Exam 6: MRP production system
Fill out the following MRP record.The lot size is 360 units and the units on hand are 500 units.The lead time between order placement and receipt is 2 periods.Now it is period 2 and the forecast for the period 2 and 3's demand has changed.For period 2, the demand is 190 while it is 125 for period 3.Provide a MRP record starting on period 2.
Lot size: 360 1 Period 1 2 3 4 5 6 7 8 GR 160 290 125 80 110 250 350 80 SR POH NR POR
Explain why lumpy demands is created by a reorder point system and less with a MRP system
A reorder point system is designed to trigger a new order when the inventory level drops to a certain point, known as the reorder point. This means that orders are only placed when the inventory level hits this specific point, which can lead to lumpy demand. For example, if the reorder point is set too high, then large and infrequent orders will be placed, leading to lumpy demand as the inventory is quickly depleted and then replenished in large quantities.
On the other hand, a Material Requirements Planning (MRP) system takes into account the demand for a product and plans the production and procurement of materials accordingly. This system uses a master production schedule and a bill of materials to calculate the exact materials and components needed at specific times. This can help to smooth out demand by ensuring that the right amount of materials are ordered at the right time, reducing the likelihood of lumpy demand.
In summary, a reorder point system can lead to lumpy demand because it only triggers orders at specific inventory levels, while an MRP system is more proactive in planning for demand and can help to mitigate lumpy demand by ensuring the right amount of materials are ordered at the right time.
List at least 2 inputs for the MRP process
The Material Requirements Planning (MRP) process is a system used for managing manufacturing processes. It helps in planning and controlling inventory levels and production schedules to ensure that materials are available for production and products are available for delivery to customers. The MRP process relies on several key inputs to function effectively. Here are at least two essential inputs for the MRP process:
1. **Bill of Materials (BOM):** The BOM is a comprehensive list of raw materials, components, and assemblies needed to manufacture a product. It includes the quantity of each item and the sequence in which the product is assembled or produced. The BOM is critical for the MRP process because it defines exactly what materials are required, in what quantities, and at what stage of the manufacturing process.
2. **Inventory Records:** Accurate and up-to-date inventory records are crucial for the MRP process. These records include information on the quantities of raw materials, work-in-progress (WIP), and finished goods that are currently in stock. They also track the status of materials (e.g., on order, in transit, available for use). The MRP system uses this information to determine when additional materials need to be ordered and in what quantities, based on the production schedule.
These two inputs are foundational for the MRP process to calculate material requirements, generate purchase orders, and create work orders to meet production demands while minimizing excess inventory and costs.
Product A uses 3 units of component B.The following is the MRP record for product A.Fill out the MRP record for component B.There are currently 100 product As and 700 component Bs on hand.For product A, the lot size is a multiple of 60 units while component B uses the lot for lot (LFL)technique.
Product A: 1 unit with a lead time of 1 period.
Component B: 3 unit with a lead time of 2 period.
Lot size: 60 Period 1 2 3 4 5 6 7 8 GR 60 90 125 280 150 150 150 30 SR POH 100 40 10 5 25 55 25 55 25 NR -40 50 115 275 125 95 125 -25 POR 60 120 300 180 120 180
Fill out the following MRP record using lot for lot (LFL)lot sizing technique.What is the total cost using end inventory value? The holding cost is $3 per unit per period and the ordering cost is $500 per order.No lead time exists.
LFL Period 0 1 2 3 4 5 6 7 8 GR 60 90 125 180 150 50 450 60 SR 150 60 POH 10 NR POR
MRP is a computer-driven information system that translates end-item demand into raw materials, component parts, and subassemblies requirements.It works backward from the due date using _________, and other production information's.Which of the following information does not fit in the previous sentence?
Using the table below, calculate the holding inventory costs for all periods using end inventory values.The holding cost per period per unit is $5.
Periods 1 2 3 4 5 6 7 8 9 10 Usage 1000 120 500 800 450 1280 800 500 280 180 End Inventory 0 300 70 530 70 0 30 0 30 0
Describe how MRP II is differentiated from the MRP system in the context of manufacturing control and planning.
Using the table below, calculate the holding inventory costs for all four periods using both average inventory and end inventory values.The holding cost per period per unit is $200.The sequence of cost is (average inventory, end inventory).
Periods 1 2 3 4 Usage 100 120 50 80 End Inventory 10 30 70 30
The lot size is 60 units and the units on hand are 0 units.What is the total cost when using an average inventory value? The holding cost is $3 per unit per period and the ordering cost is $500 per order.No lead time exists.
Lot size: 60 Period 1 2 3 4 5 6 7 8 GR 80 90 125 290 125 80 45 60 SR 150 60 POH NR POR
Complete the following MRP record.The lot size is a multiple of 60 with a holing cost of $300 per unit per period.What is the period with the largest holding cost for both average and end item values? (average/end)
Lot size: 60 Period 1 2 3 4 5 6 7 8 GR 80 90 125 290 125 80 45 60 SR 150 60 PA NR POR
Using all idealized assumptions regarding uncertainty, the lot-sizing procedure performance is based on the minimizing the total cost which include _______ cost and ________ costs subject to the __________ of each period.Find the correct concepts to fit in to the previous sentence.
Find the correct concepts to fit in to the following sentence.The MPS process handles ___________ while the MRP process handles ____________.
Fill out the following MRP record using a holding cost of $2 per unit per week and the ordering cost is $90 per order.No lead time exists.What is the cost difference between using EOQ and POQ Techniques? Which one is more effective? Use the ending inventory values.
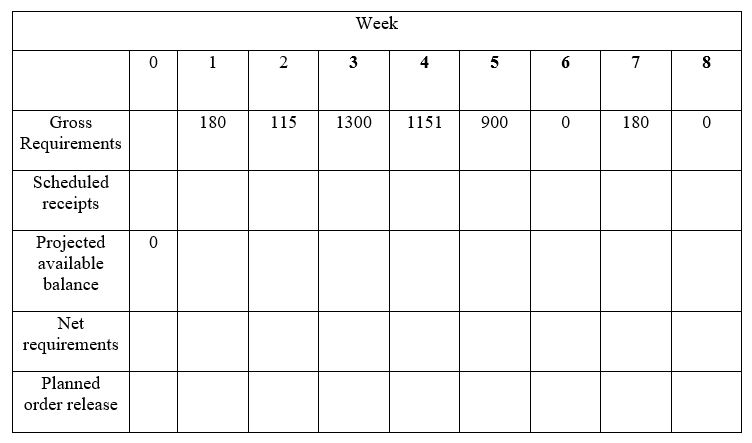
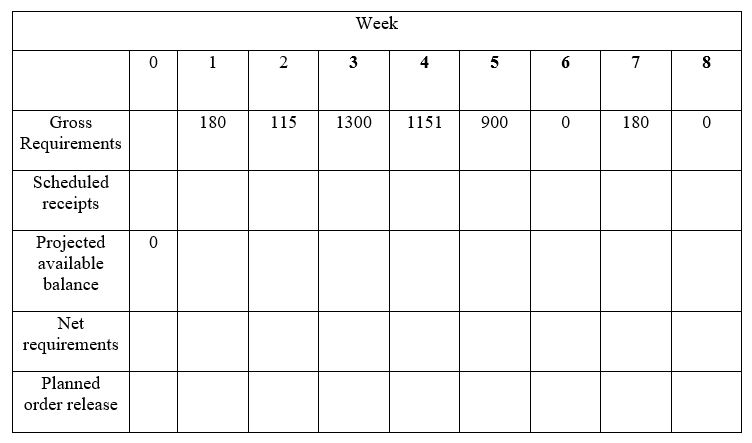
What is the difference between using average inventory values and end inventory values when it comes to calculating inventory costs?
Fill out the following MRP record and calculate the inventory holding cost using end inventory values.The lot size is a multiple of 500 units and the holding cost is $20 per unit per period.
Periods 1 2 3 4 Demands 1000 350 500 800 Projected Availability Net Requirements
Which of the following are not MRP Design Decisions?
1)time bucket size
2)delivery lead time
3)safety stock size
4)lot-sizing method
In the context of a MRP record, describe what a scheduled receipt is.
Filters
- Essay(0)
- Multiple Choice(0)
- Short Answer(0)
- True False(0)
- Matching(0)