Exam 6: Managing Quality
Exam 1: Operations and Productivity134 Questions
Exam 2: Operations Strategy in a Global Environment145 Questions
Exam 3: Project Management131 Questions
Exam 4: Forecasting151 Questions
Exam 5: Design of Goods and Services136 Questions
Exam 6: Managing Quality139 Questions
Exam 7: Process Strategy and Sustainability141 Questions
Exam 8: Location Strategies149 Questions
Exam 9: Layout Strategies171 Questions
Exam 10: Human Resources, Job Design, and Work Measurement202 Questions
Exam 11: Supply-Chain Management152 Questions
Exam 12: Inventory Management178 Questions
Exam 13: Aggregate Planning144 Questions
Exam 14: Material Requirements Planning Mrp and Erp184 Questions
Exam 15: Short-Term Scheduling149 Questions
Exam 16: Lean Operations147 Questions
Exam 17: Maintenance and Reliability139 Questions
Exam 18: Decision-Making Tools107 Questions
Exam 19: Linear Programming110 Questions
Exam 20: Transportation Models104 Questions
Exam 21: Waiting-Line Models145 Questions
Exam 22: Learning Curves121 Questions
Exam 23: Simulation102 Questions
Exam 24: Supply Chain Management Analytics65 Questions
Exam 25: Sustainability in the Supply Chain11 Questions
Exam 26: Statistical Process Control166 Questions
Exam 27: Capacity and Constraint Management117 Questions
Select questions type
The Japanese use the term poka-yoke to refer to continuous improvement.
Free
(True/False)
4.9/5
(35)
Correct Answer:
False
ISO 9000 has evolved from a set of quality assurance standards toward a quality management system.
Free
(True/False)
4.8/5
(39)
Correct Answer:
True
How is source inspection related to employee empowerment?
Free
(Essay)
4.8/5
(41)
Correct Answer:
Source inspection involves the operator ensuring that the job is done properly. These operators are empowered to self-check their own work. Employees that deal with a system on a daily basis have a better understanding of the system than anyone else, and can be very effective at improving the system.
A cause-and-effect diagram helps identify the source of a problem.
(True/False)
4.8/5
(31)
Calculate the Quality loss function from the following information.
D2 = 2.1
C = $0.87
(Short Answer)
4.9/5
(36)
Which of the determinants of service quality involves having the customer's best interests at heart?
(Multiple Choice)
4.9/5
(35)
Create a Pareto Chart for the following mistakes made in grading an exam.
Cause Frequency Incorrect sum 35 Question marked wrong was right 3 Question marked right was wrong 4 Partial credit not consistent 58
(Essay)
5.0/5
(40)
When a sample measurement falls inside the control limits, it means that
(Multiple Choice)
4.8/5
(23)
A refrigeration and heating company-one that installs and repairs home central air and heating systems-has asked your advice on how to analyse their service quality. They have logged customer complaints. Here's a recent sampling. Use the supplied template to construct a conventional cause-and-effect diagram. Place each of the complaints onto a main cause; justify your choice with a brief comment as necessary. 1. "I was overcharged-your labour rates are too high." 2. "The repairman left trash where he was working." 3. "You weren't here when you said you would be. You should call when you must be late." 4. "Your repairman smoked in my house."5. "The part you installed is not as good as the factory original." 6. "Your repairman was here for over two hours, but he wasn't taking his work seriously." 7. "You didn't tighten some of the fittings properly-the system's leaking." 8. "Your estimate of repair costs was WAY off." 9. "I called you to do an annual inspection, but you've done more-work that I didn't authorize." 10. "Your mechanic is just changing parts-he doesn't have a clue what's really wrong." 11. "Your bill has only a total-I wanted to see detail billing." 12. "Your testing equipment isn't very new-are you sure you've diagnosed the problem?"13. "One of the workmen tracked mud into my living room." 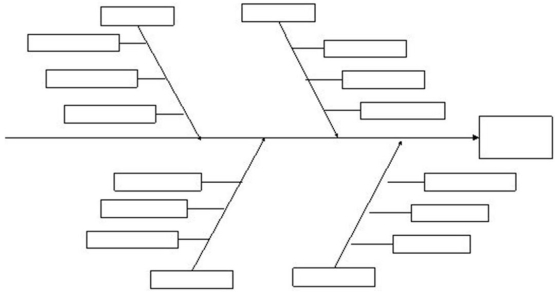
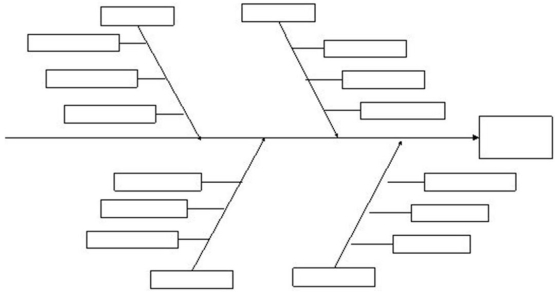
(Essay)
4.7/5
(40)
Calculate the Quality loss function from the following information.
D2 = 3.54
C = $2.61
(Short Answer)
4.8/5
(42)
Showing 1 - 20 of 139
Filters
- Essay(0)
- Multiple Choice(0)
- Short Answer(0)
- True False(0)
- Matching(0)