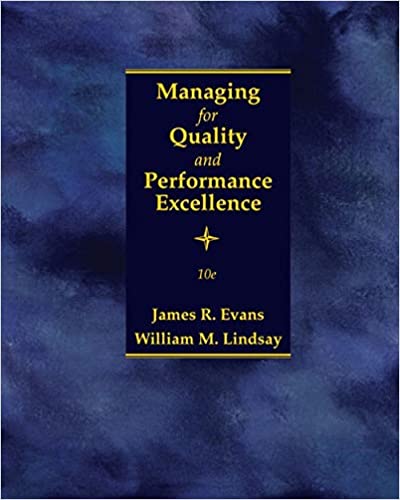
Managing for Quality and Performance Excellence 10th Edition by James Evans ,William Lindsay
Edition 10ISBN: 978-1305662544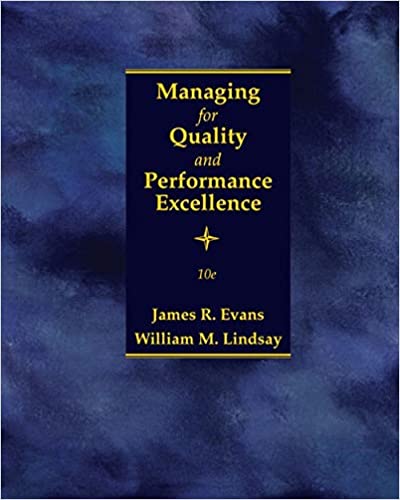
Managing for Quality and Performance Excellence 10th Edition by James Evans ,William Lindsay
Edition 10ISBN: 978-1305662544 Exercise 17
Lexus automobiles have consistently led the industry in quality. In 2000, Cambridge, Ontario, was chosen as the site of the first Lexus plant outside Japan, designated to build the RX 330 SUV. The assistant general manager for manufacturing observed, "We understood from the beginning that to be accepted we had to be not just as good as but better than Kyushu [the location of the Lexus plant in Japan]."
Teamwork at Cambridge starts with teaching workers about every stage of the production process, and about the duties of other team members. Not only does this reinforce the idea that each job is important, but it increases motivation: Each team member does his or her job better if he or she understands how other jobs are done and how one job affects another. This is all part of the kaizen philosophy, which at Cambridge is all about the many small inventions masterminded by team members on the line. Most are simple ideas that would occur only to a person doing the job-a clip to hold a part, say, or a jig or template to protect a part from damage, or the replacement of several parts by one. (These inventions are themselves called kaizens.)
In order to foster this mindset, engineers and managers created an environment like a clean room, brightly lit like a pharmaceutical laboratory, with a place for everything and everything in its place. Traditional automobile factories are dark and noisy places, filled with flying sparks and the pounding of metal stamping machines. The Cambridge plant, by contrast, is painted in light colors (coordinated by an interior designer) and boasts a spotless floor-the result of constant sweeping up with small brooms and dustpans. These come from "5s" stations, a key element of lean production (see Chapter 9). Cleanliness plays such a large role because at a typical automobile plant most defects are caused by the process of manufacturing itself, by bumps and scrapes from workers. That's why there are no rings or watches on the line at Cambridge, no jeans with rivets to scratch bodies, and why fragments of metal are swept up before they can infiltrate the paint system. The Lexus philosophy is based on the fundamental insight that quality must be built into each part of the production process, not applied as an afterthought through inspections or fixes. Each worker is also a quality control inspector of his or her own work and that of his or her fellow team members-entrusted with the task of eliminating defects before they move down the line.
In the service of this ideal, computer monitors high above the plant's floor display the status of production at each point. Pulling a cord allows team members to stop the line entirely, if necessary. When this happens, the news is indicated by towers of lights, and by characteristic brief musical tones unique to each station, like personal cell phone rings. At the Cambridge plant, Lexus has taken this quality control to a new level, with the introduction of "quality gates": checkpoints where items found to be of particular concern to customers (such as flawless vertical paint surfaces and the fit of headlights into the body of the vehicle) are noted and evaluated. At the welding area's quality gate, for example, welds are tested with hammer and chisel and alignments measured with jigs. Team members certify each vehicle's weld integrity by applying their initials in bright colors. These personal testimonials to care and quality will ride with the vehicles for their lifetimes, albeit under coats of paint or hidden away from the customer's eye. Then, at the end of the welding process, the bodies receive an even closer inspection, distinguished by that special human touch that makes Lexus so rare among car companies. Under an angled roof made up of light tubes, team members sweep their hands carefully across every inch of the vehicles' exteriors. With small, black abrasive squares in their gloved hands, they smooth out any remaining spots or irregularities.
Once welded, vehicle bodies move to the paint shop, more spotless than any other part of the plant. It has the air of a Silicon Valley clean room. Team members wear special antistatic suits. Two sets of doors make an airlock to the paint area. Downdrafts and grated walkways with water beneath catch particles of lint and dust. No cardboard is allowed anywhere in the area. Each vehicle body is vacuumed to remove metal shavings. And the basecoats themselves -the key paint layers that give vehicles their colors-are made of a water-soluble paint, not environmentally hazardous solvents. Spraying is carried out by robotic arms grasping cartridges of measured paint. The cartridges hold just enough paint for one vehicle and are refilled. This allows for mixing colors on the line-no longer must a batch of blue or red vehicles be run together. Finally, a machine called a Perceptron, which measures the changing reflection of light on the vehicle's surface, a rippling effect called "orange peel"-tests for gloss and smoothness.
After painting comes assembly. Here the focus is on the fit and finish of doors, windows, and other key items, such as interior accent pieces. Doors are removed early in the assembly process and make their own course through the plant before rejoining the body-always the same body, of course. This affords access to the inside of the vehicle and protects the door leather and wood from damage. To install the headliner-the large single piece in the ceiling-a team member is swung inside the vehicle in a clever little seat on an arm, called a Raku. Then there are the interior detail items, such as wood paneling. Each vehicle comes with sets of wooden parts that are cut from the same log, and then stained and finished together. If a wood component is damaged in assembly, all the other pieces from its set are replaced as well.
At the end of the line, on a typical day, one vehicle sits in a steady rainstorm, undergoing weatherproof testing. Two others are installed in bays for what are known as "shipping quality audits"-where random vehicles are chosen for an extra-close, no-holds-barred, semi-surgical inspection. The finished RX 330s then run through a test track with bumps and curves. A driver speeds, then brakes, then takes his hands off the wheel to be sure the new vehicles don't pull to one side or the other. Eventually, they'll board the railcars ready to carry them off to a distant city and a new owner. As for Cambridge surpassing Japan, so far they're on track: they're even sending kaizens back to Kyushu.
What lessons or best practices might be learned and applied to other companies (outside of the automotive industry)?
Teamwork at Cambridge starts with teaching workers about every stage of the production process, and about the duties of other team members. Not only does this reinforce the idea that each job is important, but it increases motivation: Each team member does his or her job better if he or she understands how other jobs are done and how one job affects another. This is all part of the kaizen philosophy, which at Cambridge is all about the many small inventions masterminded by team members on the line. Most are simple ideas that would occur only to a person doing the job-a clip to hold a part, say, or a jig or template to protect a part from damage, or the replacement of several parts by one. (These inventions are themselves called kaizens.)
In order to foster this mindset, engineers and managers created an environment like a clean room, brightly lit like a pharmaceutical laboratory, with a place for everything and everything in its place. Traditional automobile factories are dark and noisy places, filled with flying sparks and the pounding of metal stamping machines. The Cambridge plant, by contrast, is painted in light colors (coordinated by an interior designer) and boasts a spotless floor-the result of constant sweeping up with small brooms and dustpans. These come from "5s" stations, a key element of lean production (see Chapter 9). Cleanliness plays such a large role because at a typical automobile plant most defects are caused by the process of manufacturing itself, by bumps and scrapes from workers. That's why there are no rings or watches on the line at Cambridge, no jeans with rivets to scratch bodies, and why fragments of metal are swept up before they can infiltrate the paint system. The Lexus philosophy is based on the fundamental insight that quality must be built into each part of the production process, not applied as an afterthought through inspections or fixes. Each worker is also a quality control inspector of his or her own work and that of his or her fellow team members-entrusted with the task of eliminating defects before they move down the line.
In the service of this ideal, computer monitors high above the plant's floor display the status of production at each point. Pulling a cord allows team members to stop the line entirely, if necessary. When this happens, the news is indicated by towers of lights, and by characteristic brief musical tones unique to each station, like personal cell phone rings. At the Cambridge plant, Lexus has taken this quality control to a new level, with the introduction of "quality gates": checkpoints where items found to be of particular concern to customers (such as flawless vertical paint surfaces and the fit of headlights into the body of the vehicle) are noted and evaluated. At the welding area's quality gate, for example, welds are tested with hammer and chisel and alignments measured with jigs. Team members certify each vehicle's weld integrity by applying their initials in bright colors. These personal testimonials to care and quality will ride with the vehicles for their lifetimes, albeit under coats of paint or hidden away from the customer's eye. Then, at the end of the welding process, the bodies receive an even closer inspection, distinguished by that special human touch that makes Lexus so rare among car companies. Under an angled roof made up of light tubes, team members sweep their hands carefully across every inch of the vehicles' exteriors. With small, black abrasive squares in their gloved hands, they smooth out any remaining spots or irregularities.
Once welded, vehicle bodies move to the paint shop, more spotless than any other part of the plant. It has the air of a Silicon Valley clean room. Team members wear special antistatic suits. Two sets of doors make an airlock to the paint area. Downdrafts and grated walkways with water beneath catch particles of lint and dust. No cardboard is allowed anywhere in the area. Each vehicle body is vacuumed to remove metal shavings. And the basecoats themselves -the key paint layers that give vehicles their colors-are made of a water-soluble paint, not environmentally hazardous solvents. Spraying is carried out by robotic arms grasping cartridges of measured paint. The cartridges hold just enough paint for one vehicle and are refilled. This allows for mixing colors on the line-no longer must a batch of blue or red vehicles be run together. Finally, a machine called a Perceptron, which measures the changing reflection of light on the vehicle's surface, a rippling effect called "orange peel"-tests for gloss and smoothness.
After painting comes assembly. Here the focus is on the fit and finish of doors, windows, and other key items, such as interior accent pieces. Doors are removed early in the assembly process and make their own course through the plant before rejoining the body-always the same body, of course. This affords access to the inside of the vehicle and protects the door leather and wood from damage. To install the headliner-the large single piece in the ceiling-a team member is swung inside the vehicle in a clever little seat on an arm, called a Raku. Then there are the interior detail items, such as wood paneling. Each vehicle comes with sets of wooden parts that are cut from the same log, and then stained and finished together. If a wood component is damaged in assembly, all the other pieces from its set are replaced as well.
At the end of the line, on a typical day, one vehicle sits in a steady rainstorm, undergoing weatherproof testing. Two others are installed in bays for what are known as "shipping quality audits"-where random vehicles are chosen for an extra-close, no-holds-barred, semi-surgical inspection. The finished RX 330s then run through a test track with bumps and curves. A driver speeds, then brakes, then takes his hands off the wheel to be sure the new vehicles don't pull to one side or the other. Eventually, they'll board the railcars ready to carry them off to a distant city and a new owner. As for Cambridge surpassing Japan, so far they're on track: they're even sending kaizens back to Kyushu.
What lessons or best practices might be learned and applied to other companies (outside of the automotive industry)?
Explanation
Facts:
In 2000, country C was selected ...
Managing for Quality and Performance Excellence 10th Edition by James Evans ,William Lindsay
Why don’t you like this exercise?
Other Minimum 8 character and maximum 255 character
Character 255