Exam 18: Activity-Based Costing and Other Cost Management Tools
Exam 1: Accounting and the Business Environment156 Questions
Exam 2: Recording Business Transactions156 Questions
Exam 3: The Adjusting Process160 Questions
Exam 4: Completing the Accounting Cycle165 Questions
Exam 5: Merchandising Operations168 Questions
Exam 6: Merchandising Inventory155 Questions
Exam 7: Internal Control and Cash161 Questions
Exam 8: Receivables166 Questions
Exam 9: Plant Assets and Intangibles170 Questions
Exam 10: Current Liabilities and Payroll159 Questions
Exam 11: Long-Term Liabilities, Bonds Payable, and Classification of Liabilities on the Balance Sheet161 Questions
Exam 12: Corporations: Paid-In Capital and the Balance Sheet167 Questions
Exam 13: Corporations: Effects on Retained Earnings and the Income Statement164 Questions
Exam 14: The Statement of Cash Flows162 Questions
Exam 15: Financial Statement Analysis163 Questions
Exam 16: Introduction to Management Accounting163 Questions
Exam 17: Job Order and Process Costing172 Questions
Exam 18: Activity-Based Costing and Other Cost Management Tools162 Questions
Exam 19: Cost-Volume-Profit Analysis165 Questions
Exam 20: Short-Term Business Decisions163 Questions
Exam 21: Capital Investment Decisions and the Time Value of Money153 Questions
Exam 22: The Master Budget and Responsibility Accounting157 Questions
Exam 23: Flexible Budgets and Standard Costs166 Questions
Exam 24: Performance Evaluation and the Balanced Scorecard166 Questions
Select questions type
Target cost is the price that customers are willing to pay and target price is the desired cost to produce the product.
Free
(True/False)
4.7/5
(39)
Correct Answer:
False
Clark Manufacturing makes blank CDs; it is a very competitive market and the company follows a target pricing strategy. Currently the market price for a unit of product (one unit equals a package of 100 CDs)is $18.00. Clark's production costs are shown below:
The company's objective is to earn 5% profit on the sales price of the product. Clark carried out a value engineering study and decided that they could make the processing activity more efficient and save costs. In order to achieve their profit objective for this product, they need to reduce the indirect cost per unit from $6.42 down to what amount?
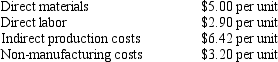

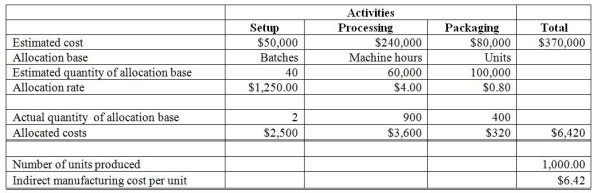
Free
(Multiple Choice)
4.7/5
(38)
Correct Answer:
B
Just-in-time production systems have a great deal of flexibility, and can easily tolerate small interruptions of supplies, and occasional defective materials.
Free
(True/False)
4.8/5
(33)
Correct Answer:
False
Percival Company wishes to sell wooden beams to home builders. The current market price of the beams is $950, and Percival knows it must accept the market price. The company wishes to make a profit equal to 16% of the price. Using target costing, the company will have to design the production process to meet this requirement. What is the desired target cost per beam?
(Multiple Choice)
4.8/5
(34)
Pitt Jones Company had the following activities, allocated costs, and allocation bases:
The above activities are carried out at two of their regional offices.
How much of the account inquiry cost will be assigned to the Midwest Office?


(Multiple Choice)
4.8/5
(43)
Pitt Jones Company had the following activities, allocated costs, and allocation bases:
The above activities are carried out at two of their regional offices.
What is the cost per unit for the correspondence activity?


(Multiple Choice)
4.8/5
(36)
All of the following accounts would be used in a backflush costing system EXCEPT:
(Multiple Choice)
4.9/5
(33)
Activity-based management can be used to make business decisions about cost cutting.
(True/False)
4.9/5
(39)
Clark Manufacturing makes blank CDs; it is a very competitive market and the company follows a target pricing strategy. Currently the market price for a unit of product (one unit equals a package of 100 CDs)is $18.00. Clark's production costs are shown below:
The company's objective is to earn 5% profit on the sales price of the product. Clark carried out a value engineering study and decided that they could make the processing activity more efficient and save costs. If they reduce the total processing activity cost down to $210,000, what will their profit percentage be? (Please round to the nearest tenth of a percent.)


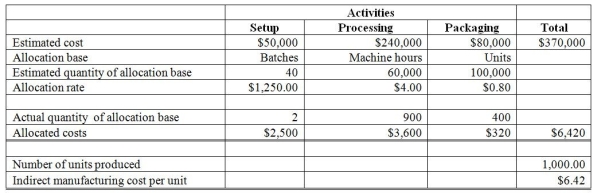
(Multiple Choice)
4.8/5
(38)
A-1 Sports Vehicles Manufacturing produces a specialty racing bicycle. There is stiff foreign competition, and the company is forced to pursue target pricing. The competitive market price of the bicycle is $2,000. Currently the manufacturing cost for this product at A-1 is $1,550 and the associated non-manufacturing costs are $270. A-1's owners insist on achieving a profit of 12% of sales price. What amount is the target cost? (Please round all amounts to the nearest whole dollar.)
(Multiple Choice)
4.8/5
(38)
Archetype Fabrication makes pre-stressed concrete forms for the building industry. They use just-in-time production and accounting methodology. At the beginning of January, selected account balances are shown in the T-accounts below.
During January, the following 5 transactions take place:
Use the T-accounts shown above to record the transactions, and then answer the following question:
How much was the cost of goods sold?
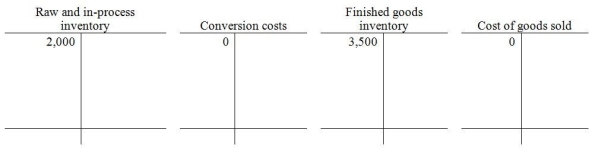

(Multiple Choice)
4.9/5
(41)
Leon Production produces steel rivets for the shipbuilding business. Leon uses the target pricing approach. The company's objective is to achieve gross profit equal to 25% of selling price. Other data are shown below:
What must the company do to achieve their profit goal? (Please round all amounts to the nearest cent.)

(Multiple Choice)
5.0/5
(33)
The cost of reengineering the production process to reduce defect rate is an example of which of the following?
(Multiple Choice)
4.7/5
(27)
Equival Company wishes to sell truck axles to car manufacturers. The current market price of the axles is $400, and Equival knows it must accept the market price. The company wishes to make a profit equal to 20% of the price. Using target costing, Equival will have to design the production process to meet this requirement. What is the desired target cost per axle?
(Multiple Choice)
4.8/5
(33)
In a just-in-time costing system, the entry to record the standard cost of finished goods completed would include which of the following?
(Multiple Choice)
4.8/5
(27)
The cost of product liability claims comes under which category of costs?
(Multiple Choice)
4.7/5
(27)
Formosa Steel Products makes steel building materials for export, and uses an activity-based costing system to account for the indirect manufacturing costs of its various products. Indirect costs for the whole factory are broken down into three activities-casting, materials handling, and milling. The cost driver for casting is machine hours; the cost driver for material handling is kilograms, and the cost driver for milling is direct labor hours. Activity costs and volumes for the year were estimated as follows:
One product is steel reinforcement rods, sold by the metric ton. Engineering reports show that one metric ton of steel reinforcement rods requires $100 of direct materials cost plus $50 of direct labor cost. Producing one metric ton of steel rods also requires 24 machine hours for casting, weighs 1,000 kilograms, and requires 15 direct labor hours.
What is the activity rate for the material handling activity?

(Multiple Choice)
4.8/5
(26)
Pitt Jones Company had the following activities, allocated costs, and allocation bases:
The above activities are carried out at two of their regional offices.
What is the cost per unit for the account verification activity?


(Multiple Choice)
4.8/5
(46)
AAA Metal Bearings produces two sizes of metal bearings (sold by the crate)-standard and heavy. The standard bearings require $200 of direct materials per unit (per crate)and the heavy bearings require $245 of direct materials per unit. The operation is mechanized and there is no direct labor. Previously AAA used a single plantwide allocation rate for manufacturing overhead, which was $1.55 per machine hour. Based on the single rate, gross profit data were as follows:
Although the data showed that the heavy bearings were more profitable than the standard bearings, the plant manager knew that the heavy bearings required much more processing in the metal fabrication phase than the standard bearings, and that this factor was not adequately reflected in the single allocation rate. He suspected that it was distorting the profit data. He suggested adopting an activity-based costing approach.
Working together, the engineers and accountants identified the following three manufacturing activities, and broke down the annual overhead costs as shown:
Engineers believed that metal fabrication costs should be allocated by weight, and estimated that the plant processed 12,000 kilos of metal per year. Machine processing costs were correlated to machine hours, and the engineers estimated a total of 380,000 machine hours for the year. Packaging costs were the same for both types of products, and so they could be allocated simply by the number of units produced. The production plan provided for 4,000 units of standard and 1,000 units of heavy bearings to be produced during the year. Additional data on a per unit basis are as follows:
Using the data above, please calculate activity rates. Then, following the ABC methodology, calculate the production cost and gross profit for both product types, using the format below:

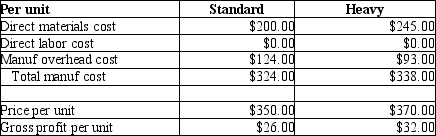



(Essay)
5.0/5
(33)
Which of the following categories includes costs incurred in detecting poor quality goods or services?
(Multiple Choice)
4.8/5
(25)
Showing 1 - 20 of 162
Filters
- Essay(0)
- Multiple Choice(0)
- Short Answer(0)
- True False(0)
- Matching(0)