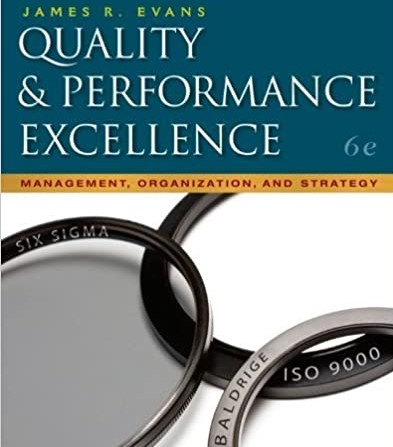
Quality & Performance Excellence 6th Edition by James Evans
Edition 6ISBN: 978-0324827064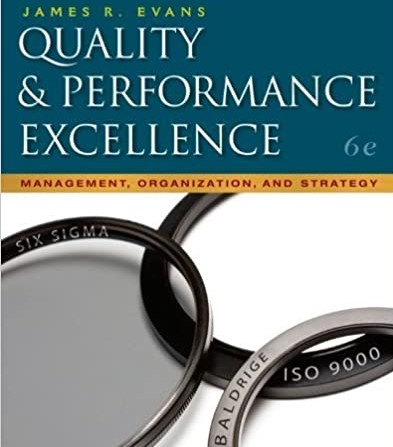
Quality & Performance Excellence 6th Edition by James Evans
Edition 6ISBN: 978-0324827064 Exercise 6
Case of the Rotary Compressor
In 1981, market share and profits in General Electric's appliance division were falling. The company's technology was antiquated compared to foreign competitors. For example, making refrigerator compressors required 65 minutes of labor in comparison to 25 minutes for competitors in Japan and Italy. Moreover, GE's labor costs were higher. The alternatives were obvious: either purchase compressors from Japan or Italy or design and build a better model.
By 1983, the decision to build a new rotary com-pressor in-house was made, along with a commitment for a new 5120 million factory. GE was not a novice in rotary compressor technology; they had invented it and had been using it in air conditioners for many years. A rotary compressor weighed less, had one-third fewer parts, and was more energy efficient than the current reciprocating compressors. The rotary compressor took up less space, thus providing more room inside the refrigerator and better meeting customer requirements.
Some engineers argued to the contrary, citing the fact that rotary compressors nut hotter. This is not a problem in most air conditioners, because the coolant cools the compressor. In a refrigerator, however, the coolant flows only one-tenth as fast, and the unit runs about four times longer in one year than an air conditioner. GE had problems with the early rotary compressors in air conditioners. Although the bugs had been eliminated in smaller units, GE quit using rotaries in larger units due to frequent breakdowns in hot climates. GE managers and design engineers were concerned about other issues.
Rotary compressors make a high-pitched whine, and managers were afraid that this would adversely affect consumer acceptance. Managers and consumer test panels spent many hours on this issue. The new design also required key parts to work together with a tolerance of only 50 millionths of an inch. Nothing had been mass-produced with such precision before, but manufacturing engineers felt sure they could do it.
The compressor they finally designed was nearly identical to that used in air conditioners, with one change. Two small parts inside the compressor were made out of powdered metal, rather than the hardened steel and cast iron used in air conditioners. This material was chosen because it could be machined to much closer tolerances, and it reduced machining costs. Powdered metal had been tried a decade earlier on air conditioners but did not work. The design engineers who were new to designing Compressors did not consider the earlier failure important.
A consultant suggested that GE consider a joint venture with a Japanese company that had a rotary refrigerator compressor already on the market. The idea was rejected by management. The original designer of the air conditioner rotary compressor, who had left GE, offered his services as a consultant. GE declined his offer, writing him that they had sufficient technical expertise.
About 600 compressors were tested in 1983 with-out a single failure. They were run continuously for two months under elevated temperatures and pressures that were supposed to simulate five years' operation. GE normally conducts extensive field testing of new products; their original plan to test models in the field for two years was reduced to nine months because of time pressure to complete the project.
The technician who disassembled and inspected the pans thought they did not look right. Pans of the motor were discolored, a sign of excessive heat. Bearings were worn, and it appeared that high heat was breaking down the lubricating oil. The technician's supervisors discounted these findings and did not relay them ro upper levels of management. Another consultant who evaluated the test results believed that something was wrong because only one failure was found in two years and recommended that rest :auditions be intensified. This suggestion was also rejected by management.
By 1986, only two and a half years after board approval, the new factory was producing compressors at a rate of 10 per minute. By the end of the year, more than one million had been produced. Market share rose and the new refrigerator appeared to be a success. Bat in July 1987 the first compressor failed. Soon after, reports of other failures in Puerto Rico arrived. By September the appliance division knew it had a major problem. In December the plant stopped making the compressor. Not until 1988 was the problem diagnosed as excessive wear in the two powdered-metal parts that burned up the oil. The cost in 1989 alone was $450 million. By mid-1990, GE had voluntarily replaced nearly 1.1 million compressors with ones purchased from six suppliers, five of them foreign.
Discussion Questions
On what basis was GE attempting to achieve a competitive advantage How did they fail
In 1981, market share and profits in General Electric's appliance division were falling. The company's technology was antiquated compared to foreign competitors. For example, making refrigerator compressors required 65 minutes of labor in comparison to 25 minutes for competitors in Japan and Italy. Moreover, GE's labor costs were higher. The alternatives were obvious: either purchase compressors from Japan or Italy or design and build a better model.
By 1983, the decision to build a new rotary com-pressor in-house was made, along with a commitment for a new 5120 million factory. GE was not a novice in rotary compressor technology; they had invented it and had been using it in air conditioners for many years. A rotary compressor weighed less, had one-third fewer parts, and was more energy efficient than the current reciprocating compressors. The rotary compressor took up less space, thus providing more room inside the refrigerator and better meeting customer requirements.
Some engineers argued to the contrary, citing the fact that rotary compressors nut hotter. This is not a problem in most air conditioners, because the coolant cools the compressor. In a refrigerator, however, the coolant flows only one-tenth as fast, and the unit runs about four times longer in one year than an air conditioner. GE had problems with the early rotary compressors in air conditioners. Although the bugs had been eliminated in smaller units, GE quit using rotaries in larger units due to frequent breakdowns in hot climates. GE managers and design engineers were concerned about other issues.
Rotary compressors make a high-pitched whine, and managers were afraid that this would adversely affect consumer acceptance. Managers and consumer test panels spent many hours on this issue. The new design also required key parts to work together with a tolerance of only 50 millionths of an inch. Nothing had been mass-produced with such precision before, but manufacturing engineers felt sure they could do it.
The compressor they finally designed was nearly identical to that used in air conditioners, with one change. Two small parts inside the compressor were made out of powdered metal, rather than the hardened steel and cast iron used in air conditioners. This material was chosen because it could be machined to much closer tolerances, and it reduced machining costs. Powdered metal had been tried a decade earlier on air conditioners but did not work. The design engineers who were new to designing Compressors did not consider the earlier failure important.
A consultant suggested that GE consider a joint venture with a Japanese company that had a rotary refrigerator compressor already on the market. The idea was rejected by management. The original designer of the air conditioner rotary compressor, who had left GE, offered his services as a consultant. GE declined his offer, writing him that they had sufficient technical expertise.
About 600 compressors were tested in 1983 with-out a single failure. They were run continuously for two months under elevated temperatures and pressures that were supposed to simulate five years' operation. GE normally conducts extensive field testing of new products; their original plan to test models in the field for two years was reduced to nine months because of time pressure to complete the project.
The technician who disassembled and inspected the pans thought they did not look right. Pans of the motor were discolored, a sign of excessive heat. Bearings were worn, and it appeared that high heat was breaking down the lubricating oil. The technician's supervisors discounted these findings and did not relay them ro upper levels of management. Another consultant who evaluated the test results believed that something was wrong because only one failure was found in two years and recommended that rest :auditions be intensified. This suggestion was also rejected by management.
By 1986, only two and a half years after board approval, the new factory was producing compressors at a rate of 10 per minute. By the end of the year, more than one million had been produced. Market share rose and the new refrigerator appeared to be a success. Bat in July 1987 the first compressor failed. Soon after, reports of other failures in Puerto Rico arrived. By September the appliance division knew it had a major problem. In December the plant stopped making the compressor. Not until 1988 was the problem diagnosed as excessive wear in the two powdered-metal parts that burned up the oil. The cost in 1989 alone was $450 million. By mid-1990, GE had voluntarily replaced nearly 1.1 million compressors with ones purchased from six suppliers, five of them foreign.
Discussion Questions
On what basis was GE attempting to achieve a competitive advantage How did they fail
Explanation
The organization was attempting to gain ...
Quality & Performance Excellence 6th Edition by James Evans
Why don’t you like this exercise?
Other Minimum 8 character and maximum 255 character
Character 255