Exam 11: Strategic Cost Management
Exam 1: Introduction to Cost Management151 Questions
Exam 2: Basic Cost Management Concepts199 Questions
Exam 3: Cost Behavior193 Questions
Exam 4: Activity-Based Costing198 Questions
Exam 5: Product and Service Costing: Job-Order System149 Questions
Exam 6: Process Costing181 Questions
Exam 7: Allocating Costs of Support Departments and Joint Products171 Questions
Exam 8: Budgeting for Planning and Control202 Questions
Exam 9: Standard Costing: a Functional-Based Control Approach125 Questions
Exam 10: Decentralization: Responsibility, Accounting, Performance Evaluation, and Transfer Pricing134 Questions
Exam 11: Strategic Cost Management148 Questions
Exam 12: Activity-Based Management146 Questions
Exam 13: The Balanced Scorecard: Strategic-Based Control124 Questions
Exam 14: Quality and Environmental Cost Management199 Questions
Exam 15: Lean Accounting and Productivity Measurement161 Questions
Exam 16: Cost-Volume-Profit Analysis128 Questions
Exam 17: Activity Resource Usage Model and Tactical Decision Making121 Questions
Exam 18: Pricing and Profitability Analysis159 Questions
Exam 19: Capital Investment125 Questions
Exam 20: Inventory Management: Economic Order Quantity, Jit, and the Theory of Constraints127 Questions
Select questions type
Figure 11-1
Ambrosia Corp. is a manufacturer of equipment used in manufacturing. It currently produces a product with 30 parts but through redesign has reduced the number of parts to 9. Then current activity capacity and demand for the 30 unit configuration and expected activity demand for the 9 part configuration are provided below:
Materials usage has a rate of $6 per part and no fixed costs. Assembly has a rate of $20 per labor hour with no fixed component. Purchasing requires clerks that can process 5,000 purchase orders. Each clerk earns $40,000 per year. There is also a $1 per order processing cost.
-Refer to Figure 11-1. What is the cost savings from purchasing parts?
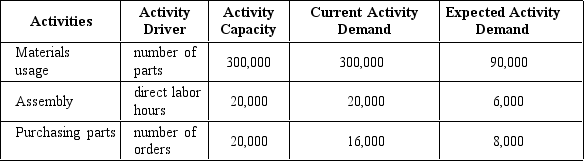
Free
(Multiple Choice)
4.8/5
(28)
Correct Answer:
B
Analyzing how costs and other financial factors vary as different bundles of activities are considered to strengthen a firm's strategic position is the process of
Free
(Multiple Choice)
4.9/5
(35)
Correct Answer:
A
The following transactions take place after the implementation of JIT:
1) Materials were purchased on account for $75,000.
2) Materials were placed into production.
3) Actual direct labor costs were $16,000.
4) Actual overhead costs were $30,000.
5) Conversion costs applied were $52,000.
6) All work was completed for the month.
7) All completed work was sold.
8) The variance is recognized.
Which of the following would NOT be an entry under the backflush system, assuming the second trigger point is the completion of goods?
Free
(Multiple Choice)
4.9/5
(34)
Correct Answer:
B
Laramie Company has a traditional, unit-based cost system. The Kansas City plant of Laramie produces eight different electronic products. Each year, 100,000 units of all products are produced. The demand for each product is about the same; thus, the average output for each product is 12,500 units. Although the products differ in complexity, each product uses about the same labor time and materials. The plant has used direct labor hours for years to assign overhead to products. The cost accounting department developed the following cost equation to help design engineers understand the assumed cost relationships. (The equation describes the relationship between total manufacturing costs and direct labor hours. The equation is supported by a coefficient of determination of 63 percent):
Y = $5,000,000 + $60X where X is the number of direct labor hours
The variable rate of $60 is broken down as follows:
Direct labor $19
Variable overhead 12
Direct materials 29
Because of competitive pressures, product engineering was asked to redesign products to reduce the total cost of manufacturing. Using the above cost relationships, product engineering adopted the strategy of redesigning to reduce direct labor content. As each design was completed, an engineering change order was cut, triggering a series of events such as design approval, vendor selection, bill of materials update, redrawing of schematic, test runs, changes in setup procedures, development of new inspection procedures, and so on.
After one year of design change, the normal volume of direct labor was reduced from 125,000 hours to 100,000 hours, with the 100,000 units being built. Although each product differs in its labor content, the redesign efforts reduced the labor content for all products. On average, labor content per unit of product dropped from 1.25 hours per unit to 1 hour per unit. Fixed overhead, however, increased from $5,000,000 to $6,000,000.
Required:
a. Using normal volume, compute the manufacturing cost per labor hour before the design changes. What is the cost per unit of an "average" product?
b. Using the normal volume after the one year of design changes, compute the manufacturing cost per hour. What is the cost per unit of an "average" product?
(Essay)
5.0/5
(36)
At which stage of the consumable life-cycle is price sensitivity low?
(Multiple Choice)
4.8/5
(35)
JIT manufacturing uses which of the following philosophies of quality control?
(Multiple Choice)
4.8/5
(32)
The difference between the sales price needed to capture a predetermined market share and the desired profit per unit is called:
(Multiple Choice)
4.8/5
(36)
The factor(s) that describe the relationships of a firm's value chain activities that are performed with its suppliers and customers is(are) called:
(Multiple Choice)
4.9/5
(35)
Strategic decision making is important to achieve good inventory control.
(True/False)
4.8/5
(36)
The stage during which the product loses market acceptance is called the:
(Multiple Choice)
4.8/5
(40)
The assignments to suppliers and customers that provide the best cost information needed are called assignments.
(Short Answer)
4.7/5
(32)
A firm that has implemented JIT had the following transactions:
1) Materials were purchased on account for $40,000.
2) Materials were placed into production.
3) Actual direct labor costs were $6,000.
4) Actual overhead costs were $40,000.
5) Conversion costs applied were $42,000.
6) All work was completed for the month.
7) All completed work was sold.
8) The variance is recognized.
What will be the entry to record materials placed into production using the backflush approach?
(Multiple Choice)
4.9/5
(34)
Figure 11-1
Ambrosia Corp. is a manufacturer of equipment used in manufacturing. It currently produces a product with 30 parts but through redesign has reduced the number of parts to 9. Then current activity capacity and demand for the 30 unit configuration and expected activity demand for the 9 part configuration are provided below:
Materials usage has a rate of $6 per part and no fixed costs. Assembly has a rate of $20 per labor hour with no fixed component. Purchasing requires clerks that can process 5,000 purchase orders. Each clerk earns $40,000 per year. There is also a $1 per order processing cost.
-Refer to Figure 11-1. What is the total cost reduction of the new design?
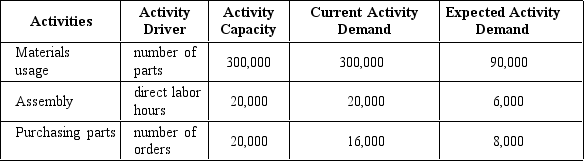
(Multiple Choice)
4.9/5
(36)
Which of the following manufacturing costs is assigned to products in JIT environment using direct tracing?
(Multiple Choice)
4.8/5
(40)
Which stage of the marketing life-cycle has slow sales growth with peak sales?
(Multiple Choice)
4.8/5
(37)
The time a product exists-from conception to abandonment is called the:
(Multiple Choice)
4.8/5
(32)
The viewpoint that describes the general sales pattern of a product as it passes through the introduction, growth, maturity, and decline stages is called the:
(Multiple Choice)
4.8/5
(33)
There are two general cost management strategies: cost leadership and focusing.
(True/False)
4.8/5
(29)
Prior to installing a JIT system, Clarendon Company used machine hours to assign maintenance costs to its three products of 6-inch, 8-inch, and 11-inch insulation. The maintenance costs totaled $400,000 per year. The machine hours used by each product and the quantity produced of each product are as follows:
After installing JIT, three manufacturing cells were created and the cell workers were trained to perform
Maintenance. Maintenance costs for the three cells still totaled $400,000; however, these costs are now traceable to each cell.
Cell, 6-inch $100,000
Cell, 8-inch 120,000
Cell, 11-inch 180,000
After installing JIT, the maintenance cost per roll of 6-inch insulation would be

(Multiple Choice)
4.8/5
(30)
The relationships among activities that are performed with a firm's portion of the value chain is(are) called:
(Multiple Choice)
4.8/5
(38)
Showing 1 - 20 of 148
Filters
- Essay(0)
- Multiple Choice(0)
- Short Answer(0)
- True False(0)
- Matching(0)