DLH is $29.743
C)The hourly variable overhead rate is $34.502
D)The hourly fixed overhead rate is $215.638
E)None of the above
Unlock Deck
Unlock for access to all 28 flashcards in this deck.
Unlock Deck
k this deck
12
A computer manufacturer has the following account balances at the end of the year. These accounts contain $500,000 of allocated overhead. Actual overhead, however, is $600,000.
Required:
What are the account balances after prorating the under-absorbed overhead?
Required:
What are the account balances after prorating the under-absorbed overhead?
Unlock Deck
Unlock for access to all 28 flashcards in this deck.
Unlock Deck
k this deck
13
The Talbott Company has received an order (#324) for 100 widgets. On January 20 the shop supervisor requisitioned 100 units of part 503 at a cost of $5 per unit and 500 units of part 456 at a cost of $3 per unit to begin work on the 100 widgets. On the same day 20 hours of direct labor at $20 per hour are used to work on the widgets. On January 21, 200 units of part 543 at $6 per unit are requisitioned and 10 hours of direct labor at $15 per hour are performed on the 100 units of widgets to complete the job. Overhead is allocated to the job based on $5 per direct labor hour.
Required:
Prepare a job order cost sheet for the 100 widgets.
Required:
Prepare a job order cost sheet for the 100 widgets.
Unlock Deck
Unlock for access to all 28 flashcards in this deck.
Unlock Deck
k this deck
14
Micro Enterprises planned to produce 120,000 lerts per year. Annual overheads, of which 32.5% are variable, are estimated at $320,400. Each lert takes 1.2 machine hours and 3 labor hours to produce. The firm allocates overhead by direct labor hours. In February, when 11,000 lerts were produced, 32,000 direct labor hours were recorded and expenditures on overheads amounted to $29,650. Which is true for this month?
A)The overhead absorption rate is $0.9266 per DLH
B)Overhead applied is $29,370
C)Overhead applied is $29,650
D)Overhead applied is $28,480
E)None of the above
A)The overhead absorption rate is $0.9266 per DLH
B)Overhead applied is $29,370
C)Overhead applied is $29,650
D)Overhead applied is $28,480
E)None of the above
Unlock Deck
Unlock for access to all 28 flashcards in this deck.
Unlock Deck
k this deck
15
Barbara Karloff Inc. recently set up as a microbrewery to manufacture a variety of beers, ales and stouts to customer specifications. The standard sizes per batch are as follows: stout, 5,000 gallons; ale, 8,000 gallons; and beer, 10,000 gallons. A beer batch takes six days to process, ale ten days and stout 14 days, the difference primarily attributable to the number of steps in the brewing process and the amount of time needed to mature the brew to the intended flavor specifications. By tradition, a new batch is started at 7 a.m., the start of a work day. It costs $1,800 in labor and variable overheads to set up each batch. The brewery's monthly fixed overheads are $220,000, which is allocated to products based on gallons. Other costing data appears below. Basic direct materials are applied at the start of the process. Direct materials costs are charged when used in production and variable conversion costs are applied evenly throughout the production process. All products are sold in 12-ounce bottles. Beer is sold with 24 bottles per case, but ale is packed by the dozen in mini-crates, and stout in 6-packs. In April, the first month of operations, BKI finished five batches of beer, three of ale and one of stout. Dribbles of liquids from one batch that do not completely fill a bottle are poured away. Bottles from a batch that do not make up a complete case, crate or pack are donated to the company monthly picnic. In reviewing the production records, you find that a batch of stout was started on the 23rd, a batch of ale on the 27th, and a batch of beer on the 29th. These batches constitute ending work in process (EWIP).
Which is true as far as equivalent units of output are concerned?
A)53,333 gallons of beer are complete with respect to materials
B)1,280,000 fluid ounces of ale and 8,888 packs of stout were completed
C)24,000 gallons of ale have been completed with respect to conversion costs
D)7,857 gallons of stout have been completed with respect to conversion costs
E)None of the above
Which is true as far as equivalent units of output are concerned?
A)53,333 gallons of beer are complete with respect to materials
B)1,280,000 fluid ounces of ale and 8,888 packs of stout were completed
C)24,000 gallons of ale have been completed with respect to conversion costs
D)7,857 gallons of stout have been completed with respect to conversion costs
E)None of the above
Unlock Deck
Unlock for access to all 28 flashcards in this deck.
Unlock Deck
k this deck
16
Incentives and Depreciation Methods
What conditions are likely to exist when operating managers are compensated based on accounting earnings and accelerated depreciation methods are used to compute overhead charges to operating departments?
What conditions are likely to exist when operating managers are compensated based on accounting earnings and accelerated depreciation methods are used to compute overhead charges to operating departments?
Unlock Deck
Unlock for access to all 28 flashcards in this deck.
Unlock Deck
k this deck
17
First Eastern Bank is a large, multi-branch bank offering a wide variety of commercial and retail banking services. Eastern uses an absorption costing system to monitor the costs of various services and provide information for a variety of decisions.
One set of services is a retail loan operation providing residential mortgages, car loans, and student college loans. All loan applications are filed by the applicant at a branch bank, where the branch manager fills out the loan application. From there, the loan application is sent to the loan processing department, where the applicant's credit history is checked and a recommendation is made regarding loan approval based on the applicant's credit history and current financial situation. This recommendation is forwarded to the loan committee of senior lending officers, who review the file and make a final decision.
Thus, there are three stages to making a loan: application in a branch, the loan processing department, and the loan committee. Mr. and Mrs. Jones visit the West Street branch and file an application for a residential mortgage. The Jones's loan application is processed through the three stages.
• West Street Branch Bank. The branch manager spends one hour taking the application. The branch manager spends 1,000 hours per year of her total time taking loan applications and the remainder of her time providing other direct services to customers. Total overhead in the West Street Branch is budgeted to be $259,000, excluding the manager's salary, and is allocated to direct customer services using the branch manager's time spent providing direct customer services. The branch manager's annual salary is $42,600.
• Processing department. The processing department budgets its total overhead for the year to be $800,000, which is allocated to loans processed using direct labor hours. Budgeted direct labor hours for the year are 40,000 hours. Direct labor hours in the processing department cost $18 per hour. The Jones's loan requires five direct labor hours in the loan processing department.
• Loan committee. Ten senior bank executives are on the loan committee. The loan committee meets 52 times per year, every Wednesday, all day, to approve all loans. The average salary and benefits of each member of the loan committee are $104,000. The loan committee spends 15 minutes reviewing the Jones's loan application before approving it.
For costing purposes, all employees are assumed to work eight-hour days, five days per week, and 52 weeks per year.
Required:
Calculate the total cost of taking the application, processing, and approving the Joneses' mortgage.
One set of services is a retail loan operation providing residential mortgages, car loans, and student college loans. All loan applications are filed by the applicant at a branch bank, where the branch manager fills out the loan application. From there, the loan application is sent to the loan processing department, where the applicant's credit history is checked and a recommendation is made regarding loan approval based on the applicant's credit history and current financial situation. This recommendation is forwarded to the loan committee of senior lending officers, who review the file and make a final decision.
Thus, there are three stages to making a loan: application in a branch, the loan processing department, and the loan committee. Mr. and Mrs. Jones visit the West Street branch and file an application for a residential mortgage. The Jones's loan application is processed through the three stages.
• West Street Branch Bank. The branch manager spends one hour taking the application. The branch manager spends 1,000 hours per year of her total time taking loan applications and the remainder of her time providing other direct services to customers. Total overhead in the West Street Branch is budgeted to be $259,000, excluding the manager's salary, and is allocated to direct customer services using the branch manager's time spent providing direct customer services. The branch manager's annual salary is $42,600.
• Processing department. The processing department budgets its total overhead for the year to be $800,000, which is allocated to loans processed using direct labor hours. Budgeted direct labor hours for the year are 40,000 hours. Direct labor hours in the processing department cost $18 per hour. The Jones's loan requires five direct labor hours in the loan processing department.
• Loan committee. Ten senior bank executives are on the loan committee. The loan committee meets 52 times per year, every Wednesday, all day, to approve all loans. The average salary and benefits of each member of the loan committee are $104,000. The loan committee spends 15 minutes reviewing the Jones's loan application before approving it.
For costing purposes, all employees are assumed to work eight-hour days, five days per week, and 52 weeks per year.
Required:
Calculate the total cost of taking the application, processing, and approving the Joneses' mortgage.
Unlock Deck
Unlock for access to all 28 flashcards in this deck.
Unlock Deck
k this deck
18
Micro Enterprises planned to produce 120,000 lerts per year. Annual overheads, of which 32.5% are variable, are estimated at $320,400. Each lert takes 1.2 machine hours and 3 labor hours to produce. The firm allocates overhead by direct labor hours. In March, when 11,500 lerts were produced, 33,500 direct labor hours were recorded and expenditures on overheads amounted to $31,200. Which is true for this month?
A)Under-applied overheads are $495
B)Over-applied overheads are $495
C)Under-applied overheads are $1,385
D)Over-applied overheads are $1,385
E)None of the above
A)Under-applied overheads are $495
B)Over-applied overheads are $495
C)Under-applied overheads are $1,385
D)Over-applied overheads are $1,385
E)None of the above
Unlock Deck
Unlock for access to all 28 flashcards in this deck.
Unlock Deck
k this deck
19
The job cost sheet for 1,000 units of toy trucks is:
All of the materials for the job were purchased on 4/10. The batch of 1,000 toy trucks is sold on 7/10.
What are the costs of this job order in the raw materials account, the work-in-process account, the finished goods account, and the cost of goods account on 4/30, 5/31, 6/30 and 7/31?
All of the materials for the job were purchased on 4/10. The batch of 1,000 toy trucks is sold on 7/10.
What are the costs of this job order in the raw materials account, the work-in-process account, the finished goods account, and the cost of goods account on 4/30, 5/31, 6/30 and 7/31?
Unlock Deck
Unlock for access to all 28 flashcards in this deck.
Unlock Deck
k this deck
20
Hercules Hair Restorer Inc. (HHRI) makes many varieties of hair restoration products which are sold under well-known marketing labels. A single batch contains 10,000 8 oz. bottles and takes two days to make. Typically 15 batches are completed per month, for different brands. Basic cost data for the month of January appears below.
Why is actual costing of overheads less accepted than normal costing?
A)It is impossible to determine overheads per job until the end of the year
B)Monthly allocation of actual overheads leads to unusually low or high product costs when monthly output differs from the annual average
C)It exacerbates the problem of under/over applied overheads
D)Actual costing is widely used in practice
E)(a) and (b) only
Why is actual costing of overheads less accepted than normal costing?
A)It is impossible to determine overheads per job until the end of the year
B)Monthly allocation of actual overheads leads to unusually low or high product costs when monthly output differs from the annual average
C)It exacerbates the problem of under/over applied overheads
D)Actual costing is widely used in practice
E)(a) and (b) only
Unlock Deck
Unlock for access to all 28 flashcards in this deck.
Unlock Deck
k this deck
21
The Cope Company had an over-absorbed overhead balance at year-end. The firm wrote off one-third of it to Cost of Goods Sold, thereby raising net income by $100,000, and the remainder was charged to inventory accounts. Overhead is allocated to products using direct labor dollars. The firm uses a flexible budget to calculate its overhead rate. Before the year began, the variable overhead rate and budgeted volume were estimated to be $7.00 per direct labor dollar and $1 million, respectively. Actual overhead incurred for the year was $9.7 million, and actual direct labor cost was $1,250,000.
Required:
What budgeted fixed overhead amount did the Cope Company use in calculating the overhead rate?
Required:
What budgeted fixed overhead amount did the Cope Company use in calculating the overhead rate?
Unlock Deck
Unlock for access to all 28 flashcards in this deck.
Unlock Deck
k this deck
22
Employees' Incentives to Mis-state Product Costs
Chris Maynard, one of Owens Metal Products' three customer engineers, is reviewing the costs of the radar housings for Lingle Aerospace (LA). LA is one of Maynard's largest accounts and the radar housing is a fabricated piece of sheet metal LA uses to assemble an aircraft's radar system installed in the nose of the plane. In reviewing the detailed cost record for this job, Maynard is concerned that the direct labor posted to the job appears too high. He estimated the direct labor in the welding department to be six hours per batch of 130 units. But the job sheet reports that 9.5 hours were used.
Background
Owens Metal Products is a custom machine shop that bids on orders and produces sheet metal parts in batches. It was founded 30 years ago by two tool and die makers in their mid-30s: Jack Spence and Don Carter. Spence and Carter were previously employed by a national automobile company. They started Owens to make parts for local large manufacturing firms that did not have sufficient capacity to meet short-run production schedules. Now Owens competes by supplying certain types of parts more cheaply than large companies can produce them internally. It does this by (1) bidding on jobs with run lengths that match Owens's machine configurations, (2) employing nonunion labor, and (3) avoiding much of the overhead existing in big factories. Owens Metal Products now manufactures sheet metal parts used in a variety of office products, computers, and printers. The firm has grown in recent years and has benefited from the outsourcing movement whereby large firms seeking to reduce their manufacturing costs outsource noncritical metal fabricated parts.
Owens's single plant has a number of sheet metal presses (the largest being a 500-ton press), numerically controlled cutting and drilling machines, lathes, drill presses, and electric arc welders. Engineers contact customers to see if they have parts they are willing to outsource. Usually, the customer is introducing a new model and has not produced the tools necessary to fabricate the part internally. Owens's customer engineer works with the client on the manufacturing and design specifications for the part and submits a bid to produce and deliver a set number of parts over a given time period at a fixed price. In the process of preparing the bid, the customer engineer forecasts the cost of the job by estimating direct labor, direct material, and machine time required in each factory department.
Due to intense competition from other firms (as large office equipment companies constantly shift production worldwide to find the lowest-cost, highest-quality producers), shops such as Owens have high variability in volumes. In response to these volume changes, Owens is always laying off and rehiring employees. If Owens loses a large contract, it often requires six to nine months to replace the work. In the meantime, employees are laid off until new work can be found.
Two hundred employees now work at Owens, including sales, administrative, and factory employees. Besides production workers, Owens has a maintenance and janitorial staff. To improve cost competitiveness, Spence and Carter have been trying to get production employees to take over more of the maintenance and clean-up tasks when they have idle time. They would also like to see the workers cross-trained in more production and maintenance tasks to help better balance work flow in the factory. These actions will raise productivity and reduce costs. However, the attempts at cross-training have achieved very limited success.
Compensationsystem
Owens does not have a formal pay-for-performance or bonus system. All employees are paid straight salary with annual raises. Customer engineers do not receive commissions for sales. In good years, raises are higher. Management has explored incentive pay and piece-rate systems. They have concluded that the constantly changing product mix would cause such systems to be very expensive to implement and maintain.
At a sales staff meeting in February, Phil Matson, Owens's vice president of operation, mentioned they were going to award bonuses to the customer engineers if they could achieve their target sales forecasts. In July, Chris Maynard, whose sales were up 22 percent over the previous year, asked Matson whether total sales were ahead of the target needed for the bonus. Matson said that while sales were up for the year, the plant still had excess capacity and it appeared they would not achieve the forecast.
Accountingsystem
A job order cost system is used to accumulate direct labor and direct materials to individual jobs. At the end of the day, employees fill out a time sheet indicating the jobs they worked on and the time spent on each job. All the indirect costs are accumulated into a separate overhead cost pool for each factory department (pressing, drilling, and welding). The indirect costs for each department include equipment depreciation and lease charges, the department supervisor's salary, employees' idle time, and allocated utilities and occupancy charges (property taxes, plant building depreciation). Then, separate overhead rates are set for each department using direct labor hours as the allocation base. When an employee posts time to a particular job, the overhead rate for the employee's department multiplied by the employee's time charged to the job is the amount of overhead for that department charged to the job.
ProblemwiththeLingleAerospacejob
Chris Maynard contacts Phil Sanchez, supervisor of the welding department, and asks about the discrepancy between Maynard's estimate of 6.0 hours in the welding department and the 9.5 hours actually charged to the LA contract. Sanchez admits that there were two other jobs in the welding department at that time and that it is possible the employee had mistakenly charged some time to the LA contract instead of the other jobs.
Maynard then asks Linda Rawlings, supervisor of the drilling department, about the 67 labor hours charged to LA. Maynard had estimated the drilling time to be 53 hours for the batch. Rawlings said she was too busy now to look into the matter but she would contact him later. That was two weeks ago. Maynard is concerned that if the costs charged to the LA contract are too high, Phil Matson will ask LA for a higher price. If this happens, LA might shift the radar housing from Owens to another supplier.
When Jack Spence learned of the accounting errors on the LA account, he replied, "I don't see any problem. As long as the time cards are charged to jobs, our tax returns are right."
Required:
a. Identify various problems at Owens.
b. What improvements would you suggest Owens implement?
Chris Maynard, one of Owens Metal Products' three customer engineers, is reviewing the costs of the radar housings for Lingle Aerospace (LA). LA is one of Maynard's largest accounts and the radar housing is a fabricated piece of sheet metal LA uses to assemble an aircraft's radar system installed in the nose of the plane. In reviewing the detailed cost record for this job, Maynard is concerned that the direct labor posted to the job appears too high. He estimated the direct labor in the welding department to be six hours per batch of 130 units. But the job sheet reports that 9.5 hours were used.
Background
Owens Metal Products is a custom machine shop that bids on orders and produces sheet metal parts in batches. It was founded 30 years ago by two tool and die makers in their mid-30s: Jack Spence and Don Carter. Spence and Carter were previously employed by a national automobile company. They started Owens to make parts for local large manufacturing firms that did not have sufficient capacity to meet short-run production schedules. Now Owens competes by supplying certain types of parts more cheaply than large companies can produce them internally. It does this by (1) bidding on jobs with run lengths that match Owens's machine configurations, (2) employing nonunion labor, and (3) avoiding much of the overhead existing in big factories. Owens Metal Products now manufactures sheet metal parts used in a variety of office products, computers, and printers. The firm has grown in recent years and has benefited from the outsourcing movement whereby large firms seeking to reduce their manufacturing costs outsource noncritical metal fabricated parts.
Owens's single plant has a number of sheet metal presses (the largest being a 500-ton press), numerically controlled cutting and drilling machines, lathes, drill presses, and electric arc welders. Engineers contact customers to see if they have parts they are willing to outsource. Usually, the customer is introducing a new model and has not produced the tools necessary to fabricate the part internally. Owens's customer engineer works with the client on the manufacturing and design specifications for the part and submits a bid to produce and deliver a set number of parts over a given time period at a fixed price. In the process of preparing the bid, the customer engineer forecasts the cost of the job by estimating direct labor, direct material, and machine time required in each factory department.
Due to intense competition from other firms (as large office equipment companies constantly shift production worldwide to find the lowest-cost, highest-quality producers), shops such as Owens have high variability in volumes. In response to these volume changes, Owens is always laying off and rehiring employees. If Owens loses a large contract, it often requires six to nine months to replace the work. In the meantime, employees are laid off until new work can be found.
Two hundred employees now work at Owens, including sales, administrative, and factory employees. Besides production workers, Owens has a maintenance and janitorial staff. To improve cost competitiveness, Spence and Carter have been trying to get production employees to take over more of the maintenance and clean-up tasks when they have idle time. They would also like to see the workers cross-trained in more production and maintenance tasks to help better balance work flow in the factory. These actions will raise productivity and reduce costs. However, the attempts at cross-training have achieved very limited success.
Compensationsystem
Owens does not have a formal pay-for-performance or bonus system. All employees are paid straight salary with annual raises. Customer engineers do not receive commissions for sales. In good years, raises are higher. Management has explored incentive pay and piece-rate systems. They have concluded that the constantly changing product mix would cause such systems to be very expensive to implement and maintain.
At a sales staff meeting in February, Phil Matson, Owens's vice president of operation, mentioned they were going to award bonuses to the customer engineers if they could achieve their target sales forecasts. In July, Chris Maynard, whose sales were up 22 percent over the previous year, asked Matson whether total sales were ahead of the target needed for the bonus. Matson said that while sales were up for the year, the plant still had excess capacity and it appeared they would not achieve the forecast.
Accountingsystem
A job order cost system is used to accumulate direct labor and direct materials to individual jobs. At the end of the day, employees fill out a time sheet indicating the jobs they worked on and the time spent on each job. All the indirect costs are accumulated into a separate overhead cost pool for each factory department (pressing, drilling, and welding). The indirect costs for each department include equipment depreciation and lease charges, the department supervisor's salary, employees' idle time, and allocated utilities and occupancy charges (property taxes, plant building depreciation). Then, separate overhead rates are set for each department using direct labor hours as the allocation base. When an employee posts time to a particular job, the overhead rate for the employee's department multiplied by the employee's time charged to the job is the amount of overhead for that department charged to the job.
ProblemwiththeLingleAerospacejob
Chris Maynard contacts Phil Sanchez, supervisor of the welding department, and asks about the discrepancy between Maynard's estimate of 6.0 hours in the welding department and the 9.5 hours actually charged to the LA contract. Sanchez admits that there were two other jobs in the welding department at that time and that it is possible the employee had mistakenly charged some time to the LA contract instead of the other jobs.
Maynard then asks Linda Rawlings, supervisor of the drilling department, about the 67 labor hours charged to LA. Maynard had estimated the drilling time to be 53 hours for the batch. Rawlings said she was too busy now to look into the matter but she would contact him later. That was two weeks ago. Maynard is concerned that if the costs charged to the LA contract are too high, Phil Matson will ask LA for a higher price. If this happens, LA might shift the radar housing from Owens to another supplier.
When Jack Spence learned of the accounting errors on the LA account, he replied, "I don't see any problem. As long as the time cards are charged to jobs, our tax returns are right."
Required:
a. Identify various problems at Owens.
b. What improvements would you suggest Owens implement?
Unlock Deck
Unlock for access to all 28 flashcards in this deck.
Unlock Deck
k this deck
23
Overhead Rate, Flexible Budget, and Over-Absorbed Overhead
Snyder Stampings allocates overhead to products based on machine hours. It uses a flexible overhead budget to calculate a predetermined overhead rate at the beginning of the year. This rate is used during the year to allocate overhead to the various stampings produced. The following table summarizes operations for the last year:
Required:
In setting the overhead rate at the beginning of the year, what budgeted volume of machine hours was used?
Snyder Stampings allocates overhead to products based on machine hours. It uses a flexible overhead budget to calculate a predetermined overhead rate at the beginning of the year. This rate is used during the year to allocate overhead to the various stampings produced. The following table summarizes operations for the last year:
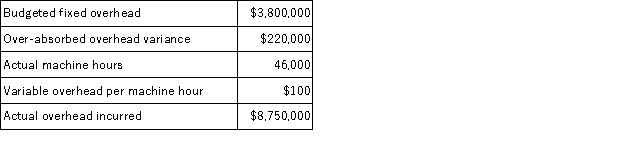
In setting the overhead rate at the beginning of the year, what budgeted volume of machine hours was used?
Unlock Deck
Unlock for access to all 28 flashcards in this deck.
Unlock Deck
k this deck
24
The following figures were taken from the records of Welling Co. for the current year. At the end of the year, two jobs were still in process. Details about the two jobs include: Welling Co. applies overhead at a budgeted rate, calculated at the beginning of the year. The budgeted rate is the ratio of budgeted overhead to budgeted direct labor costs. Budgeted figures for the current year were: Actual figures were There were no opening inventories. It is the practice of the company to prorate any over/under-absorption of overhead to finished goods inventory, work in process, and cost of goods sold based on the total dollars in these categories.
Required:
a. Compute the cost of work in process before over/under-applied overheads are prorated.
b. Prepare a schedule of finished goods inventory, work in process, and cost of goods sold after over/under-applied overheads are prorated.
c. What is the difference in operating income if the over/under-applied overhead is charged to cost of goods sold instead of being prorated to finished goods inventory, work in process, and cost of goods sold?
Required:
a. Compute the cost of work in process before over/under-applied overheads are prorated.
b. Prepare a schedule of finished goods inventory, work in process, and cost of goods sold after over/under-applied overheads are prorated.
c. What is the difference in operating income if the over/under-applied overhead is charged to cost of goods sold instead of being prorated to finished goods inventory, work in process, and cost of goods sold?
Unlock Deck
Unlock for access to all 28 flashcards in this deck.
Unlock Deck
k this deck
25
Comprehensive Absorption Costing Problem
The Denna Water plant in Sarasota, Florida, bottles purified and flavored waters in a variety of sizes (20, 36, 48, and 64 ounces) for sale through vending machines and retail stores. Volume is measured as bottled ounces. The plant's annual budgeted fixed manufacturing overhead amounts to $1.8 million, and variable manufacturing overhead is projected at $0.005 per bottled ounce. Projected volume in the Sarasota plant next year is 200 million ounces. Actual volume for the year accumulated to 210 million ounces and total manufacturing overhead incurred (both fixed and variable) was $2.85 million.
Required:
a. Calculate the Denna Sarasota plant overhead rate.
b. How much overhead was absorbed to products in the Sarasota plant?
c. Calculate the Denna Sarasota plant's over- or under-absorbed overhead.
d. Describe the effect on income when the over- or under-absorbed overhead calculated in (c) is written off to cost of goods sold.
The Denna Water plant in Sarasota, Florida, bottles purified and flavored waters in a variety of sizes (20, 36, 48, and 64 ounces) for sale through vending machines and retail stores. Volume is measured as bottled ounces. The plant's annual budgeted fixed manufacturing overhead amounts to $1.8 million, and variable manufacturing overhead is projected at $0.005 per bottled ounce. Projected volume in the Sarasota plant next year is 200 million ounces. Actual volume for the year accumulated to 210 million ounces and total manufacturing overhead incurred (both fixed and variable) was $2.85 million.
Required:
a. Calculate the Denna Sarasota plant overhead rate.
b. How much overhead was absorbed to products in the Sarasota plant?
c. Calculate the Denna Sarasota plant's over- or under-absorbed overhead.
d. Describe the effect on income when the over- or under-absorbed overhead calculated in (c) is written off to cost of goods sold.
Unlock Deck
Unlock for access to all 28 flashcards in this deck.
Unlock Deck
k this deck
26
Calculating and Disposing of Under-Applied Overhead
PPX is a specialized packaging company that packages other manufacturers' products. Other manufacturers ship their products to PPX in bulk. PPX then packages the products using high-speed, state-of-the-art packaging machines and ships the packaged products to wholesalers. A typical order involves packaging small toys in see-through plastic and cardboard containers.
PPX uses a flexible budget to forecast annual plantwide overhead, which is then allocated to jobs based on machine hours. The annual flexible overhead budget is projected to be $6 million of fixed costs and $120 per machine hour. The budgeted number of machine hours for the year is 20,000.
At the end of the year, 21,000 machine hours were used and actual overhead incurred was $9.14 million.
Required:
a. Calculate the overhead rate set at the beginning of the year.
b. Calculate the amount of over/under-absorbed overhead for the year.
c. The company's policy is to write off any over/under-absorbed overhead to cost of goods sold. Will net income rise or fall this year when the over/under-absorbed overhead is written off to cost of goods sold?
PPX is a specialized packaging company that packages other manufacturers' products. Other manufacturers ship their products to PPX in bulk. PPX then packages the products using high-speed, state-of-the-art packaging machines and ships the packaged products to wholesalers. A typical order involves packaging small toys in see-through plastic and cardboard containers.
PPX uses a flexible budget to forecast annual plantwide overhead, which is then allocated to jobs based on machine hours. The annual flexible overhead budget is projected to be $6 million of fixed costs and $120 per machine hour. The budgeted number of machine hours for the year is 20,000.
At the end of the year, 21,000 machine hours were used and actual overhead incurred was $9.14 million.
Required:
a. Calculate the overhead rate set at the beginning of the year.
b. Calculate the amount of over/under-absorbed overhead for the year.
c. The company's policy is to write off any over/under-absorbed overhead to cost of goods sold. Will net income rise or fall this year when the over/under-absorbed overhead is written off to cost of goods sold?
Unlock Deck
Unlock for access to all 28 flashcards in this deck.
Unlock Deck
k this deck
27
DigitalEar invented and patented a new digital behind-the-ear hearing aid with adaptive noise reduction and automatic feedback cancellation. DigitalEar produces four different models of its DigitalEar device. The following table summarizes the planned production levels, costs, and selling prices for the four DigitalEar devices for this year:
DigitalEar allocates both fixed and variable manufacturing overhead to the four devices using a single overhead rate, which includes both fixed and variable manufacturing overhead. The number of direct labor hours in each device is used as the allocation base for assigning overhead to hearing aids. Budgeted volume measured using direct labor hours is calculated using the budgeted sales of each device. Variable manufacturing overhead is budgeted at $12.00 per direct labor hour and fixed manufacturing overhead is budgeted this year at $2,157,000.
Required:
a. Calculate DigitalEar's budgeted manufacturing overhead rate per direct labor hour for this year.
b. Using absorption costing, calculate the budgeted manufacturing cost per unit for each of DigitalEar's four hearing aid devices.
c. During the year, actual manufacturing overhead incurred (fixed plus variable) was $3,110,000, and the actual number of direct labor hours used producing the four hearing aids was: Calculate the over- or under-absorbed overhead DigitalEar for this year.
d. Assuming that the entire over- or under-absorbed overhead you calculated in part (c) is written off to cost of goods sold, does this write-off increase or decrease net income before taxes? Explain.
DigitalEar allocates both fixed and variable manufacturing overhead to the four devices using a single overhead rate, which includes both fixed and variable manufacturing overhead. The number of direct labor hours in each device is used as the allocation base for assigning overhead to hearing aids. Budgeted volume measured using direct labor hours is calculated using the budgeted sales of each device. Variable manufacturing overhead is budgeted at $12.00 per direct labor hour and fixed manufacturing overhead is budgeted this year at $2,157,000.
Required:
a. Calculate DigitalEar's budgeted manufacturing overhead rate per direct labor hour for this year.
b. Using absorption costing, calculate the budgeted manufacturing cost per unit for each of DigitalEar's four hearing aid devices.
c. During the year, actual manufacturing overhead incurred (fixed plus variable) was $3,110,000, and the actual number of direct labor hours used producing the four hearing aids was: Calculate the over- or under-absorbed overhead DigitalEar for this year.
d. Assuming that the entire over- or under-absorbed overhead you calculated in part (c) is written off to cost of goods sold, does this write-off increase or decrease net income before taxes? Explain.
Unlock Deck
Unlock for access to all 28 flashcards in this deck.
Unlock Deck
k this deck
28
Athletic Inc. is a wholesale distributor supplying a wide range of moderately priced sporting equipment to large chain stores. About 60 percent of Athletic's products are purchased from other companies and the remainder are manufactured by Athletic. The company has a plastics department that is currently manufacturing molded fishing tackle boxes. Athletic is able to manufacture and sell 8,000 tackle boxes annually, making full use of its direct labor capacity at available workstations. Presented below are the selling price and costs associated with Athletic's tackle boxes. Because Athletic believes it could sell 12,000 tackle boxes if it had sufficient manufacturing capacity, the company has looked into the possibility of purchasing the tackle boxes for distribution. Maple Products, a steady supplier of quality products, would be able to provide up to 9,000 tackle boxes per year at a price of $68 per box delivered to Athletic's facility.
Bart Johnson, Athletic's product manager, has suggested that the company could make better use of its plastics department by manufacturing skateboards. To support his position, Johnson has a market study that indicates an expanding market for skateboards and a need for additional suppliers. Johnson believes that Athletic could expect to sell 17,500 skateboards annually at $45 per skateboard. Johnson's estimate of the costs to manufacture the skateboards follows. In the plastics department, Athletic uses direct labor hours as the application base for manufacturing overhead. Included in manufacturing overhead for the current year is $50,000 of factorywide, fixed manufacturing overhead that has been allocated to the plastics department. For each product that Athletic sells, regardless of whether the product has been purchased or is manufactured by Athletic, a portion of the selling and administrative cost is fixed at $6 per unit. Total selling and administrative costs for the purchased tackle boxes would be $10 per unit.
Required:
Prepare an analysis based on the data presented that will show which product or products Athletic Inc. should manufacture and/or purchase to maximize the company's profitability. Show the associated financial impact. Support your answer with appropriate calculations.
Bart Johnson, Athletic's product manager, has suggested that the company could make better use of its plastics department by manufacturing skateboards. To support his position, Johnson has a market study that indicates an expanding market for skateboards and a need for additional suppliers. Johnson believes that Athletic could expect to sell 17,500 skateboards annually at $45 per skateboard. Johnson's estimate of the costs to manufacture the skateboards follows. In the plastics department, Athletic uses direct labor hours as the application base for manufacturing overhead. Included in manufacturing overhead for the current year is $50,000 of factorywide, fixed manufacturing overhead that has been allocated to the plastics department. For each product that Athletic sells, regardless of whether the product has been purchased or is manufactured by Athletic, a portion of the selling and administrative cost is fixed at $6 per unit. Total selling and administrative costs for the purchased tackle boxes would be $10 per unit.
Required:
Prepare an analysis based on the data presented that will show which product or products Athletic Inc. should manufacture and/or purchase to maximize the company's profitability. Show the associated financial impact. Support your answer with appropriate calculations.
Unlock Deck
Unlock for access to all 28 flashcards in this deck.
Unlock Deck
k this deck