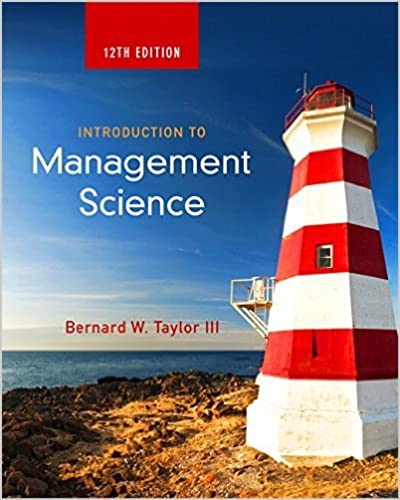
Introduction to Management Science 12th Edition by Bernard Taylor
Edition 12ISBN: 978-0133778847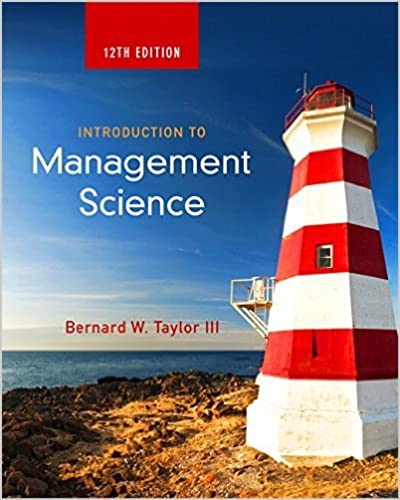
Introduction to Management Science 12th Edition by Bernard Taylor
Edition 12ISBN: 978-0133778847 Exercise 45
In Problem in Chapter, the supplier receives shipments of partially completed laptops from its manufacturing facility in Southeast Asia, which has maximum production rate of 200 units per day. Using the forecast of annual demand developed in that problem, an annual carrying cost of $115.75 (which includes an average obsolescence cost), a shipping cost from Asia of $6,500 per shipment, and a lead time for receiving an order of 25 days, determine the optimal order size, the minimum total annual inventory cost, the maximum inventory level, and the reorder point (given that the Bell assembly operation operates 365 days per year).
Problem
Bell Inc. is a computer company that gets most of its component parts from suppliers in Southeast Asia, who ship to small warehouses called "revolvers" (for revolving inventory) near Bell's main assembly plants near Fort Worth, Texas. Bell withdraws inventory for these warehouses every few hours, and most of Bell's suppliers deliver to their revolvers every 3 or 4 days. One particular supplier provides most of the workings for the Bell Intrepid laptop, including the screen and keyboard, and the hard drive and mother board plus a few other parts are added at the assembly plant. These revolvers allow Bell to carry little of its own inventory by pushing it down to its suppliers. However, the supplier also wants to minimize its inventory, and one way it can do that is to develop an accurate demand forecast. Following is the supplier's demand data (units) from Bell for the past 24 months:
Closely observe the demand data and develop a forecast model for year 3 that you believe will be accurate.
Problem
Bell Inc. is a computer company that gets most of its component parts from suppliers in Southeast Asia, who ship to small warehouses called "revolvers" (for revolving inventory) near Bell's main assembly plants near Fort Worth, Texas. Bell withdraws inventory for these warehouses every few hours, and most of Bell's suppliers deliver to their revolvers every 3 or 4 days. One particular supplier provides most of the workings for the Bell Intrepid laptop, including the screen and keyboard, and the hard drive and mother board plus a few other parts are added at the assembly plant. These revolvers allow Bell to carry little of its own inventory by pushing it down to its suppliers. However, the supplier also wants to minimize its inventory, and one way it can do that is to develop an accurate demand forecast. Following is the supplier's demand data (units) from Bell for the past 24 months:
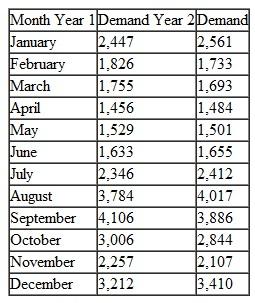
Explanation
Optimal Production Run Quantity
The Opt...
Introduction to Management Science 12th Edition by Bernard Taylor
Why don’t you like this exercise?
Other Minimum 8 character and maximum 255 character
Character 255