Deck 13: Resource Management
Question
Question
Question
Question
Question
Question
Question
Question
Question
Question
Question
Question
Question
Question
Question
Question
Question
Question
Question
Question
Question
Question
Question
Question
Question
Question
Question
Question
Question
Question
Question
Question
Question
Question
Question
Question
Question
Question
Question
Question
Question
Question
Question
Question
Question
Question
Question
Question
Question
Question
Question
Question
Question
Question
Question
Question
Question
Question
Question
Question
Question
Question
Question
Question
Question
Question
Question
Question
Question
Question
Question
Question
Question
Question
Question
Question
Question
Question
Question
Question
Unlock Deck
Sign up to unlock the cards in this deck!
Unlock Deck
Unlock Deck
1/106
Play
Full screen (f)
Deck 13: Resource Management
1
Determine the net requirement for E if the gross requirement for A is still 200 and current on-hand inventory balance for A is 60, D is 200, E is 100, and F is 600.
A) Less than or equal to 1,000 units
B) Greater than 1,000 but less than or equal to 1,500 units
C) Greater than 1,500 but less than or equal to 2,000 units
D) Greater than 2,000 but less than or equal to 2,500 units
A) Less than or equal to 1,000 units
B) Greater than 1,000 but less than or equal to 1,500 units
C) Greater than 1,500 but less than or equal to 2,000 units
D) Greater than 2,000 but less than or equal to 2,500 units
A
2
The Academic Company mixes and bottles a high-energy beverage in various container types and sizes for college students. The aggregate forecast for the next four quarters (1 year) in thousands of gallons is as follows:
Table 1
Academic's management makes the following assumptions:
Each employee works 550 standard hours of regular time each quarter.
On average, it takes 27 hours to produce and package 1 unit (1,000 gallons).
Regular-time labor costs $6.00/hour; overtime labor costs $9.00/hour.
Inventory-holding cost is approximately $4.50/unit (1,000 gallons) per quarter based upon the ending inventory per quarter.
Because of extremely hot weather, there is no beginning inventory available to start Quarter 1.
Management wants a constant work force (no hiring or firing).
Managers have also decided to always round up the number of employees needed to the next whole integer, i.e., 37.2 yields 38 employees.
______________________________________________________________________________
-Using the data in Table 1, if management will allow a maximum of 30 percent overtime, how many workers are needed for Quarter 3?
A) 29
B) 33
C) 35
D) 40
Table 1
Academic's management makes the following assumptions:
Each employee works 550 standard hours of regular time each quarter.
On average, it takes 27 hours to produce and package 1 unit (1,000 gallons).
Regular-time labor costs $6.00/hour; overtime labor costs $9.00/hour.
Inventory-holding cost is approximately $4.50/unit (1,000 gallons) per quarter based upon the ending inventory per quarter.
Because of extremely hot weather, there is no beginning inventory available to start Quarter 1.
Management wants a constant work force (no hiring or firing).
Managers have also decided to always round up the number of employees needed to the next whole integer, i.e., 37.2 yields 38 employees.
______________________________________________________________________________
-Using the data in Table 1, if management will allow a maximum of 30 percent overtime, how many workers are needed for Quarter 3?
A) 29
B) 33
C) 35
D) 40
33
3
The Academic Company mixes and bottles a high-energy beverage in various container types and sizes for college students. The aggregate forecast for the next four quarters (1 year) in thousands of gallons is as follows:
Table 1
Academic's management makes the following assumptions:
Each employee works 550 standard hours of regular time each quarter.
On average, it takes 27 hours to produce and package 1 unit (1,000 gallons).
Regular-time labor costs $6.00/hour; overtime labor costs $9.00/hour.
Inventory-holding cost is approximately $4.50/unit (1,000 gallons) per quarter based upon the ending inventory per quarter.
Because of extremely hot weather, there is no beginning inventory available to start Quarter 1.
Management wants a constant work force (no hiring or firing).
Managers have also decided to always round up the number of employees needed to the next whole integer, i.e., 37.2 yields 38 employees.
______________________________________________________________________________
-Using the information given in Table 1, determine how many employees would be needed to meet the peak demand in Quarter 3.
A) 32
B) 21
C) 50
D) 42
Table 1
Academic's management makes the following assumptions:
Each employee works 550 standard hours of regular time each quarter.
On average, it takes 27 hours to produce and package 1 unit (1,000 gallons).
Regular-time labor costs $6.00/hour; overtime labor costs $9.00/hour.
Inventory-holding cost is approximately $4.50/unit (1,000 gallons) per quarter based upon the ending inventory per quarter.
Because of extremely hot weather, there is no beginning inventory available to start Quarter 1.
Management wants a constant work force (no hiring or firing).
Managers have also decided to always round up the number of employees needed to the next whole integer, i.e., 37.2 yields 38 employees.
______________________________________________________________________________
-Using the information given in Table 1, determine how many employees would be needed to meet the peak demand in Quarter 3.
A) 32
B) 21
C) 50
D) 42
42
4
If A has a gross requirement to build 250 units and an on-hand inventory for A of 40, determine the net requirement for D if its current on-hand inventory balance for D is 200 (all other components have no (zero) current inventory).
A)Less than or equal to 1,000 units
B)Greater than 1,000 but less than or equal to 1,500 units
C)Greater than 1,500 but less than or equal to 2,000 units
D)Greater than 2,000 but less than or equal to 2,500 units
A)Less than or equal to 1,000 units
B)Greater than 1,000 but less than or equal to 1,500 units
C)Greater than 1,500 but less than or equal to 2,000 units
D)Greater than 2,000 but less than or equal to 2,500 units
Unlock Deck
Unlock for access to all 106 flashcards in this deck.
Unlock Deck
k this deck
5
The bill of material (BOM) for Products A and B are shown below followed by a table of inventory data (called Exhibit 1). The master production scheduling (MPS) for A calls for 150 units of A to be completed in Week 4 and another 225 units to be completed in Week 5. End item A has a two-week lead time. The MPS calls for 400 units of B to be completed in Week 6. End item B has a one-week lead time.
Exhibit 1
____________________________________________________________________
-Using the data given in Exhibit 1, determine the timing and amount of the planned order receipt for Item E.
A) Week 1; 1,800 units
B) Week 3; 1,900 units
C) Week 2; 2,250 units
D) Week 2; 3,850 units
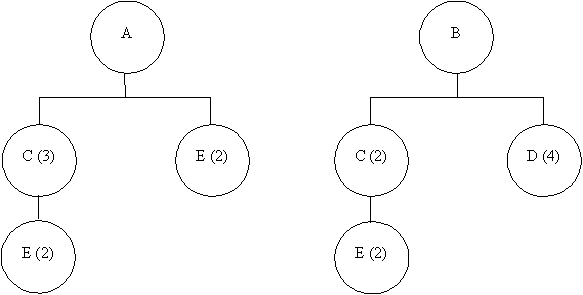
____________________________________________________________________
-Using the data given in Exhibit 1, determine the timing and amount of the planned order receipt for Item E.
A) Week 1; 1,800 units
B) Week 3; 1,900 units
C) Week 2; 2,250 units
D) Week 2; 3,850 units
Unlock Deck
Unlock for access to all 106 flashcards in this deck.
Unlock Deck
k this deck
6
A paint company has the following aggregate demand requirements and cost data for the upcoming year by quarter.
Table 2
____________________________________________________________________
-Using the data in Table 2, determine the inventory holding and backorder costs for the year if the paint company wants to use a pure level strategy, ending Quarter 4 with no inventory.
A) $8,400
B) $32,400
C) $28,500
D) $27,600
Table 2
____________________________________________________________________
-Using the data in Table 2, determine the inventory holding and backorder costs for the year if the paint company wants to use a pure level strategy, ending Quarter 4 with no inventory.
A) $8,400
B) $32,400
C) $28,500
D) $27,600
Unlock Deck
Unlock for access to all 106 flashcards in this deck.
Unlock Deck
k this deck
7
The bill of material (BOM) for Products A and B are shown below followed by a table of inventory data (called Exhibit 1). The master production scheduling (MPS) for A calls for 150 units of A to be completed in Week 4 and another 225 units to be completed in Week 5. End item A has a two-week lead time. The MPS calls for 400 units of B to be completed in Week 6. End item B has a one-week lead time.
Exhibit 1
____________________________________________________________________
-Using the data given in Exhibit 1, determine the projected on-hand inventory for Item C, beginning in Week 8.
A) 800 units
B) 645 units
C) 155 units
D) 0 units
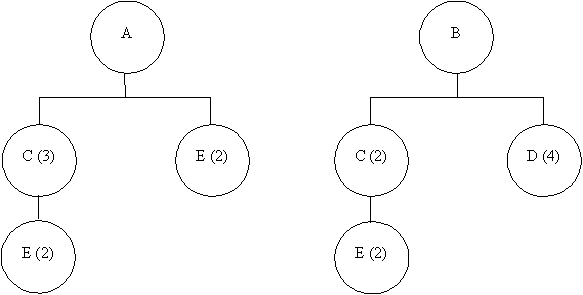
____________________________________________________________________
-Using the data given in Exhibit 1, determine the projected on-hand inventory for Item C, beginning in Week 8.
A) 800 units
B) 645 units
C) 155 units
D) 0 units
Unlock Deck
Unlock for access to all 106 flashcards in this deck.
Unlock Deck
k this deck
8
Determine the net requirement for E if the gross requirement for A is still 250, and current on-hand inventory balance for A is 40, D is 200, E is 300, and F is 600.
A) Less than or equal to 1,000 units
B) Greater than 1,000 but less than or equal to 1,500 units
C) Greater than 1,500 but less than or equal to 2,000 units
D) Greater than 2,000 but less than or equal to 2,500 units
A) Less than or equal to 1,000 units
B) Greater than 1,000 but less than or equal to 1,500 units
C) Greater than 1,500 but less than or equal to 2,000 units
D) Greater than 2,000 but less than or equal to 2,500 units
Unlock Deck
Unlock for access to all 106 flashcards in this deck.
Unlock Deck
k this deck
9
A paint company has the following aggregate demand requirements and cost data for the upcoming year by quarter.
Table 2
____________________________________________________________________
-Using the information in Table 2, determine the change in workforce costs (hiring and firing employees) if the paint company decides to use a chase strategy.
A) $93,000
B) $84,000
C) $280,000
D) $30,000
Table 2
____________________________________________________________________
-Using the information in Table 2, determine the change in workforce costs (hiring and firing employees) if the paint company decides to use a chase strategy.
A) $93,000
B) $84,000
C) $280,000
D) $30,000
Unlock Deck
Unlock for access to all 106 flashcards in this deck.
Unlock Deck
k this deck
10
The Academic Company mixes and bottles a high-energy beverage in various container types and sizes for college students. The aggregate forecast for the next four quarters (1 year) in thousands of gallons is as follows:
Table 1
Academic's management makes the following assumptions:
Each employee works 550 standard hours of regular time each quarter.
On average, it takes 27 hours to produce and package 1 unit (1,000 gallons).
Regular-time labor costs $6.00/hour; overtime labor costs $9.00/hour.
Inventory-holding cost is approximately $4.50/unit (1,000 gallons) per quarter based upon the ending inventory per quarter.
Because of extremely hot weather, there is no beginning inventory available to start Quarter 1.
Management wants a constant work force (no hiring or firing).
Managers have also decided to always round up the number of employees needed to the next whole integer, i.e., 37.2 yields 38 employees.
______________________________________________________________________________
-Using the data in Table 1 and a level schedule of 650 units per quarter, what will be the annual employee costs?
A) $105,600
B) $554,400
C) $421,200
D) $369,600
Table 1
Academic's management makes the following assumptions:
Each employee works 550 standard hours of regular time each quarter.
On average, it takes 27 hours to produce and package 1 unit (1,000 gallons).
Regular-time labor costs $6.00/hour; overtime labor costs $9.00/hour.
Inventory-holding cost is approximately $4.50/unit (1,000 gallons) per quarter based upon the ending inventory per quarter.
Because of extremely hot weather, there is no beginning inventory available to start Quarter 1.
Management wants a constant work force (no hiring or firing).
Managers have also decided to always round up the number of employees needed to the next whole integer, i.e., 37.2 yields 38 employees.
______________________________________________________________________________
-Using the data in Table 1 and a level schedule of 650 units per quarter, what will be the annual employee costs?
A) $105,600
B) $554,400
C) $421,200
D) $369,600
Unlock Deck
Unlock for access to all 106 flashcards in this deck.
Unlock Deck
k this deck
11
A company currently has no items in inventory. The demand for the next four months is 200, 400, 250, and 350 units. Determine the level production rate if a level strategy is selected with the goal of ending Period 4 with 100 units in inventory.
A) 300
B) 325
C) 450
D) 350
A) 300
B) 325
C) 450
D) 350
Unlock Deck
Unlock for access to all 106 flashcards in this deck.
Unlock Deck
k this deck
12
Aggregate planning:
A) is not driven by forecasts.
B) includes detailed staff schedules.
C) defines budget and associated resource requirements.
D) is used to develop detailed short-term plans and establish shop floor control.
A) is not driven by forecasts.
B) includes detailed staff schedules.
C) defines budget and associated resource requirements.
D) is used to develop detailed short-term plans and establish shop floor control.
Unlock Deck
Unlock for access to all 106 flashcards in this deck.
Unlock Deck
k this deck
13
A paint company has the following aggregate demand requirements and cost data for the upcoming year by quarter.
Table 2
____________________________________________________________________
-Using the data in Table 2 and assuming the level strategy, determine the change in production costs for the year.
A) $0 (none)
B) $35,000
C) $15,000
D) $27,600
Table 2
____________________________________________________________________
-Using the data in Table 2 and assuming the level strategy, determine the change in production costs for the year.
A) $0 (none)
B) $35,000
C) $15,000
D) $27,600
Unlock Deck
Unlock for access to all 106 flashcards in this deck.
Unlock Deck
k this deck
14
A company currently has no items in inventory. The demand for the next four months is 200, 400, 250, and 350 units. Assuming a level production rate of 250 units per month, determine the months in which backorders or stockouts will materialize.
A) Only in month 1
B) In months 2 and 4
C) In months 2, 3, and 4
D) In months 2 and 3
A) Only in month 1
B) In months 2 and 4
C) In months 2, 3, and 4
D) In months 2 and 3
Unlock Deck
Unlock for access to all 106 flashcards in this deck.
Unlock Deck
k this deck
15
The Academic Company mixes and bottles a high-energy beverage in various container types and sizes for college students. The aggregate forecast for the next four quarters (1 year) in thousands of gallons is as follows:
Table 1
Academic's management makes the following assumptions:
Each employee works 550 standard hours of regular time each quarter.
On average, it takes 27 hours to produce and package 1 unit (1,000 gallons).
Regular-time labor costs $6.00/hour; overtime labor costs $9.00/hour.
Inventory-holding cost is approximately $4.50/unit (1,000 gallons) per quarter based upon the ending inventory per quarter.
Because of extremely hot weather, there is no beginning inventory available to start Quarter 1.
Management wants a constant work force (no hiring or firing).
Managers have also decided to always round up the number of employees needed to the next whole integer, i.e., 37.2 yields 38 employees.
______________________________________________________________________________
-Using the data in Table 1, if management decides on a chase strategy, with production in the last quarter of 600 units and a rate change cost of $3.00/1000 gallons, determine the yearly cost of rate change (hiring and firing).
A) $2,550
B) $1,950
C) $7,800
D) $3,900
Table 1
Academic's management makes the following assumptions:
Each employee works 550 standard hours of regular time each quarter.
On average, it takes 27 hours to produce and package 1 unit (1,000 gallons).
Regular-time labor costs $6.00/hour; overtime labor costs $9.00/hour.
Inventory-holding cost is approximately $4.50/unit (1,000 gallons) per quarter based upon the ending inventory per quarter.
Because of extremely hot weather, there is no beginning inventory available to start Quarter 1.
Management wants a constant work force (no hiring or firing).
Managers have also decided to always round up the number of employees needed to the next whole integer, i.e., 37.2 yields 38 employees.
______________________________________________________________________________
-Using the data in Table 1, if management decides on a chase strategy, with production in the last quarter of 600 units and a rate change cost of $3.00/1000 gallons, determine the yearly cost of rate change (hiring and firing).
A) $2,550
B) $1,950
C) $7,800
D) $3,900
Unlock Deck
Unlock for access to all 106 flashcards in this deck.
Unlock Deck
k this deck
16
The Academic Company mixes and bottles a high-energy beverage in various container types and sizes for college students. The aggregate forecast for the next four quarters (1 year) in thousands of gallons is as follows:
Table 1
Academic's management makes the following assumptions:
Each employee works 550 standard hours of regular time each quarter.
On average, it takes 27 hours to produce and package 1 unit (1,000 gallons).
Regular-time labor costs $6.00/hour; overtime labor costs $9.00/hour.
Inventory-holding cost is approximately $4.50/unit (1,000 gallons) per quarter based upon the ending inventory per quarter.
Because of extremely hot weather, there is no beginning inventory available to start Quarter 1.
Management wants a constant work force (no hiring or firing).
Managers have also decided to always round up the number of employees needed to the next whole integer, i.e., 37.2 yields 38 employees.
______________________________________________________________________________
-Using the data in Table 1, determine the annual inventory-holding cost if Academic decides to use a level production rate of 650 units per quarter.
A) $2,925.00
B) $1,012.50
C) $2,025.00
D) $4,500.00
Table 1
Academic's management makes the following assumptions:
Each employee works 550 standard hours of regular time each quarter.
On average, it takes 27 hours to produce and package 1 unit (1,000 gallons).
Regular-time labor costs $6.00/hour; overtime labor costs $9.00/hour.
Inventory-holding cost is approximately $4.50/unit (1,000 gallons) per quarter based upon the ending inventory per quarter.
Because of extremely hot weather, there is no beginning inventory available to start Quarter 1.
Management wants a constant work force (no hiring or firing).
Managers have also decided to always round up the number of employees needed to the next whole integer, i.e., 37.2 yields 38 employees.
______________________________________________________________________________
-Using the data in Table 1, determine the annual inventory-holding cost if Academic decides to use a level production rate of 650 units per quarter.
A) $2,925.00
B) $1,012.50
C) $2,025.00
D) $4,500.00
Unlock Deck
Unlock for access to all 106 flashcards in this deck.
Unlock Deck
k this deck
17
The bill of material (BOM) for Products A and B are shown below followed by a table of inventory data (called Exhibit 1). The master production scheduling (MPS) for A calls for 150 units of A to be completed in Week 4 and another 225 units to be completed in Week 5. End item A has a two-week lead time. The MPS calls for 400 units of B to be completed in Week 6. End item B has a one-week lead time.
Exhibit 1
____________________________________________________________________
-Using the data in Exhibit 1, determine the timing and amount of the first planned order receipt for Item C.
A) Week 3; 800 units
B) Week 3; 645 units
C) Week 3; 1,600 units
D) Week 2; 800 units
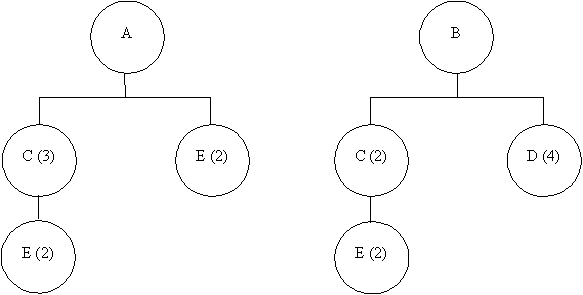
____________________________________________________________________
-Using the data in Exhibit 1, determine the timing and amount of the first planned order receipt for Item C.
A) Week 3; 800 units
B) Week 3; 645 units
C) Week 3; 1,600 units
D) Week 2; 800 units
Unlock Deck
Unlock for access to all 106 flashcards in this deck.
Unlock Deck
k this deck
18
The bill of material (BOM) for Products A and B are shown below followed by a table of inventory data (called Exhibit 1). The master production scheduling (MPS) for A calls for 150 units of A to be completed in Week 4 and another 225 units to be completed in Week 5. End item A has a two-week lead time. The MPS calls for 400 units of B to be completed in Week 6. End item B has a one-week lead time.
Exhibit 1
____________________________________________________________________
-Using the data given in Exhibit 1, determine the gross requirements for Item E in Week 2.
A) 450
B) 300
C) 1,600
D) 1,900
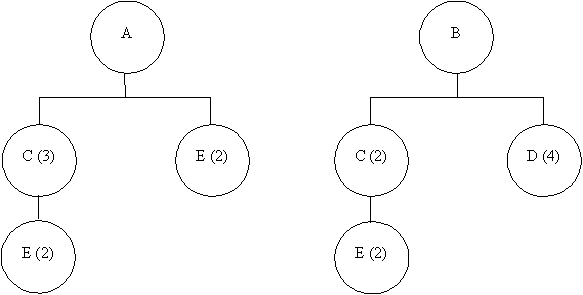
____________________________________________________________________
-Using the data given in Exhibit 1, determine the gross requirements for Item E in Week 2.
A) 450
B) 300
C) 1,600
D) 1,900
Unlock Deck
Unlock for access to all 106 flashcards in this deck.
Unlock Deck
k this deck
19
If A has a gross requirement to build 200 units and an on-hand inventory for A of 60, determine the net requirement for D if its current on-hand inventory balance for D is 200 (all other components have no (zero) current inventory).
A)Less than or equal to 1,000 units
B)Greater than 1,000 but less than or equal to 1,500 units
C)Greater than 1,500 but less than or equal to 2,000 units
D)Greater than 2,000 but less than or equal to 2,500 units
A)Less than or equal to 1,000 units
B)Greater than 1,000 but less than or equal to 1,500 units
C)Greater than 1,500 but less than or equal to 2,000 units
D)Greater than 2,000 but less than or equal to 2,500 units
Unlock Deck
Unlock for access to all 106 flashcards in this deck.
Unlock Deck
k this deck
20
Which of the following is least likely to be found in service organizations?
A) Intermediate levels in aggregate planning
B) Bills of labor (BOL)
C) Bills of resources and forecasting
D) Dependent demand
A) Intermediate levels in aggregate planning
B) Bills of labor (BOL)
C) Bills of resources and forecasting
D) Dependent demand
Unlock Deck
Unlock for access to all 106 flashcards in this deck.
Unlock Deck
k this deck
21
Which of the following is an aggregate planning decision option?
A) Staff schedules
B) Disaggregation
C) Shop floor control
D) Market forecasts
A) Staff schedules
B) Disaggregation
C) Shop floor control
D) Market forecasts
Unlock Deck
Unlock for access to all 106 flashcards in this deck.
Unlock Deck
k this deck
22
_____ are the total demand for an item derived from all of its parents.
A) Explosions
B) Gross requirements
C) Scheduled receipts
D) Planned order receipts
A) Explosions
B) Gross requirements
C) Scheduled receipts
D) Planned order receipts
Unlock Deck
Unlock for access to all 106 flashcards in this deck.
Unlock Deck
k this deck
23
All of the following statements are true regarding dependent demand EXCEPT:
A) it is one of the underlying concepts of materials requirements planning (MRP).
B) its concept can be understood by examining the bill of materials.
C) it can be calculated only by forecasting.
D) it is directly related to the demands of other stock-keeping units (SKUs).
A) it is one of the underlying concepts of materials requirements planning (MRP).
B) its concept can be understood by examining the bill of materials.
C) it can be calculated only by forecasting.
D) it is directly related to the demands of other stock-keeping units (SKUs).
Unlock Deck
Unlock for access to all 106 flashcards in this deck.
Unlock Deck
k this deck
24
The primary output of a materials requirements planning (MRP) system is a time-phased report that gives all of the following EXCEPT:
A) the facilities managers a detailed schedule for acquiring additional factory space.
B) the accounting and financial functions production information that drives cash flow, budgets, and financial needs.
C) the production managers a detailed schedule for manufacturing the product and controlling manufacturing inventories.
D) the purchasing department a schedule for obtaining raw material and purchased items.
A) the facilities managers a detailed schedule for acquiring additional factory space.
B) the accounting and financial functions production information that drives cash flow, budgets, and financial needs.
C) the production managers a detailed schedule for manufacturing the product and controlling manufacturing inventories.
D) the purchasing department a schedule for obtaining raw material and purchased items.
Unlock Deck
Unlock for access to all 106 flashcards in this deck.
Unlock Deck
k this deck
25
Which aggregate planning strategy generally would result in the least amount of inventory?
A) Level production strategy
B) Chase demand strategy
C) Fixed-order-quantity rule
D) Lot-for-lot (LFL) rule
A) Level production strategy
B) Chase demand strategy
C) Fixed-order-quantity rule
D) Lot-for-lot (LFL) rule
Unlock Deck
Unlock for access to all 106 flashcards in this deck.
Unlock Deck
k this deck
26
Which lot sizing rule bases the order quantity on a standard-size container or pallet load?
A) Lot-for-lot (LFL) rule
B) Fixed-order quantity (FOQ) rule
C) Periodic-order quantity (POQ) rule
D) Gross requirements (GR) rule
A) Lot-for-lot (LFL) rule
B) Fixed-order quantity (FOQ) rule
C) Periodic-order quantity (POQ) rule
D) Gross requirements (GR) rule
Unlock Deck
Unlock for access to all 106 flashcards in this deck.
Unlock Deck
k this deck
27
If forecast demand exceeds the total factory or supply capacity, managers might simply decide not to meet forecast demand. This decision would most likely be made at which planning level?
A) Aggregate planning-Level 1
B) Disaggregation-Level 2
C) Execution-Level 3
D) Shop floor controlling-Level 4
A) Aggregate planning-Level 1
B) Disaggregation-Level 2
C) Execution-Level 3
D) Shop floor controlling-Level 4
Unlock Deck
Unlock for access to all 106 flashcards in this deck.
Unlock Deck
k this deck
28
Which aggregate planning strategy sets production rate equal to the demand?
A) Level production strategy
B) Chase demand strategy
C) Lot-for-lot (LFL) rule
D) Periodic-order-quantity (POQ) rule
A) Level production strategy
B) Chase demand strategy
C) Lot-for-lot (LFL) rule
D) Periodic-order-quantity (POQ) rule
Unlock Deck
Unlock for access to all 106 flashcards in this deck.
Unlock Deck
k this deck
29
An inventory item can be:
A) only a parent.
B) only a component.
C) both a parent and a component.
D) either a parent or a component, but not both.
A) only a parent.
B) only a component.
C) both a parent and a component.
D) either a parent or a component, but not both.
Unlock Deck
Unlock for access to all 106 flashcards in this deck.
Unlock Deck
k this deck
30
Time buckets:
A) are the same as planning horizons.
B) can be set at a day for longer-term planning.
C) are usually one week in length.
D) are computed based on gross requirements.
A) are the same as planning horizons.
B) can be set at a day for longer-term planning.
C) are usually one week in length.
D) are computed based on gross requirements.
Unlock Deck
Unlock for access to all 106 flashcards in this deck.
Unlock Deck
k this deck
31
Setting order sizes and schedules for individual subassemblies and resources by week or day fits best with which level of the generic framework for resource planning?
A) Aggregate planning-Level 1
B) Disaggregation-Level 2
C) Execution-Level 3
D) Shop floor controlling-Level 4
A) Aggregate planning-Level 1
B) Disaggregation-Level 2
C) Execution-Level 3
D) Shop floor controlling-Level 4
Unlock Deck
Unlock for access to all 106 flashcards in this deck.
Unlock Deck
k this deck
32
Which of the following is NOT an aggregate planning decision option?
A) Promotion and advertising
B) Subcontracting
C) Layoffs
D) Staff schedules
A) Promotion and advertising
B) Subcontracting
C) Layoffs
D) Staff schedules
Unlock Deck
Unlock for access to all 106 flashcards in this deck.
Unlock Deck
k this deck
33
Lot-for-lot (LFL):
A) minimizes purchase or setup costs.
B) maximizes the amount of inventory that need to be carried.
C) ignores the cost associated with purchase orders.
D) masks the true nature of dependent demand.
A) minimizes purchase or setup costs.
B) maximizes the amount of inventory that need to be carried.
C) ignores the cost associated with purchase orders.
D) masks the true nature of dependent demand.
Unlock Deck
Unlock for access to all 106 flashcards in this deck.
Unlock Deck
k this deck
34
A _____ is a statement of how many finished items are to be produced and when they are to be produced.
A) capacity requirements plan (CRP)
B) master production schedule (MPS)
C) material requirements plan (MRP)
D) shop floor control
A) capacity requirements plan (CRP)
B) master production schedule (MPS)
C) material requirements plan (MRP)
D) shop floor control
Unlock Deck
Unlock for access to all 106 flashcards in this deck.
Unlock Deck
k this deck
35
The words "product family," "budget allocation," and "long-term" fit best with which level of the generic framework for resource planning?
A) Aggregate planning-Level 1
B) Disaggregation-Level 2
C) Execution-Level 3
D) Shop floor controlling-Level 4
A) Aggregate planning-Level 1
B) Disaggregation-Level 2
C) Execution-Level 3
D) Shop floor controlling-Level 4
Unlock Deck
Unlock for access to all 106 flashcards in this deck.
Unlock Deck
k this deck
36
In the disaggregation framework, the direct inputs to material requirements planning (MRP) include all of the following EXCEPT:
A) master production schedule (MPS).
B) transaction files.
C) bills of materials (BOM).
D) capacity requirements plan (CRP).
A) master production schedule (MPS).
B) transaction files.
C) bills of materials (BOM).
D) capacity requirements plan (CRP).
Unlock Deck
Unlock for access to all 106 flashcards in this deck.
Unlock Deck
k this deck
37
Which of the following is NOT TRUE regarding aggregate planning?
A) Large number of alternatives can be developed.
B) Good solutions using spreadsheets can be found by trial-and-error method.
C) Seasonal fluctuations in demand can be accommodated.
D) Costs are sunk and irrelevant.
A) Large number of alternatives can be developed.
B) Good solutions using spreadsheets can be found by trial-and-error method.
C) Seasonal fluctuations in demand can be accommodated.
D) Costs are sunk and irrelevant.
Unlock Deck
Unlock for access to all 106 flashcards in this deck.
Unlock Deck
k this deck
38
Which lot sizing rule is best when inventory carrying costs are high and setup/order costs are low?
A) Lot-for-lot (LFL)
B) Fixed-order quantity (FOQ)
C) Periodic-order quantity (POQ)
D) Gross requirements (GR)
A) Lot-for-lot (LFL)
B) Fixed-order quantity (FOQ)
C) Periodic-order quantity (POQ)
D) Gross requirements (GR)
Unlock Deck
Unlock for access to all 106 flashcards in this deck.
Unlock Deck
k this deck
39
Promotion of weekly discount airfares by an airline would be an example of _____.
A) demand management
B) production-rate changes
C) inventory changes
D) facility, equipment, and transportation changes
A) demand management
B) production-rate changes
C) inventory changes
D) facility, equipment, and transportation changes
Unlock Deck
Unlock for access to all 106 flashcards in this deck.
Unlock Deck
k this deck
40
Assigning people to tasks, setting priorities for jobs, and scheduling equipment fits best with which level of the generic framework for resource planning?
A) Aggregate planning-Level 1
B) Disaggregation-Level 2
C) Execution-Level 3
D) Market forecasting-Level 4
A) Aggregate planning-Level 1
B) Disaggregation-Level 2
C) Execution-Level 3
D) Market forecasting-Level 4
Unlock Deck
Unlock for access to all 106 flashcards in this deck.
Unlock Deck
k this deck
41
Short-term changes in facilities and equipment are seldom used in traditional aggregate planning methods because of the capital costs involved.
Unlock Deck
Unlock for access to all 106 flashcards in this deck.
Unlock Deck
k this deck
42
A chase demand aggregate planning strategy may result in substantial overtime, undertime, and rate-change costs.
Unlock Deck
Unlock for access to all 106 flashcards in this deck.
Unlock Deck
k this deck
43
Service firms frequently take their aggregate plans and disaggregate them down to the execution level as detailed frontline staff and resource schedules, job sequences, and service-encounter execution.
Unlock Deck
Unlock for access to all 106 flashcards in this deck.
Unlock Deck
k this deck
44
If a work center load report indicates insufficient capacity, options for correcting the problem include all of the following EXCEPT:
A) revising the bill of materials.
B) changing the master product schedule.
C) subcontracting.
D) transferring personnel between work centers.
A) revising the bill of materials.
B) changing the master product schedule.
C) subcontracting.
D) transferring personnel between work centers.
Unlock Deck
Unlock for access to all 106 flashcards in this deck.
Unlock Deck
k this deck
45
The purpose of the master schedule is to translate the aggregate plan into a separate plan for individual finished goods.
Unlock Deck
Unlock for access to all 106 flashcards in this deck.
Unlock Deck
k this deck
46
Aggregate planning and disaggregation methods in goods-producing industries involve fewer levels of planning than service-providing organizations, because service organizations deal with more than just materials.
Unlock Deck
Unlock for access to all 106 flashcards in this deck.
Unlock Deck
k this deck
47
Increasing the output rate without changing existing resources is an example of demand management.
Unlock Deck
Unlock for access to all 106 flashcards in this deck.
Unlock Deck
k this deck
48
A(n) _____ is a process of determining the amount of labor and machines required to accomplish the tasks of production on a more detailed level.
A) action schedule (AS)
B) master production schedule (MPS)
C) material requirements plan (MRP)
D) capacity requirements plan (CRP)
A) action schedule (AS)
B) master production schedule (MPS)
C) material requirements plan (MRP)
D) capacity requirements plan (CRP)
Unlock Deck
Unlock for access to all 106 flashcards in this deck.
Unlock Deck
k this deck
49
Good solutions to aggregate planning situations using spreadsheets can be found by trial-and-error approaches.
Unlock Deck
Unlock for access to all 106 flashcards in this deck.
Unlock Deck
k this deck
50
Capacity requirements are computed by multiplying the number of units scheduled for production at a work center by:
A) the setup time and then subtracting the unit resource requirements.
B) the setup time and then adding the unit resource requirements.
C) the unit resource requirements and then adding in the setup time.
D) the unit resource requirements and then subtracting the setup time.
A) the setup time and then subtracting the unit resource requirements.
B) the setup time and then adding the unit resource requirements.
C) the unit resource requirements and then adding in the setup time.
D) the unit resource requirements and then subtracting the setup time.
Unlock Deck
Unlock for access to all 106 flashcards in this deck.
Unlock Deck
k this deck
51
A level production strategy maintains constant inventory levels over the planning horizon.
Unlock Deck
Unlock for access to all 106 flashcards in this deck.
Unlock Deck
k this deck
52
Resources include materials, equipment, facilities, information, technical knowledge and skills, and people.
Unlock Deck
Unlock for access to all 106 flashcards in this deck.
Unlock Deck
k this deck
53
When demand is seasonal, inventory cannot be used to stabilize production and employment rates.
Unlock Deck
Unlock for access to all 106 flashcards in this deck.
Unlock Deck
k this deck
54
An example of aggregation would be an ice cream manufacturer developing targets to produce a number of gallons of each flavor along with the purchasing requirements for specific ingredients for a one-week period.
Unlock Deck
Unlock for access to all 106 flashcards in this deck.
Unlock Deck
k this deck
55
The lower the skill requirements of the workforce, the more feasible it is to change workforce levels as an aggregate planning option.
Unlock Deck
Unlock for access to all 106 flashcards in this deck.
Unlock Deck
k this deck
56
Level 3 planning, i.e. detailed planning and execution, represents aggregate planning at higher management levels of an organization.
Unlock Deck
Unlock for access to all 106 flashcards in this deck.
Unlock Deck
k this deck
57
Which lot sizing rule uses the economic order quantity (EOQ) calculation?
A) Both lot-for-lot (LFL) and periodic-order quantity (POQ) rules
B) Only fixed-order quantity (FOQ) rule
C) Only periodic-order quantity (POQ) rule
D) Both fixed-order quantity (FOQ) and periodic-order quantity (POQ) rules
A) Both lot-for-lot (LFL) and periodic-order quantity (POQ) rules
B) Only fixed-order quantity (FOQ) rule
C) Only periodic-order quantity (POQ) rule
D) Both fixed-order quantity (FOQ) and periodic-order quantity (POQ) rules
Unlock Deck
Unlock for access to all 106 flashcards in this deck.
Unlock Deck
k this deck
58
Which is the most comprehensive solution for a firm if a load report shows not enough capacity is available?
A) Revise the bill of materials (BOM) and increase capacity.
B) Change the action bucket.
C) Change the master production schedule (MPS) and add capacity.
D) Rerun materials requirements planning (MRP).
A) Revise the bill of materials (BOM) and increase capacity.
B) Change the action bucket.
C) Change the master production schedule (MPS) and add capacity.
D) Rerun materials requirements planning (MRP).
Unlock Deck
Unlock for access to all 106 flashcards in this deck.
Unlock Deck
k this deck
59
Resource management deals primarily with managing inventories in a value chain.
Unlock Deck
Unlock for access to all 106 flashcards in this deck.
Unlock Deck
k this deck
60
The master production schedule (MPS) is developed in the same manner, no matter the type of industry (make-to-stock vs. make-to-order) and the number of items produced (few or many).
Unlock Deck
Unlock for access to all 106 flashcards in this deck.
Unlock Deck
k this deck
61
Define material requirements planning (MRP) and how it can benefit an organization.
Unlock Deck
Unlock for access to all 106 flashcards in this deck.
Unlock Deck
k this deck
62
Describe the options that managers have for developing aggregate plans to respond to fluctuating demand.
Unlock Deck
Unlock for access to all 106 flashcards in this deck.
Unlock Deck
k this deck
63
A bill of materials (BOM) characterizes the structure of dependent demand among all items that comprise a finished good.
Unlock Deck
Unlock for access to all 106 flashcards in this deck.
Unlock Deck
k this deck
64
A service facility like a hospital cannot use material requirements planning concepts and methods such as bills of labor (BOL) and the concept of dependent demand.
Unlock Deck
Unlock for access to all 106 flashcards in this deck.
Unlock Deck
k this deck
65
Explain how a bill of materials (BOM), bill of labor (BOL), and bill of resources (BOR) relate.
Unlock Deck
Unlock for access to all 106 flashcards in this deck.
Unlock Deck
k this deck
66
Lot sizing is the process of translating aggregate plans into short-term operational plans that provide the basis for weekly and daily schedules.
Unlock Deck
Unlock for access to all 106 flashcards in this deck.
Unlock Deck
k this deck
67
Which one of the following statements is TRUE regarding the Greyhound Frequent Flyer Call Center case?
A) In the four step analysis procedure described in the case, Step 1 uses equation "Utilization = Demand Rate/[(Service Rate)*(Number of Servers)]."
B) The "travel advice" category of calls was the lowest priority relative to the other three categories of calls.
C) True demand in the case included the number of calls rerouted to different customer service representative (CSR) specialists.
D) The analysis of the case data revealed no scheduling problem with the current customer service representative (CSR) staff schedule.
A) In the four step analysis procedure described in the case, Step 1 uses equation "Utilization = Demand Rate/[(Service Rate)*(Number of Servers)]."
B) The "travel advice" category of calls was the lowest priority relative to the other three categories of calls.
C) True demand in the case included the number of calls rerouted to different customer service representative (CSR) specialists.
D) The analysis of the case data revealed no scheduling problem with the current customer service representative (CSR) staff schedule.
Unlock Deck
Unlock for access to all 106 flashcards in this deck.
Unlock Deck
k this deck
68
In materials requirements planning (MRP), it is essential that all dependent demand requirements be ordered at the beginning of the planning period.
Unlock Deck
Unlock for access to all 106 flashcards in this deck.
Unlock Deck
k this deck
69
Define resource management and list its key objectives.
Unlock Deck
Unlock for access to all 106 flashcards in this deck.
Unlock Deck
k this deck
70
After a master production schedule (MPS) is created for finished goods, the demand for all materials and components necessary can be calculated, not forecasted.
Unlock Deck
Unlock for access to all 106 flashcards in this deck.
Unlock Deck
k this deck
71
A scheduled receipt for an outside vendor is called a purchase order.
Unlock Deck
Unlock for access to all 106 flashcards in this deck.
Unlock Deck
k this deck
72
Explain the three levels of resource planning.
Unlock Deck
Unlock for access to all 106 flashcards in this deck.
Unlock Deck
k this deck
73
In a bill of materials (BOM), each component is comprised of one or more parent items.
Unlock Deck
Unlock for access to all 106 flashcards in this deck.
Unlock Deck
k this deck
74
Differentiate between a level production strategy and a chase demand strategy.
Unlock Deck
Unlock for access to all 106 flashcards in this deck.
Unlock Deck
k this deck
75
Define a master production schedule (MPS) and explain how it differs from a final assembly schedule.
Unlock Deck
Unlock for access to all 106 flashcards in this deck.
Unlock Deck
k this deck
76
End items in a master production schedule (MPS) or final assembly schedule must be forecast.
Unlock Deck
Unlock for access to all 106 flashcards in this deck.
Unlock Deck
k this deck
77
A periodic-order quantity (POQ) for a one-week time period is equivalent to lot-for-lot (LFL) sizing.
Unlock Deck
Unlock for access to all 106 flashcards in this deck.
Unlock Deck
k this deck
78
Dependent demand does not occur in the service business.
Unlock Deck
Unlock for access to all 106 flashcards in this deck.
Unlock Deck
k this deck
79
Lot sizing rules on a parent item do not affect the gross requirements of all lower level component items.
Unlock Deck
Unlock for access to all 106 flashcards in this deck.
Unlock Deck
k this deck
80
Work center load reports are used in capacity requirements planning (CRP).
Unlock Deck
Unlock for access to all 106 flashcards in this deck.
Unlock Deck
k this deck