Exam 13: Resource Management
Exam 1: Goods, Services, and Operations Management65 Questions
Exam 2: Value Chains68 Questions
Exam 3: Measuring Performance in Operations80 Questions
Exam 4: Operations Strategy65 Questions
Exam 5: Technology and Operations Management72 Questions
Exam 6: Goods and Service Design91 Questions
Exam 7: Process Selection, Design, and Analysis88 Questions
Exam 8: Facility and Work Design78 Questions
Exam 9: Supply Chain Design71 Questions
Exam 10: Capacity Management70 Questions
Exam 11: Forecasting and Demand Planning77 Questions
Exam 12: Managing Inventories89 Questions
Exam 13: Resource Management88 Questions
Exam 14: Operations Scheduling and Sequencing66 Questions
Exam 15: Quality Management72 Questions
Exam 16: Quality Control and Spc85 Questions
Exam 17: Lean Operating Systems63 Questions
Exam 18: Project Management63 Questions
Exam 19: Work Measurement, Learning Curves, and Standards57 Questions
Exam 20: Queuing Analysis38 Questions
Exam 21: Modeling Using Linear Programming44 Questions
Exam 22: Simulation38 Questions
Exam 23: Decision Analysis44 Questions
Select questions type
A cement company is considering how to expand its capacity and they are examining the use of overtime or subcontracting on a quarterly basis as possible options.They have the following information about their operation:
Aggregate demand = 30,000; 25,000; 27,000; and 31,000
Maximum capacity = 25,000 units
Labor standard = 2.45 hours/unit
Cost of overtime = $10.50/hour
Cost of subcontracting = $25.00/unit
a.What is the cost of overtime in quarter 1?
b.What is the total cost of subcontracting over four quarters?
Free
(Essay)
4.7/5
(39)
Correct Answer:
a.Costs of overtime and subcontracting:
Overtime = (5000)(2.45)($10.50) = $128,625
Subcontracting = (5000)($25.00) = $125,000
b.Subcontracting cost = $325,000.
A manufacturing company is interested in making a product structure tree for one of its major products.They know that product A is made up of assemblies B, C, and D.Each B assembly is made up of one raw material F, and 2 E parts.Each C assembly is composed of 2 G parts and one H subassembly.Each H sub?assembly is made up of 2 F raw materials, 2 1 parts and 2 J parts.
a.How many units of part G are needed to make one unit of product A?
b.How many units of raw material F are needed to make up one unit of product A?
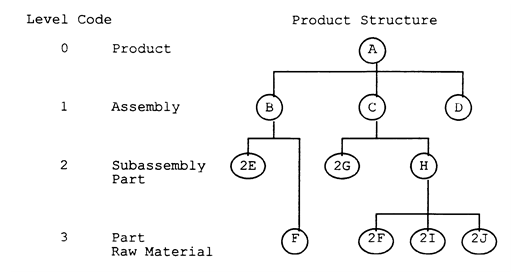
Free
(Essay)
4.9/5
(38)
Correct Answer:
a.2 parts G are in 1 assembly C which is in 1 product A
b.1 raw material F is in 1 assembly B which is in 1 product A, plus two raw materials F is in 1 subassembly H which is in 1 assembly C which is in 1 product A, for a total of 3 units of raw material F
Promotion of weekly discount airfares by an airline would be an example of ____.
Free
(Multiple Choice)
4.8/5
(43)
Correct Answer:
A
If forecast demand exceeds the total factory or supply capacity, managers might simply decide not to meet forecast demand.This decision would most likely be made at which planning level?
(Multiple Choice)
4.8/5
(35)
Assigning people to tasks, setting priorities for jobs and scheduling equipment fits best with which level of the generic framework for resource planning?
(Multiple Choice)
4.8/5
(36)
A sheet metal company has developed the following six-month production schedule (in thousands of square yards):
In addition, their monthly labor and machine capacities (in hours) available, and the production standards (in hours per square yard) are:
a.What is the percent utilization of the labor capacity in month 4?
b.What is the percent utilization of the machine capacity in month 3?
c.In how many weeks are the labor requirements over capacity?

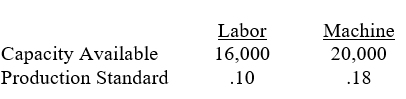
(Essay)
4.9/5
(40)
Service firms frequently take their aggregate plans and disaggregate them down to the execution level as detailed front-line staff and resources schedules, job sequences and service encounter execution.
(True/False)
4.9/5
(38)
The BOM for Product X is shown below, followed by a table of inventory data.The master production schedule quantity calls for the completion of 300 Xs in Week 7.The lead-time for production of X is 2 weeks and there are currently no units of X available.
a.When and what quantity will be the planned order release for Item C?
b.Determine the week and the quantity of the planned order release for Item D.
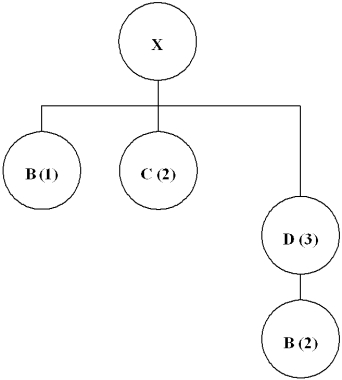
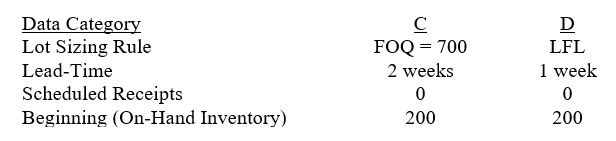
(Essay)
4.9/5
(29)
Aggregate planning and disaggregation methods in goods-producing industries involve fewer levels of planning than service-providing organizations, because service organizations deal with more than just materials.
(True/False)
4.9/5
(29)
Describe the options that managers have for developing aggregate plans to respond to fluctuating demand.
(Essay)
4.9/5
(34)
Short-term changes in facilities and equipment are seldom used in traditional aggregate planning methods because of the capital costs involved.
(True/False)
4.8/5
(42)
A metal shop currently has a work force of 20 people and is considering hiring four more people for the next three weeks only.The cost of hiring and training one person is $200 and the cost of terminating one person is $100.Each employee can produce 40 units/week on regular time and four units/week on overtime, and each person must be paid to produce 40 units even if the demand is not sufficient enough to keep everyone busy.The cost of producing one unit on regular time is $20 while on overtime it is $30.The cost of subcontracting one unit is $40.Demand for the next three weeks is 800 units, 1200 units, and 1000 units.Because there is no storage available the shop has a policy that no inventory is to be carried over from week to week.
a.What is the total cost for week 1 if there are only 20 workers?
b.What is the total cost for all three weeks using only 20 workers?
c.What is the total cost for week 1 if the company uses 24 workers?
d.What is the total cost for all three weeks using all 24 workers?
(Essay)
4.8/5
(35)
A company that makes construction equipment is exploring different lot sizing approaches to its MRP schedule: lot-for-lot (LFL), fixed order quantity (FOQ) using the EOQ, and period order quantity (POQ).It costs $100 to set up the production line to produce hydraulic jacks and the carrying cost per unit per week is $1.Annual demand is expected to be 1550 jacks.For planning purposes, the company uses a 50-week work year and disregards the effects of initial inventory and safety stock.The net requirements for hydraulic jacks for the next six weeks are:
a.Using a LFL approach, what is the lot size in week 3?
b.What is the total cost for the LFL method?
c.What is the Fixed order quantity (FOQ) using the EOQ approach?
d.What is the beginning inventory for week 5 using the FOQ approach?
e.What is the total cost using the FOQ method?
f.What is the period order quantity?
g.What is the ending inventory for week 4 using the POQ method?
h.What is the total cost using the POQ approach?

(Essay)
4.7/5
(28)
Resources include materials, equipment, facilities, information, technical knowledge and skills, and people.
(True/False)
4.7/5
(32)
Explain the three lot-sizing methods, and under what circumstances each work best:
a.Lot-for-Lot (LFL)
b.Fixed Order Quantity (FOQ)
c.Periodic Order Quantity (POQ)
(Essay)
4.8/5
(31)
The direct inputs to material requirements planning include all of the following except
(Multiple Choice)
4.7/5
(35)
Lot sizing rules on a parent item do not affect the gross requirements of all lower level component items.
(True/False)
4.8/5
(36)
A company currently has no items in inventory.The demand for the next four months is 200, 400, 250 and 350 units.Assuming a level production rate of 250 units per month, determine the month in which a backorder will materialize.
(Essay)
4.7/5
(32)
A company is interested in developing a quarterly aggregate production plan but they aren't sure if level capacity or matching demand would be better.They have the following information available regarding their production operation:
Number of working days per quarter = 65 days
Number of hours per day per person = 8 hours
Labor standard to produce one unit = 3 hours
Demand for four quarters respectively:
40,000, 42,000, 41,000, and 44,000 units
a.Using a level capacity plan, how many workers would be needed each quarter?
b.For a level capacity plan, what is the beginning inventory in quarter 2?
c.Using a level capacity plan, in how many quarters are the machine requirements over capacity?
d.Using a matching demand plan, how many workers are needed for quarter 1?
e.How many additional workers are needed in quarter 2 under a matching demand plan?
(Essay)
4.7/5
(34)
Showing 1 - 20 of 88
Filters
- Essay(0)
- Multiple Choice(0)
- Short Answer(0)
- True False(0)
- Matching(0)