Exam 13: Aggregate Planning
Exam 1: Operations and Productivity126 Questions
Exam 2: Operations Strategy in a Global Environment135 Questions
Exam 3: Project Management123 Questions
Exam 4: Forecasting142 Questions
Exam 5: Design of Goods and Services137 Questions
Exam 6: Managing Quality130 Questions
Exam 7: Process Strategy129 Questions
Exam 8: Location Strategies140 Questions
Exam 9: Layout Strategies161 Questions
Exam 10: Human Resources, Job Design, and Work Measurement191 Questions
Exam 11: Supply-Chain Management145 Questions
Exam 12: Inventory Management171 Questions
Exam 13: Aggregate Planning134 Questions
Exam 14: Material Requirements Planning Mrp and Erp172 Questions
Exam 15: Short-Term Scheduling139 Questions
Exam 16: Just-In-Time and Lean Options138 Questions
Exam 17: Maintenance and Reliability130 Questions
Exam 18: Statistical Tools for Managers97 Questions
Exam 19: Acceptance Sampling99 Questions
Exam 20: The Simplex Method of Linear Programming94 Questions
Exam 21: The Modi and Vam Methods of Solving Transportation Problems135 Questions
Exam 22: Vehicle Routing and Scheduling111 Questions
Exam 23 Managing Quality155 Questions
Exam 24: Process Strategy107 Questions
Exam 25: Supply-Chain Management73 Questions
Exam 26: Vehicle Routing and Scheduling92 Questions
Select questions type
Reddick's Specialty Electronics makes weatherproof surveillance systems for parking lots. Demand estimates for the next four quarters are 25, 9, 13, and 17 units. Prepare an aggregate plan that uses inventory, regular time and overtime and back orders. Subcontracting is not allowed. Regular time capacity is 15 units for quarters 1 and 2, 18 units for quarters 3 and 4. Overtime capacity is 3 units per quarter. Regular time cost is $2000 per unit, while overtime cost is $3000 per unit. Back order cost is $300 per unit per quarter; inventory holding cost is $100 per unit per quarter. Beginning inventory is zero.
The data inputs for this problem, and the optimal solution, generated by microcomputer software, appear below. Answer the following questions based on the scenario and the solution.
a. How many total units will be produced in quarter 1 for delivery in quarter 1?
b. How many units in total will be used to fill back orders over the four quarters?
c. What is the cost to produce one unit in Quarter 4 using overtime to deliver in quarter 1 (filling a back order)?
d. At the end of quarter 3, what is the ending inventory of finished systems?
e. What is the total cost of the solution?
f. What is the average cost per unit?
(Essay)
4.9/5
(32)
__________ involves capacity decisions that determine the allocation of classes of resources in order to maximize profit or yield.
(Short Answer)
4.7/5
(33)
Aggregate planning for fast food restaurants is very similar to aggregate planning in manufacturing, but with much smaller units of time.
(True/False)
4.8/5
(36)
Which of the following statements about aggregate planning is false?
(Multiple Choice)
4.7/5
(34)
The __________ strategy sets production equal to forecasted demand.
(Short Answer)
4.9/5
(43)
Which of the following actions is consistent with the use of pure level strategy?
(Multiple Choice)
4.7/5
(37)
Which of the following is not an advantage of level scheduling?
(Multiple Choice)
4.9/5
(36)
Which of the following is the term used for medium range capacity planning with a time horizon of three to eighteen months?
(Multiple Choice)
4.8/5
(29)
Eagle Fabrication has the following aggregate demand requirements and other data for the upcoming four quarters.
Which of the following production plans is better: Plan A-chase demand by hiring and layoffs; or Plan B-produce at a constant rate of 1200 and obtain the remainder from overtime?
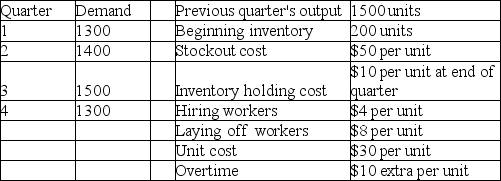
(Essay)
4.9/5
(41)
The management coefficients model is a formal planning model built around a manager's experience and performance.
(True/False)
4.8/5
(30)
A manufacturer of industrial seafood processing equipment wants you to develop an aggregate plan for the four quarters of the upcoming year using the following data on demand and capacity.
a. Find the optimal plan using the transportation method.
b. What is the cost of the plan?
c. Does any regular time capacity go unused? How much in what periods?
d. What capacity went unused in this solution (list in detail)?
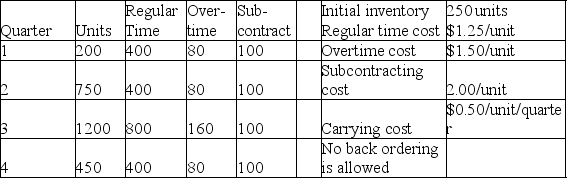
(Essay)
4.9/5
(31)
In aggregate planning, one of the adjustable elements of capacity is the extent of subcontracting.
(True/False)
4.9/5
(34)
The aggregate planning process usually includes expediting and dispatching of individual products.
(True/False)
4.7/5
(27)
__________ is the process of breaking the aggregate plan into greater detail.
(Short Answer)
4.8/5
(31)
Planning tasks associated with loading, sequencing, expediting, and dispatching typically fall under
(Multiple Choice)
4.9/5
(34)
Normally, the transportation model is used to solve problems involving several physical sources of product and several physical uses of the product, as in factories and warehouses. How is it possible to use the transportation model where the "routes" are from one time period to another? Describe how this provides aggregate planners with a usable mathematical model.
(Essay)
4.8/5
(36)
Byron's Manufacturing makes tables. Demand for the next four months and capacities of the plant are shown in the table below. Unit cost on regular time is $40. Overtime cost is 150% of regular time cost. Subcontracting is available in substantial quantity at $75 per unit. Holding costs are $5 per table per month; back orders cost the firm $10 per unit per month. Byron's management believes that the transportation algorithm can be used to optimize this scheduling problem. The firm has 50 units of beginning inventory and anticipates no ending inventory.
a. How many units will be produced on regular time in June?
b. How many units will be produced by subcontracting over the four-month period?
c. What will be the inventory at the end of April?
d. What will be total production from all sources in April?
e. What will be the total cost of the optimum solution?
f. Does the firm utilize the expensive options of subcontracting and back ordering? When; why?
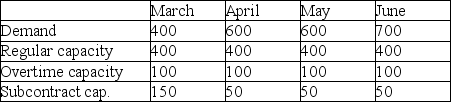
(Essay)
4.8/5
(37)
In level scheduling, what is kept uniform from month to month?
(Multiple Choice)
4.7/5
(34)
Identify (a) the demand options for aggregate planning; and (b) the capacity (supply) options for aggregate planning.
(Essay)
4.8/5
(34)
Showing 81 - 100 of 134
Filters
- Essay(0)
- Multiple Choice(0)
- Short Answer(0)
- True False(0)
- Matching(0)