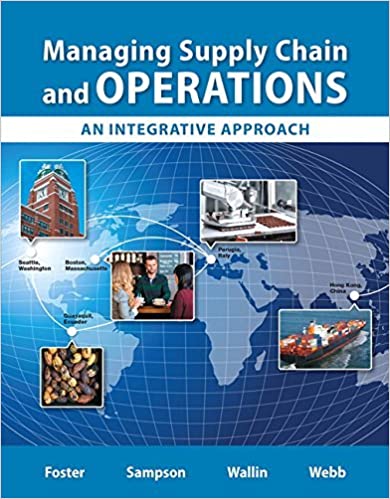
Managing Supply Chain and Operations 1st Edition by Thomas Foster ,Scott Sampson,Cynthia Wallin,Scott Webb
Edition 1ISBN: 9780134110219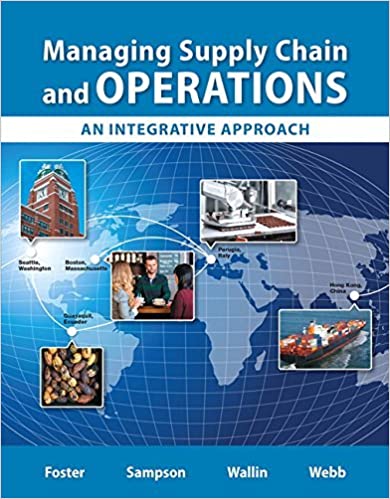
Managing Supply Chain and Operations 1st Edition by Thomas Foster ,Scott Sampson,Cynthia Wallin,Scott Webb
Edition 1ISBN: 9780134110219 Exercise 7
Trudy Johnson had only recently graduated from the supply chain management program at her state university when she accepted a position as a logistics analyst with Brentward Logistics. Trudy was excited about her new position and believed that she brought a solid set of skills related to logistics and supply chain management to Brentward. Shortly after she started, she was assigned to be a member of a team that was confronted with two challenges: (1) identify the best location for a warehouse that would be storing and shipping component parts to the five manufacturing plants the company owned and operated, and (2) identify where a new warehouse should be located to increase shipping capacity while minimizing total costs for supplying finished manufactured items produced by the company to large industrial customers located around the United States.
Trudy quickly went to work collecting information that she believed could help the team analyze the two issues it faced. For the warehouse location problem, she collected information related to the locations of the existing plants that would be supplied by the new warehouse as well as an estimate of the number of deliveries (measured in truckloads) that would take place each week from the new warehouse to the plants. This information is shown below with x and y as the Cartesian coordinates of the existing plants and daily shipments being the estimated number of truck deliveries from the warehouse to the plants estimated to be required weekly:
The team had previously identified two potential locations for the finished goods inventory warehouse. This warehouse would ship items to large industrial customers located in six V.S. cities. Currently, the company has three warehouses that could ship finished products to customers. The estimated weekly demands from the customers and the weekly shipping capacity from the warehouses are as follows:
The current warehouses do not have sufficient capacity to meet the weekly demand. Furthermore, it is not possible to expand the capacity of the existing warehouses. Conse-quently … new warehouse must be built to meet customer needs. The team has identified two potential new warehouse locations: Dallas and Albuquerque. The projected capacity of the Albuquerque warehouse would be 150 units weekly. The Dallas warehouse has greater shipping options and could be built to a shipping capacity of 200 units weekly. Trudy collected the following actual costs per unit to ship from the existing warehouses to customers and the expected shipping costs for the proposed sites:
Questions
1. As only one warehouse can be built, assist Trudy in finding the best location.
2. What is the minimum transportation cost comparing the Albuquerque option to the Dallas option?
Trudy quickly went to work collecting information that she believed could help the team analyze the two issues it faced. For the warehouse location problem, she collected information related to the locations of the existing plants that would be supplied by the new warehouse as well as an estimate of the number of deliveries (measured in truckloads) that would take place each week from the new warehouse to the plants. This information is shown below with x and y as the Cartesian coordinates of the existing plants and daily shipments being the estimated number of truck deliveries from the warehouse to the plants estimated to be required weekly:
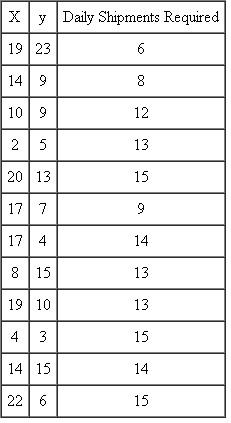
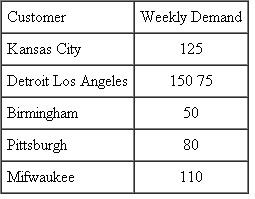
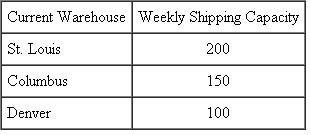
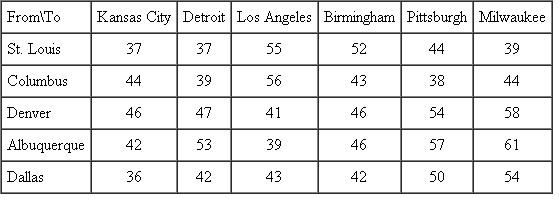
1. As only one warehouse can be built, assist Trudy in finding the best location.
2. What is the minimum transportation cost comparing the Albuquerque option to the Dallas option?
Explanation
Brief summary of the case:
Person T is ...
Managing Supply Chain and Operations 1st Edition by Thomas Foster ,Scott Sampson,Cynthia Wallin,Scott Webb
Why don’t you like this exercise?
Other Minimum 8 character and maximum 255 character
Character 255