Exam 14: The Sales and Operations Planning Process
Exam 1: Operations Management63 Questions
Exam 2: Quality Management71 Questions
Exam 3: Statistical Quality Control111 Questions
Exam 4: Product Design75 Questions
Exam 5: Service Design79 Questions
Exam 6: Processes and Technology61 Questions
Exam 17: Scheduling80 Questions
Exam 7: Capacity and Facilities83 Questions
Exam 8: Human Resources79 Questions
Exam 9: Project Management85 Questions
Exam 10: Supply Chain Management: Strategy and Design56 Questions
Exam 11: Global Supply Chain Procurement and Distribution69 Questions
Exam 12: Forecasting85 Questions
Exam 13: Inventory Management78 Questions
Exam 13: Operational Decision-Making Tools: Simulation22 Questions
Exam 14: Operational Decision-Making Tools: Linear Programming29 Questions
Exam 14: The Sales and Operations Planning Process76 Questions
Exam 15: Resource Planning82 Questions
Exam 16: Lean Systems79 Questions
Exam 18: Operational Decision-Making Tools: Decision Analysis38 Questions
Exam 19: Operational Decision-Making Tools: Acceptance Sampling28 Questions
Exam 20: Decision-Making Tools: Facility Location Models23 Questions
Exam 21: Operational Decision-Making Tools: Work Measurement31 Questions
Select questions type
Financial constraints are one of the major inputs of the sales and operations planning process.
Free
(True/False)
4.8/5
(36)
Correct Answer:
True
Reconciliation of the sales plan and the operations plan may include adjusting capacity and/or managing demand.
Free
(True/False)
4.9/5
(31)
Correct Answer:
True
The following information relates to a company's aggregate production planning activities:
Beginning Workforce = 50 workers
Production per Employee = 250 units per quarter
Hiring Cost = $1000 per worker
Firing Cost = $1,500 per worker
Inventory Carrying Cost = $15 per unit per quarter
If a level production strategy is used then the number of workers required is
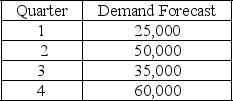
Free
(Multiple Choice)
5.0/5
(28)
Correct Answer:
B
Disaggregation is the process of breaking a sales and operations plan into more detailed plans.
(True/False)
4.9/5
(32)
The following information relates to a company's aggregate production planning activities:
Beginning Workforce = 50 workers
Production per Employee = 250 units per quarter
Hiring Cost = $1000 per worker
Firing Cost = $1,500 per worker
Inventory Carrying Cost = $15 per unit per quarter
If a chase demand strategy is used then the number of workers hired at the start of quarter 2 is
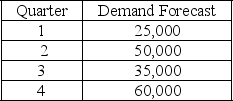
(Multiple Choice)
4.8/5
(33)
Given the information below,the number of available-to-promise units in period 1 is
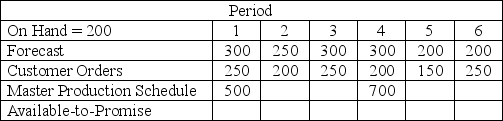
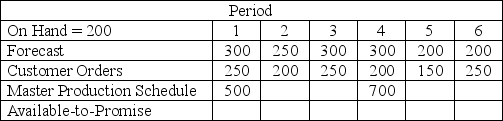
(Multiple Choice)
4.9/5
(35)
The following information relates to a company's aggregate production planning activities:
Beginning Workforce = 35 workers
Production per Employee = 1,250 units per quarter
Hiring Cost = $500 per worker
Firing Cost = $1,000 per worker
Inventory Carrying Cost = $20 per unit per quarter
If a level production strategy is used then the number of workers required for the plan is
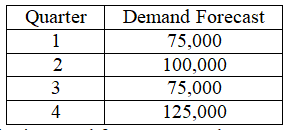
(Multiple Choice)
4.8/5
(41)
Subcontracting is a feasible alternative for adjusting capacity provided the supplier can reliably meet quality and time requirements.
(True/False)
4.9/5
(39)
A bagel company bakes a specialty bagel that it sells by the dozen every day.These specialty bagels can only be baked early in the morning before the store opens for business.The company estimates that the daily demand (in dozens)for its specialty bagel is distributed as follows:
Specialty bagels are sold by the dozen only at a cost of $9.00 per dozen.The cost to make one bagel is $0.50.Leftover specialty bagels are sold by the dozen the next day for a 50% discount.The bagel company's cost of overestimating demand,Co,is
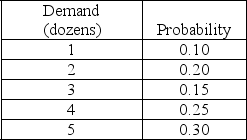
(Multiple Choice)
4.7/5
(29)
A company is developing a linear programming model for its aggregate production plan.If Wt = workforce size for period t,Ht = number of workers hired for period t,and Ft = number of workers fired for period t,then the company's workforce constraint for period 2 is
(Multiple Choice)
4.7/5
(39)
The following information relates to a company's aggregate production planning activities:
Beginning Workforce = 50 workers
Production per Employee = 250 units per quarter
Hiring Cost = $1000 per worker
Firing Cost = $1,500 per worker
Inventory Carrying Cost = $15 per unit per quarter
If a chase demand strategy is used then the number of workers fired at the start of quarter 3 is
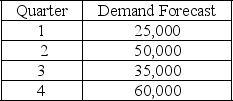
(Multiple Choice)
4.9/5
(45)
One of several strategies for managing demand is to shift it into other time periods using incentives,sales promotions,and advertising.
(True/False)
4.8/5
(41)
In capacity planning,the feasibility of the sales and operations production plan is verified by a
(Multiple Choice)
4.9/5
(32)
The following information relates to a company's aggregate production planning activities:
Beginning Workforce = 125 workers
Production per Employee = 500 units per quarter
Hiring Cost = $750 per worker
Firing Cost = $1,500 per worker
Inventory Carrying Cost = $10 per unit per quarter
If a chase demand strategy is used the number of workers fired in quarter 3 is
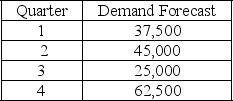
(Multiple Choice)
4.8/5
(32)
The following information relates to a company's aggregate production planning activities:
Beginning Workforce = 50 workers
Production per Employee = 250 units per quarter
Hiring Cost = $1000 per worker
Firing Cost = $1,500 per worker
Inventory Carrying Cost = $15 per unit per quarter
If a level production strategy is used then the total cost of the plan (hiring cost,firing cost and inventory carrying cost)is
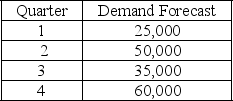
(Multiple Choice)
5.0/5
(39)
The primary cost associated with the level production strategy is the cost of
(Multiple Choice)
4.8/5
(30)
The following information relates to a company's aggregate production planning activities:
Beginning Workforce = 125 workers
Production per Employee = 500 units per quarter
Hiring Cost = $750 per worker
Firing Cost = $1,500 per worker
Inventory Carrying Cost = $10 per unit per quarter
If a level production strategy is used the number of units in inventory at the end of quarter 3 is
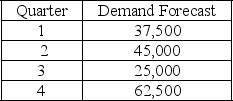
(Multiple Choice)
4.9/5
(32)
Overtime and undertime are common strategies for adjusting demand.
(True/False)
4.8/5
(37)
The following information relates to a company's aggregate production planning activities:
Beginning Workforce = 50 workers
Production per Employee = 250 units per quarter
Hiring Cost = $1000 per worker
Firing Cost = $1,500 per worker
Inventory Carrying Cost = $15 per unit per quarter
If a level production strategy is used then the required output per quarter is
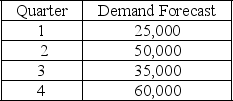
(Multiple Choice)
4.9/5
(35)
The following information relates to a company's aggregate production planning activities:
Beginning Workforce = 125 workers
Production per Employee = 500 units per quarter
Hiring Cost = $750 per worker
Firing Cost = $1,500 per worker
Inventory Carrying Cost = $10 per unit per quarter
If a chase demand strategy is used the total hiring and firing costs for the production plan is
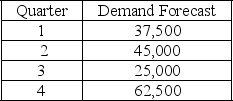
(Multiple Choice)
4.8/5
(33)
Showing 1 - 20 of 76
Filters
- Essay(0)
- Multiple Choice(0)
- Short Answer(0)
- True False(0)
- Matching(0)