Exam 9: Inventory Management
Exam 1: Using Operations to Create Value115 Questions
Exam 2: Process Strategy and Analysis239 Questions
Exam 3: Quality and Performance198 Questions
Exam 4: Capacity Planning120 Questions
Exam 5: Constraint Management136 Questions
Exam 6: Lean Systems166 Questions
Exam 7: Project Management139 Questions
Exam 8: Forecasting150 Questions
Exam 9: Inventory Management205 Questions
Exam 10: Operations Planning and Scheduling149 Questions
Exam 11: Resource Planning124 Questions
Exam 12: Supply Chain Design77 Questions
Exam 13: Supply Chain Logistic Networks114 Questions
Exam 14: Supply Chain Integration120 Questions
Exam 15: Supply Chain Sustainability78 Questions
Exam 16: Supplement A Decision Making107 Questions
Exam 17: Supplement J Operations Scheduling123 Questions
Exam 18: Supplement K Layout39 Questions
Exam 19: Supplement B Waiting Lines111 Questions
Exam 20: Supplement C Special Inventory Models53 Questions
Exam 21: Supplement D Linear Programming87 Questions
Exam 22: Supplement E Simulation54 Questions
Exam 23: Supplement F Financial Analysis55 Questions
Exam 24: Supplement G Acceptance Sampling Plans87 Questions
Exam 25: Supplement H Measuring Output Rates108 Questions
Exam 26: Supplement I Learning Curve Analysis50 Questions
Select questions type
An assistant manager is reviewing the costs associated with the store's best-selling product. The data available follows.
Demand = 500 units/year
Order cost = $40/order
Holding cost = $7/unit/year
a. What is the EOQ and its associated ordering and holding costs?
b. If annual demand doubles and all other costs remain the same, what is the new EOQ and total annual cost?
Free
(Essay)
4.7/5
(37)
Correct Answer:
a.
Qopt units
Holding cost
Ordering cost
b.
Scenario 9.5
Tom Bergman, owner and operator of the Earplug Superstore, is reviewing the costs associated with the store's best-selling hearing aid, the BZ15. The data available to Dr. Bergman concerning this device follow.
Demand = 25 units/week
Order cost = $3/order
Holding cost = $1.50/unit/year
The Earplug Superstore operates 52 weeks a year.
-A neighborhood sportswear store sells a pair of Victoria sneakers for $40. Due to the recent fitness craze, these shoes are in high demand: 50 pairs of shoes are sold per week. The ordering cost is $20 per order, and the annual holding cost is 20% of the selling price. If the store operates 52 weeks a year, what can you say about the current lot size of 235?
Free
(Multiple Choice)
4.8/5
(30)
Correct Answer:
A
When considering reorder points and inventory position, if an item has an inventory position of 200 units, an order will be placed only if the reorder point is ________.
Free
(Short Answer)
4.9/5
(37)
Correct Answer:
less than or equal to 200 units
Consider the following conditions for an item used in the Hess Company's manufacturing process:
Which of the following statements best describes Hess's situation regarding inventory replenishment?
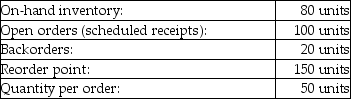
(Multiple Choice)
4.9/5
(29)
Consider the following conditions for an item used in the Hess Company's manufacturing process:
Which of the following statements best describes Hess's situation regarding inventory replenishment?
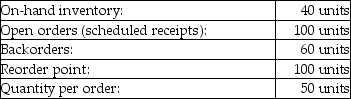
(Multiple Choice)
4.8/5
(31)
Scenario 9.8
A company operating under a continuous review system has an average demand of 50 units per week for the item it produces. The standard deviation in weekly demand is 20 units. The lead-time for the item is six weeks, and it costs the company $30 to process each order. The holding cost for each unit is $10 per year. The company operates 52 weeks per year.
-Use the information in Scenario 9.8. What is the desired safety stock level if the company has a policy of maintaining a 90% cycle-service level?
(Multiple Choice)
4.9/5
(31)
Scenario 9.11
Demand = 50,000 units/week
Standard deviation of weekly demand = 15,000 units
Average lead time = 8 weeks
Standard deviation of lead time: 3 weeks
Cycle-service level = 80%
A continuous review system is used to control inventory.
-Use the information in Scenario 9.11. If the firm decides to increase its cycle-service level to 90%, what is the new reorder point if all other parameters remain the same for this product?
(Multiple Choice)
4.7/5
(34)
Although lower inventories and a just-in-time approach receive considerable attention in the business media, some organizations prefer high levels of inventory. Why would they want to hold a large inventory?
(Essay)
4.9/5
(34)
What assumptions are made in calculating the economic order quantity? Which of these assumptions is the least realistic? Why?
(Essay)
5.0/5
(34)
In an ABC analysis, class ________ SKUs, which typically make up about ________% of the SKUs, account for about 80% of the dollar usage.
(Short Answer)
4.7/5
(29)
Scenario 9.4
The Mwongola Company is a small manufacturing company that uses gear assemblies to produce four different models of mountain bikes. One of these gear assemblies, the "Smooth Shifter", is used for the two most expensive of Burdell's four models, and has an estimated annual demand of 300 units. Burdell estimates the cost to place an order is $40, and the holding cost for each assembly is $60 per year. The company operates 250 days per year.
-Use the information in Scenario 9.4. The purchasing manager decides that, in order to save purchasing time, orders for the Smooth Shifter will be placed once a month, or twelve times per year. How much does this approach cost Mwongola in additional annual holding and ordering costs (instead of Mwongola ordering using the EOQ quantity)?
(Multiple Choice)
5.0/5
(32)
Scenario 9.1
Shipments of Product A from a distribution center to a retailer are made in lots of 350. The retailer's average demand for Product A is 75 units per week. The lead time from distributor to retailer is 3 weeks. The retailer pays for the shipments when they leave the distributor. The distributor has agreed to reduce the lead time to 2 weeks if the retailer will purchase quantities of 400 per shipment instead of 350 units per shipment.
-Refer to Scenario 9.1. With the change in purchased quantities, the average cycle inventory will:
(Multiple Choice)
4.9/5
(41)
________-demand items are items for which demand is influenced by market conditions and is not related to the inventory decisions for any other item held in stock.
(Short Answer)
4.9/5
(31)
Scenario 9.9
"Gollee those cats sure go through a lot of food," Geoff exclaimed as he saw the shopping list pad that had been pre-printed with the words "cat food" at the top. He pondered a different approach to shopping for the furry little darlings, reviewed his shopping records, and discovered the following. The price of cat food has held steady at 89 cents per can. Despite feigning indifference, each of the seven cats nibbles their way through an average of one can per day, three hundred sixty five days a year. The price of gasoline has held constant at $3.50 per gallon and his pickup uses a gallon each way to the cat food store. The cost to hold a can of cat food is 10% of the unit price.
-Use the information in Scenario 9.9 to determine the combined cost of goods and inventory if Geoff decides to follow the economic order quantity model?
(Multiple Choice)
4.9/5
(35)
Considering the EOQ model, a reduction in ordering costs justifies reducing the lot size ordered.
(True/False)
4.8/5
(41)
A stock-keeping unit (SKU) is a specially designed container for holding a specific amount of an inventory item somewhere along the supply chain.
(True/False)
4.8/5
(37)
Consider the following conditions for an item used in the Hess Company's manufacturing process:
What is Hess's inventory position for this item?

(Multiple Choice)
4.9/5
(32)
An experienced operations manager can tell at a glance whether an item should be classified as safety stock, anticipation inventory, or cycle stock.
(True/False)
4.9/5
(25)
The primary lever to reduce anticipation inventory is to place orders closer to the time when they must be received.
(True/False)
4.9/5
(30)
Showing 1 - 20 of 205
Filters
- Essay(0)
- Multiple Choice(0)
- Short Answer(0)
- True False(0)
- Matching(0)